Pii: s0266-3538(00)00101-9
Composites Science and Technology 60 (2000) 2037±2055
Sisal ®bre and its composites: a review of recent developments
Yan Li, Yiu-Wing Mai *, Lin Ye
Centre for Advanced Materials Technology (CAMT), Department of Mechanical & Mechatronic Engineering J07,
The University of Sydney, Sydney, NSW 2006, Australia
Received 4 December 1998; received in revised form 4 April 2000; accepted 19 April 2000
Sisal ®bre is a promising reinforcement for use in composites on account of its low cost, low density, high speci®c strength and
modulus, no health risk, easy availability in some countries and renewability. In recent years, there has been an increasing interest
in ®nding new applications for sisal-®bre-reinforced composites that are traditionally used for making ropes, mats, carpets, fancy
articles and others. This review presents a summary of recent developments of sisal ®bre and its composites. The properties of sisal
®bre itself, interface between sisal ®bre and matrix, properties of sisal-®bre-reinforced composites and their hybrid composites have
been reviewed. Suggestions for future work are also given. # 2000 Elsevier Science Ltd. All rights reserved.
Keywords: B. Electrical property; B. Interface; B. Mechanical property; B. Surface treatment; Ageing; Degradation; Natural±®bre composite; Sisal
mostly extracted from the periphery of the leaf. They
have a roughly thickened-horseshoe shape and seldom
Sisal ®bre is one of the most widely used natural ®bres
divide during the extraction processes. They are the most
and is very easily cultivated. It has short renewal times
commercially useful of the sisal ®bre. Ribbon ®bres occur
and grows wild in the hedges of ®elds and railway tracks
in association with the conducting tissues in the median
[1]. Nearly 4.5 million tons of sisal ®bre are produced
line of the leaf. Fig. 1 shows a cross-section of a sisal leaf
every year throughout the world. Tanzania and Brazil
and indicates where mechanical and ribbon ®bres are
are the two main producing countries [2].
obtained [3]. The related conducting tissue structure of
Sisal ®bre is a hard ®bre extracted from the leaves of
the ribbon ®bre gives them considerable mechanical
the sisal plant (Agave sisalana). Though native to tropi-
strength. They are the longest ®bres and compared with
cal and sub-tropical North and South America, sisal
mechanical ®bres they can be easily split longitudinally
plant is now widely grown in tropical countries of
during processing. Xylem ®bres have an irregular shape
Africa, the West Indies and the Far East [3]. A sketch of
and occur opposite the ribbon ®bres through the con-
a sisal plant is shown in Fig. 1 and sisal ®bres are
nection of vascular bundles as shown in Fig. 2. They are
extracted from the leaves.
composed of thin-walled cells and are therefore easily
A sisal plant produces about 200±250 leaves and each
broken up and lost during the extraction process.
leaf contains 1000±1200 ®bre bundles which is com-
The processing methods for extracting sisal ®bres
posed of 4% ®bre, 0.75% cuticle, 8% dry matter and
have been described by Chand et al. [2] and Mukherjee
87.25% water [1]. So normally a leaf weighing about
and Stayanarayana [1]. The methods include (1) retting
600 g will yield about 3% by weight of ®bre with each
followed by scraping and (2) mechanical means using
leaf containing about 1000 ®bres.
decorticators. It is shown that the mechanical process
The sisal leaf contains three types of ®bres [3]:
yields about 2±4% ®bre (15 kg per 8 h) with good
mechanical, ribbon and xylem. The mechanical ®bres are
quality having a lustrous colour while the retting pro-
cess yields a large quantity of poor quality ®bres. After
extraction, the ®bres are washed thoroughly in plenty of
* Corresponding author. Tel.: +61-2-9351-2290; fax: +61-2-9351-
clean water to remove the surplus wastes such as chlor-
E-mail address:
[email protected] (Yiu-Wing Mai).
ophyll, leaf juices and adhesive solids.
0266-3538/00/$ - see front matter # 2000 Elsevier Science Ltd. All rights reserved.
