Layout
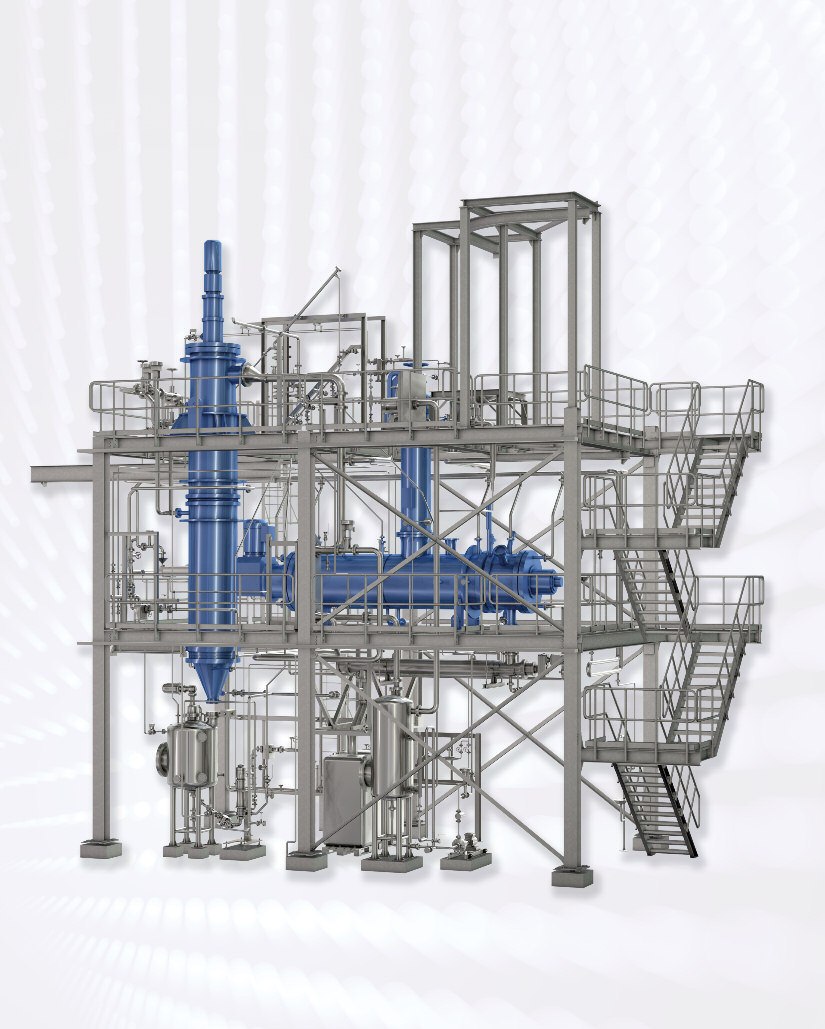
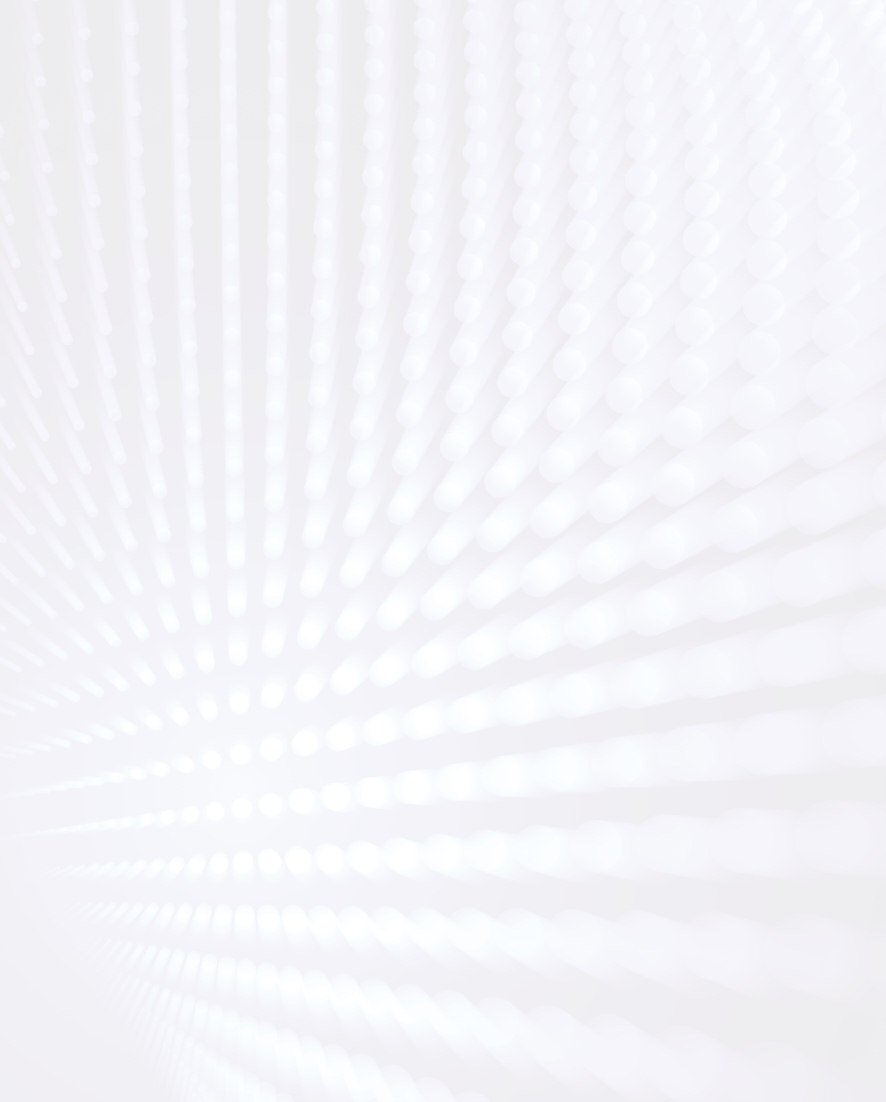
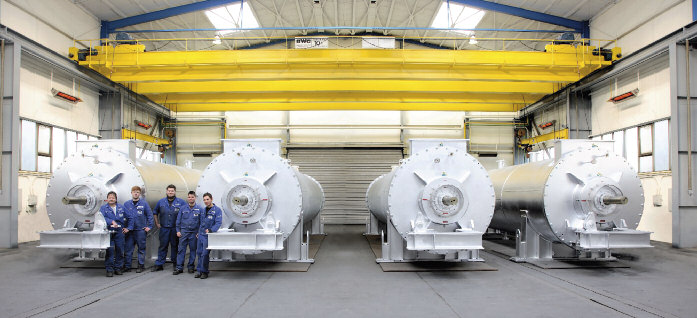
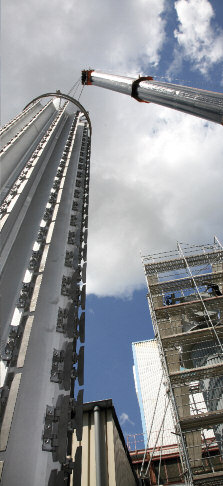
Buss-SMS-Canzler is a leading inter-
More than 500 dryers
national supplier of thermal separa-
tion solutions for difficult products
For more than 50 years we have sup-
and mixtures.
plied different types of dryers, adap-
We are the world's leading supplier
ted to a large variety of applications
of thin film evaporation technology,
throughout the world, currently more
this is due to the long-standing expe-
than 500 dryers. Based on our long-
rience of the three former companies
standing experience and supported
Luwa, SMS, Buss and Canzler. This
by lab and pilot tests, the specialists
long experience and expertise is now
at Buss-SMS-Canzler select the most
incorporated into Buss-SMS-Canzler.
suitable drying technology for your
For our customers around the world
application. Lab tests in our lab
we develop and manufacture machi-
equipment show general feasibility.
nes and plants for evaporation, pro-
Tests in our pilot plants provide the
cessing of highly viscous materials,
basis for the design of our dryers.
membrane filtration and drying. Our
These studies are not only carried out
experience and our test centre allow
upon our customers' request, but also
us to develop customer specific pro-
to investigate new applications on
cess solutions by applying tailor-made
our own development projects, as for
equipment and complete systems.
example the TDI recovery in the CFT
Buss-SMS-Canzler partners you as
dryer (page 12).
consultant, designer and manufactu-rer through all project stages: fromprocess layout, pilot tests, enginee-ring, mechanical design, manufactu-ring and documentation, to instal-lation, start up and after sales service.