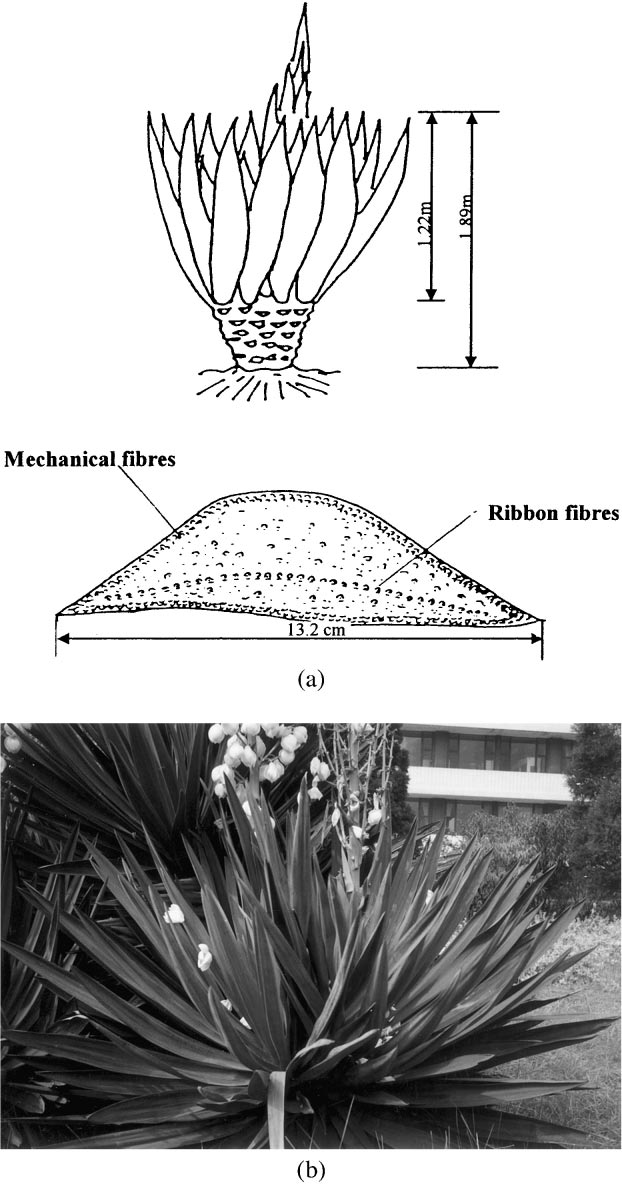
Y. Li et al. / Composites Science and Technology 60 (2000) 2037±2055
Fig. 2. Cross-section of a ribbon-®bre bundle.
reinforced with spirally oriented cellulose in a hemi-cel-
lulose and lignin matrix. So, the cell wall is a composite
structure of lignocellulosic material reinforced by helical
micro®brillar bands of cellulose. The composition of the
external surface of the cell wall is a layer of lignaceous
material and waxy substances which bond the cell to its
adjacent neighbours. Hence, this surface will not form a
strong bond with a polymer matrix. Also, cellulose is a
hydrophilic glucan polymer consisting of a linear chain
of 1, 4-b-bonded anhydroglucose units [9] and this large
amount of hydroxyl groups will give sisal ®bre hydro-
philic properties. This will lead to a very poor interface
between sisal ®bre and the hydrophobic matrix and very
poor moisture absorption resistance.
Though sisal ®bre is one of the most widely used nat-
ural ®bres, a large quantity of this economic and
renewable resource is still under-utilised. At present,
sisal ®bre is mainly used as ropes for the marine and
agriculture industry [1]. Other applications of sisal ®bres
Fig. 1. (a) A sketch of sisal plant and the cross-section of a sisal leaf
[3]; (b) photograph of a sisal plant.
include twines, cords, upholstery, padding and mat
making, ®shing nets, fancy articles such as purses, wall
The chemical compositions of sisal ®bres have been
hangings, table mats, etc. [10]. A new potential applica-
reported by several groups of researchers [4±7]. For
tion is for manufacture of corrugated roo®ng panels
example, Wilson [4] indicated that sisal ®bre contains
that are strong and cheap with good ®re resistance [11].
78% cellulose, 8% lignin, 10% hemi-celluloses, 2%
During the past decade (1987±1998), the identi®cation
waxes and about 1% ash by weight; but Rowell [5]
of new application areas for this economical material
found that sisal contains 43±56% cellulose, 7±9% lignin,
has become an urgent task. The use of sisal ®bre as a
21±24% pentosan and 0.6±1.1% ash. More recently,
reinforcement in composites has raised great interest
Joseph et al. [6] reported that sisal contains 85±88%
and expectations amongst materials scientists and engi-
cellulose. These large variations in chemical composi-
neers. The major studies on sisal ®bres carried out dur-
tions of sisal ®bre are a result of its dierent source, age,
ing this 10-year period can be broadly divided into the
measurement methods, etc. Indeed, Chand and Hashmi
following topics:
[7] showed that the cellulose and lignin contents of sisal
vary from 49.62±60.95 and 3.75±4.40%, respectively,
. Properties of sisal ®bres: Mechanical, thermal and
depending on the age of the plant.
dielectric properties of sisal ®bre have been studied
The length of sisal ®bre is between 1.0 and 1.5 m and
in detail. X-ray diraction, IR, TG, SEM, DSC,
the diameter is about 100±300 mm [8]. The ®bre is actu-
DMA, etc., have been used to determine the char-
ally a bundle of hollow sub-®bres. Their cell walls are
acteristics of sisal ®bre and provide theoretical
Y. Li et al. / Composites Science and Technology 60 (2000) 2037±2055
support for processing and application of this
ulus per unit cost), it (41.67 GPakg/$) is almost the best
next to jute (43.33 GPakg/$) amongst all the synthetic
. Interface properties between sisal ®bre and matrix:
and cellulosic ®bres.