CP dryer in outdoor test stand
Four horizontal thin film dryers for a Chinese customer
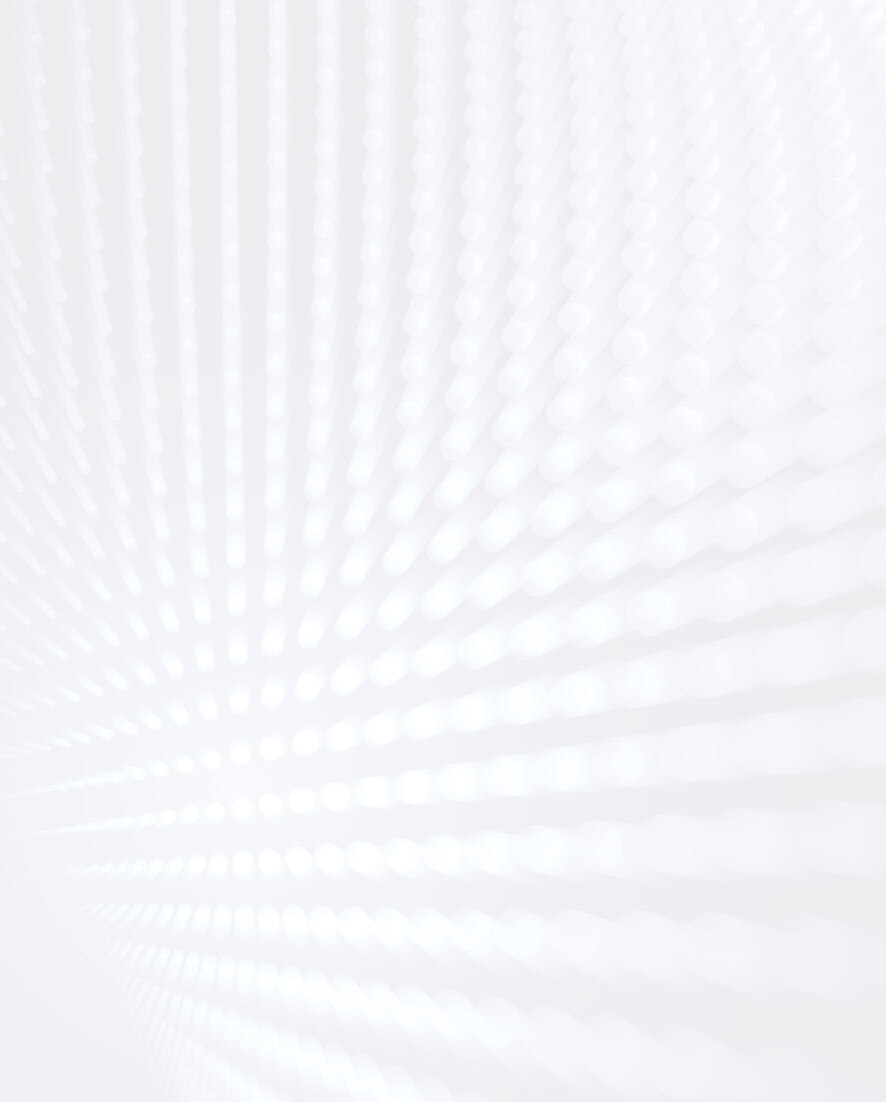
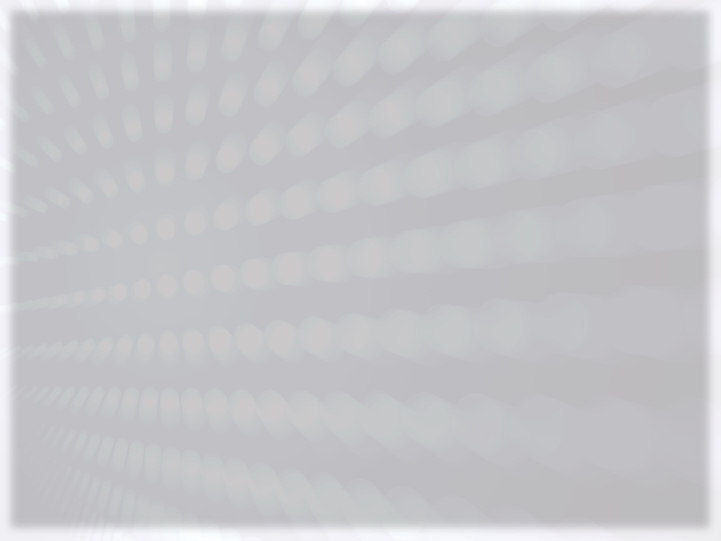
Drying Technology
at a Glance
The Buss-SMS-Canzler range of dry- Buss-SMS-Canzler offers a program of Vertical and horizontal thin film dryersers carries out the following process dryers using different operating prin- with thin product layers on the heatsteps: drying, cooling, heating, calci- ciples tailored to meet the individual exchange surface, the ROVACTOR®ning, reacting, mixing, sublimation process requirements when treating with specific paddles to convey lumpyand sterilisation.
products with particular characteris- wet feed, the REACTOTHERM® with
The product range covers heating tem- tics and specific drying behaviour.
self-cleaning hooks for sticky products
peratures of -20°C to 400°C, process
as well as the CFT dryer with its me-
pressures of 0,01 to 30 bar and resi-
chanically agitated fluid bed are tech-
dence times from seconds up to seve-
nically mature solutions for a large
variety of different drying applicati-ons.
CFT dryer
Heat transfer by
Pressure on process side
Product residence time
ce Mixing
p Desublimation
Suspension, Solution
rm Thixotropic paste
Sludge, hardly pumpable
ct fo
u Filter cake
d Wet powder
t p
e Very coarse (cm)
W Fibrous
r „Breaks up" in particles
io Pasty phase
a Sticky/viscous phase
e Crust forming
b Temperature sensitive
in Combustible, explosion risk
• suitable/applicable
• fairy suitable/case-to-case evaluation
C = Continuous operation
– not suitable/not used/not applicable
B = Batch operation

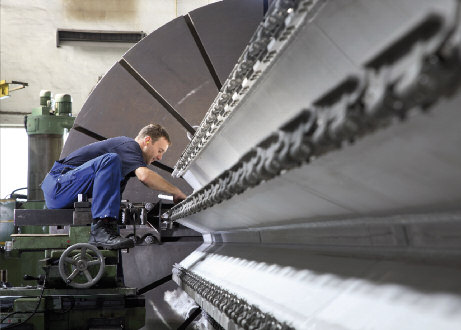
Vertical
Thin Film Dryers
Thin film dryers are characterised by duct passes typically through an eva- The volatile components driven out ofa mechanically agitated thin product poration zone, then a slurry or crystal- the product by heat, pass upwardlayer. The film thickness is normally in lisation zone and finally a powder through the dryer counter-current tothe range of less than one up to a few zone. Most of the liquid is removed in the product flow and are then conden-millimetres.
the evaporation and slurry zone while sed in an external condenser. The
In vertical thin film dryers the wet feed in the powder zone the surface mois- powder obtained at the bottom isis distributed over the heated wall by ture from the solid particles and some discharged continuously via a suitablea distributing ring and evenly applied of the internal moisture is driven off.
gaslock system. The total residence
to it in a thin film by hinged pendulum
time of the product is between 30 and
blades. Running downward the pro-
Manufacturing of CP rotor
• Agrochemicals (Atrozine etc.)
• Continuous processing of liquid and
• Waste water and spent liquors
pumpable products to get dry solids in
• Chlorides, bromides, sulfates
• Silane recovery
• Gentle treatment of products thanks to
• Benzosulfonic acid
short residence time and – if necessary
• Chemical intermediates
– operation under vacuum
• Solvent recovery from waste
• Fully enclosed design to treat explosive,
• Carbonates, phosphates
toxic and hazardous substances
• Silicon, silicon carbide
• Complete recovery of solvents
• Contact drying to ensure optimal
• Dyes and pigments
energy utilization
• Self-cleaning of heat exchange surface,
• Sodium formiate
hence a constant high heat transfer
• Baron carbide, baron nitride• Caffeine, condiments
Assembly of CP dryer
Horizontal
Thin Film Dryers
Horizontal thin film dryers are continu-
Vapours pass counter-currently to the
ously operated contact dryers and
product flow and leave the dryer close
used for a broad range of applications
to the feed nozzle. Entrained particles
of slurries, sludges, pastes, filter cakes,
under vacuum, atmospheric pressure
are removed in the wet zone.
• HEATING and COOLING of solids
and overpressure. They consist of a ho-
Moisture levels of a few tenth of a
• MELTING (Urea etc.)
rizontal externally heated shell with
percent up to 5% and more can be
end covers, the inlet and outlet nozzles
achieved. The residence time of the
for feed, vapour and final product,
product is typically between 5 and
of solids with liquids and subsequent thermal processes
nozzles for the heating medium and a
rotor with screwed on elements suppor-ted in external bearings. The wet pro-duct fed through the inlet nozzle is
conveyed steadily by the rotor ele-
• Continuous, fully enclosed processing
ments along the heated dryer wal in
• Short residence time, small product
a thin film, al owing an optimum heat
• Low energy consumption
transfer and a high evaporation per-
• Superior mixing efficiency
• Flexible through exchangeable
• Self-cleaning of heat exchange surface• Easy access
Transport of thin film dryer for food industry
• High heat transfer coefficient
Thin Film Dryer with pulled rotor
The Combi-Dryer from Buss-SMS- the high speed rotor. The pre-dried • Product loss is minimized due to theCanzler consists of a combination of a product falls from the drying zone of
compact arrangement
vertical dryer and a horizontal thin film the vertical dryer directly onto the • No intermediate storage or dryer. Special features of thin film con- rotor of the horizontal dryer. This rotor
conveying device is required
conveys the product in horizontal di-
between first and second drying
tact drying technology:
rection to the product outlet on the op-
• Gentle treatment of heat sensitive
posite side of the dryer.
• Different heating media as well as
products due to a short
The vapours of both dryers flow in
different temperature profiles can be
counter-current direction to the pro-
• Fully enclosed design to treat
duct, and then through the vapour
explosive, toxic and hazardous
nozzle of the vertical dryer into the Applications
next process stage.
The dryers are widely used throughout
• Continuous operation
the process industries to convert li-
• Small hold-up
Advantages of the
quids, slurries and pastes to free flo-
wing solids in continuous, single pass
• Entrained fine particles from the
The wet product is fed into the vertical
horizontal dryer are removed in the
dryer directly above the heating zone
top wet zone of the vertical dryer
The Combi-Dryer is applied for
and evenly spread as thin turbulent
film on the heat exchange surface by
• Dyes and pigments
• Optical whitener
• Polypropylene suspensions
• Organic and inorganic salts
• Polyethylene slurry
Industrial use of Combi-Dryer
The ROVACTOR® is an efficient con-
tact processor which provides a high
• Continuous enclosed processing of toxic,
local mixing effect for the treatment of
inflammable and explosive products
filter cakes, powders and pellets. The
• Uniform product temperature, processing
• Carbon, carbon black
ROVACTOR® consists of a cylindrical
of heat sensitive products
or trough shaped body and a hollow
• Contact drying with low energy
• Sodium chloride
agitator shaft fitted with special
• Low rotor speed: minimum dust
• Detergent additives
paddles in form of segmental discs.
production, minimal particle size
• Detergent intermediates
Heating or cooling is provided indi-
reduction, suitable for abrasive products
• Uranium oxide
rectly by means of steam or a transfer
• High heat transfer coefficient:
high throughput rates per unit
fluid via the segmented rotor discs
and the jacketed body.
• Polyvinyloxide
Continuous or batch processes under
• Terephthalic acid
vacuum, atmospheric pressure or
overpressure are possible. Product re-
sidence times can be adjusted in a
large range. The processor can be
easily protected against wear and
• Refinery sludge• Oil drilling sludge• Contaminated soil
Rotor of a ROVACTOR®
Large ROVACTOR®for drying solvent moist synthetics
The REACTOTHERM® is used for ther-mal processing of a wide variety ofpasty, viscous, fouling and lumpingproducts. It consists of a cylindrical,horizontal shell and a rotor with seg-mented discs and mixing bars. Statio-nary mixing hooks are attached tothe inside of the shell. The close clea-rance between the mixing hooks, thesegmented discs and the rotor resultsin a high mixing and kneading effectand largely self-cleaning properties ofthe rotor.
The inside of the shell is cleaned bymixing bars avoiding the fouling of
REACTOTHERM® for continuous operation
heat exchange surfaces and the for-mation of agglomerates. Shell, shaft
and discs can be heated or cooled.
• Self-cleaning heat exchange surfaces
Continuous or batch operation under
• Constant heat transfer with fouling
vacuum, atmospheric pressure and
overpressure is possible.
• Intensive mixing and kneading effect• Optimal heat/mass transfer with pasty
and sticky products
• Universal use for liquid, pasty and solid
• Several process steps in one machine
Applications
DRYING:
• Polymers
• Pharmaceutical intermediates
• Fine chemicals
• Food
• Dyes, optical brighteners
• Antioxidants
• Phosphate salts
• Surfactants
• Paint and varnish sludge
REACTIONS:
• Resorcinol
• Salicylic acid
• Benzoic acid
• Sodium cyanate
RESIDUE TREATMENT:
• Chemical waste with organic solvents
• Radioactive waste
Rotor of a REACTOTHERM®
CFT – Combi Fluidization
Technology
The main component of the Combi This technology can be used for many Many of the slurries and sludges oc-Fluidization Technology is the CFT different applications, as various hea- curing in the field of environmentaldryer. This dryer is filled with dry pro- ting methods are available and tem- protection, as e. g. paint and varnishduct, which is fluidized by the rotor. peratures up to approx. 600°C can sludges, can be processed under at-The wet product is fed into the hot be reached. The CFT dryer can be mospheric pressure. fluid bed and due to the movement of operated under vacuum or overpres- The Combi Fluidization Technologythe bed it is evenly distributed throug- sure.
also offers a very interesting alterna-
hout the dry product and dried effi-
tive with regard to cost and energy
demand compared to the spray dry-
The formation of sticky/viscous pha-
ing of products with sticky phases, if
ses, the direct contact of the wet feed
no specific properties and conditions
with the heat exchange surface and
of the dry product are required.
the consequential formation of crustsare avoided to a large extent.
The whole process is comparable toconventional drying with external re-flux system, but with the Combi Fluidi-zation Technology the externalmechanical work is no longer neces-sary. The vapour cleaning is integrated intothe drying room of the CFT dryer, sothat the vapours can be easily proces-sed in a condenser or rectifier.
CFT lab dryer
Combi Fluidization Technology twin pack
Salt Drying:
Efficiency by Combination
A very common drying application is
The composition of salt mixtures may
By combining dryers with different
the drying of salts and salt mixtures,
lead to operational malfunctions due
operating principles, such salt soluti-
to the formation of crusts. In particu-
ons can be processed very efficiently,
• in natural sources
lar, if salt mixtures contain compo-
e.g. a salty solution from the flue gas
• in down gradients of chemical
nents like sodium sulphate, hard
scrubber can be largely dehydrated
crusts may form on the heat ex-
in a vertical CP dryer. The residual
• as product from the neutralization
change surface. At best these crusts
moisture of the product from the first
plant of the flue gas scrubber
only reduce the performance of the
step is removed in the CFT dryer, thus
• as residue from membrane proces-
dryer, but if the worst comes to the
combining a dryer with a very high
ses for drinking water abstraction
worst the whole system may shut
evaporation performance with a
dryer, which safely avoids the forma-tion of crusts. This reduces the designsize and improves the operational re-liability.
CFT for salt drying
Environmental Protection Worldwide:
Sludge Drying Process
Municipal sludge is increasingly ap- These are typical applications, where These advantages resulted in moreplied as valuable product, as the di- the Buss-SMS-Canzler drying process than 100 sludge drying installationsrect agricultural use will be more can show its advantages with an eva- worldwide, with some being in ope-restrictive in the future. Industrial slud- poration performance between 0.2 ration for more than 25 years.
ges have to be incinerated in most and 8 tons of water per hour. The thincases, so that the pre-drying or full film dryer is characterized by:drying of sludges from municipal as • Single pass operation over the well as industrial plants is a manda-
sticky or pasty phase; hence
tory process step in many cases. The
no back mixing of dried product
following drying degrees can be clas- • Low energy consumptionsified:
• Self-cleaning heat exchange surface• Self-inertisation by evaporated
• 35 to 50% dry solid content prior
• Low operating and maintenance
to incineration in fluidized bed
Transport of sludge dryer
• 65 to 75% dry solid content prior
to composting or incineration with garbage
Full drying to 85 to 95%
dry solid content
• prior to using as solid fuel for
cement kilns or coal fired power stations, for pyrolisis, gasification or other conversion processes
• prior to composting, agricultural use
and soil reclamation
Sludge dryer with pulled rotor
Sludge drying plant in USA
TDI Recovery:
CFT Dryer for Economic Processes
Toluolene-2, 4-diisocyanate is the However, the realization of this reco- In the CFT dryer with its mechanicallybasis for a large variety of products very process is a demanding applica- agitated fluid bed the wet product islike glue, soft foams for upholstery tion. As soon as the content of free TDI evenly dispersed so that materials,and mattresses, shoe soles, varnishes in the residue reduces to approx. which pass viscous, pasty, sticky, crustfor the automotive industry, planes 17%, the concentrated residue beco- forming or crystallizing phases duringand trains. 90% of the worldwide pro- mes highly viscous and sticky and sud- drying, can be processed. The opera-duction of TDI is used in the pro- denly solidifies. Therefore a processor ting principle of the CFT dryer offersduction of polyurethane, a foamed used for the TDI recovery must avoid a simple and economic treatment ofsynthetics used in many applications. the blocking of the system with solids. the TDI residue, which could be de-During the TDI production process a Fluidized bed dryers, which disperse monstrated in our pilot test centre inlarge amount of distillation residue, the residue into the fluid bed or con- Pratteln, Switzerland. The treated re-which contains 30 to 70% free TDI, is tact dryers in robust design with high sidue was continuously dis- chargedgenerated. Therefore it is crucial for drive torque for the conveying ele- by gravitation into a cooler. The over-the overall profitability of the TDI pro- ments are possible solutions, but result all mass balance confirms – 100%duction process to recover the TDI in high operating and/or investment TDI recovery.
from this residue. As the TDI recovery costs. Therefore Buss-SMS-Canzleris a comparably complex process GmbH developed the TDI recovery instep, different processes have been the Combi Fluidization Technologydeveloped for the TDI recovery:
(CFT) dryer.
• Chemical/physical separation with
liquid-liquid extraction
• Chemical transformation with
reaction to toluene diamine
• Thermal separation by evaporation
The thermal separation by evapora-tion including drying allows a 100%recovery of the TDI from the residueand therefore is accepted as state-of-the-art technology.
Final product
TDI recovery process
Drying of Terephthalic Acid:
ROVACTOR® in Long-term Failure Free
Operation
Terephthalic acid is the feed product transparent, free flowing powder. Thisfor the manufacturing of PET, which is drying application is very demandingused in large quantities to produce for the process equipment, due to re-bottles, foils and textile fibres. The an- latively high process temperatures bet-nual production worldwide is more ween 180°C and 200°C and thethan 40 million tons of PET, produced large size of the processors. The highfrom the monomers ethylene glycol mechanical strain causes fatigueand terephthalic acid. This shows the cracks in the welding seams, whichimportance of PET as a material, are one of the main reasons for ope-which is used in large quantities for rational malfunctions. Based on a de- Rotor for terephthalic acid dryermany different applications.
tailed analysis of the causes for thedamages on terephthalic acid dryers,
For the industrial production of tereph- Buss-SMS-Canzler adjusted the designthalic acid various processes have of its segmented disc dryer RO-been established. The different pro- VACTOR®, so that the welding seamscesses have in common that the reac- can permanently cope with suchtion to produce the terephthalic acid strain. As a result our dryers haveis realized in a solution, which means been in continuous operation for al-the terephthalic acid needs to be most ten years without any damage.
dried to obtain the final product, a
Transport of ROVACTOR® for drying terephthalic acid
Pharmaceutical Industry:
CONTIVAC for Unchanged Product Quality
The CONTIVAC NDP processor was
Batch operated dryers have problems
developed by Buss-SMS-Canzler for
with products, which pass through a sti-
• Combination of different basic
use in production processes with spe-
cky, viscous phase during drying.
operations in one machine (no transport
cial hygienic requirements. This proces-
Such cases require very long residence
problems, no contamination of product)
sor combines the advantages of con-
• Very short residence time
times, which can cause unwanted side-
tinuous thin film drying with a special
(minimum thermal damage to product,
reactions, thermal damage to the pro-
high flow rates)
rotating spray nozzle that al ows for
duct, and/or colour changes.
• Very low hold-up
CIP cleaning. The individual y adjusta-
Experience has proven that the resi-
(little waste with product changes)
ble heating and cooling zones in the
dence time in the CONTIVAC NDP pro-
thin film dryer open up new opportuni-
cessor can be reduced up to 500 times.
ties for thin film drying technology to be
Further advantages compared to batch
used in complex processes.
systems result from the low investment
The basic operations of mixing, re-
and operating costs.
acting, flashing and drying can be car-
• Pharmaceutical intermediates
The design of the CONTIVAC NDP pro-
ried out in the same machine, with
cessor complies with the relevant GMP
several different substance streams
being fed into the processor simultane-
Shaft sealing and bearings are con-
structed compatible with pharmaceuti-
The CONTIVAC NDP processor offers
cal requirements (e.g. cartridge con-
manufacturers in the pharmaceutical,
fine chemical industries and in the foodand pet food industries new possibili-ties for improvement, which are notavailable with conventional batch ma-chines.
Rotor detail
Assembly of CONTIVAC
Low Risk Investment Decision:
Your test centre for new developments
Pilot tests are the best way
We make the process, instrumenta-
We operate worldwide and are
to find the right investment
tion and control design for plant sta-
active in the most important markets.
ges and individual components as
Your local contacts guarantee the fast
In Pratteln, Switzerland, we operate
well as the machine design for the
handling of your inquiry and arrange
a well equipped pilot plant. Process
core components, which are mainly
short-term competent advice.
conditions can be easily modified to
reach optimized test results. With theparameters from the test results the
Complete service quality
process and plant engineering can
We take care of the delivery to the
start, all under the responsibility of
site of destination, the installation or
one project manager.
the supervision of the installation on
• Physical definition
To find a suitable dryer for your ap-
site as well as the final inspection.
• Ionic chemical analysis
plication the following procedures
Our process engineers plan and su-
have proven their value:
pervise start up, test run, optimization
• General examination of drying
of your plant as well as training of the
behaviour of product
operating personnel. We also offer
• Liquid determination
• Drying tests with small product
service and maintenance contracts
• Inorganic chemical
samples in lab dryers to examine
for preventive maintenance.
general feasibility of our dryers
Spare parts are available on short
• Drying tests in our pilot plants to
call and are shipped once they have
• Gas-liquid-reaction
obtain engineering parameters
passed our quality control.
• Chromatography
These procedures provide the neces-
We offer the automation, optimiza-
sary information depending on the
tion or modification of our equipment
project stage.
and plants throughout their entireoperating life.
Our test report provides our
customers with:
• Documentation of the test
• Description of the test results• Analysis of the product samples
Professional project realization
from one source
We accompany and consult you from
the product idea to the optimized
quality production. We develop cus-
tomized process solutions for the ther-
mal separation or concentration of
substance mixtures.
entur-nogeaerbw •210 2
Head Office & Workshop
Branch Office & Test Center
Buss-SMS-Canzler GmbH
Buss-SMS-Canzler GmbH
Buss-SMS-Canzler GmbH
Kaiserstraße 13-15
Hohenrainstraße 10
Am Langen Graben 7
CH-4133 Pratteln 1
Phone: +49 60 33 - 85 - 0
Phone: +41 61 82 - 56 - 869
Phone: +49 24 21 - 705 -1
Fax: +49 60 33 - 85 - 249
Fax: +49 24 21 - 705 - 80
Source: http://www.exportpages.al/pdf.aspx?0754dbf0-9037-469b-adb5-f7604699afaf
Suivi : Famille "Horace" -Génération 1 : INC Horace x INC Téquila (pages 2-3) -Génération 2 : 2A : CHR Lutine x CHR Clafouti (pages 4-5) 2B : CHR Nesquik x IND Cotón (pages 6-7-8) 2C : CHR Nesquik x CAT Pizzly (pages 9-10) -Génération 3 : 3B : RMM Smarties x RTD Ethan (pages 11-12-13) -Génération 4 : 4B : RMM Kenya x INC Charlie (pages 14-15-16)
XLVets Fact Sheet Reprduction & Fertility RF The Oestrus Cycle MISSED HEATS Detection of oestrus or heat Heat detection and involves being able to observe and record behaviour associated with cycling. The most reliable sign is dealing with problems observing a standing response when ridden. There are various