The main purpose here is to modify the ®bre-
surface structure by using chemical and thermal
treatment methods in order to enhance the bond
strength between ®bre and matrix and reduce
Generally, the strength and stiness of plant ®bres
water absorption of sisal ®bre.
depend on the cellulose content and the spiral angle
. Properties of sisal-®bre-reinforced composites: The
which the bands of micro®brils in the inner secondary
matrix used in sisal-®bre-reinforced composites
cell wall make with the ®bre axis. That is, the structure
include thermoplastics (polyethylene, polypropylene,
and properties of natural ®bres depend on their source,
polystyrene, PVC, etc.), thermosets (epoxy, polye-
age, etc. [12]. The tensile properties of sisal ®bre are not
ster, etc.), rubber (natural rubber, styrene±buta-
uniform along its length [3]. The root or lower part has
diene rubber, etc.), gypsum and cement. The
low tensile strength and modulus but high fracture
eects of processing methods, ®bre length, ®bre
strain. The ®bre becomes stronger and stier at mid-
orientation, ®bre-volume fraction and ®bre-sur-
span and the tip has moderate properties.
face treatment on the mechanical and physical
Table 2 shows the properties of sisal ®bres as reported
properties of sisal-®bre-reinforced composites have
by dierent researchers. Note that except for the struc-
been studied. Also, several theoretical models are
ture and properties of the natural ®bre itself, experi-
given to predict the properties of the composites.
mental conditions such as ®bre length, test speed, etc.,
. Sisal/glass-®bre-reinforced hybrid composites: To
all have some eects on the properties of natural ®bres
take advantage of both sisal and glass ®bres, they
have been added conjointly to the matrix so that
Mukherjee and Satyanarayana [1] studied the eects
an optimal, superior but economical composite
of ®bre diameter, test length and test speed on the ten-
can be obtained. The hybrid eect of sisal/glass
sile strength, initial modulus and percent elongation at
®bres on the mechanical properties have been stu-
the break of sisal ®bres. They concluded that no sig-
died and explained.
ni®cant variation of mechanical properties with change
in ®bre diameter was observed. However, the tensile
Papers published between 1987 and 1998 related to
strength and percent elongation at the break decrease
sisal ®bres are listed in Table 1. It can be seen that
while Young's modulus increases with ®bre length. With
research interest has changed from the ®bre itself to
increasing speed of testing, Young's modulus and tensile
sisal-®bre-reinforced composites and hybrid composites.
strength both increase but elongation does not show
The study of interface between sisal ®bre and matrix,
any signi®cant variation. However, at a test speed of
however, remains an important topic.
500 mm/min, the tensile strength decreases sharply.
These results have been explained in terms of the inter-
nal structure of the ®bre, such as cell structure, micro-
2. Properties of sisal ®bre
®brillar angle (20±25), defects, etc. In rapid mechanical
testing, the ®bre behaves like an elastic body, i.e. the
crystalline region shares the major applied load result-
ing in high values of both modulus and tensile strength.
Compared to synthetic ®bres, the price of sisal ®bre
When the testing speed decreases, the applied load will
(0.36 US$/kg) is very low [3]. It is about one-ninth of
be borne increasingly by the amorphous region. How-
that of glass ®bre (3.25 US$/kg) and one-®ve hundredth
ever, at very slow test speeds, the ®bre behaves like a
of carbon ®bre (500 US$/kg). For speci®c price (mod-
viscous liquid. The amorphous regions take up a major
Number of papers published in the period (1987±1998) related to sisal ®bresa
Properties of sisal ®bres
6 [15±17,20±22]
Interface between sisal ®bre and matrix
Properties of sisal-ibre composites
13 [3,11,34±37,54, 57±59,61,62,64]
11 [26,32,33,42±44, 51±53,55,56]
Sisal/glass hybrid composites
a Data taken from Compendex (Computerised Engineering Index).
Y. Li et al. / Composites Science and Technology 60 (2000) 2037±2055
Properties of sisal ®bres reported by dierent researchers
Density (kg/m3) Moisture content (%) Tensile strength (MPa) Tensile Modulus (GPa) Maximum strain (%) Diameter (mm) Reference
portion of the applied load giving a low ®bre modulus
shows the results of sisal ®bres of dierent age at dif-
and a low tensile strength. But at very high strain rates
ferent temperature.
(500 mm/min), the sudden fall in tensile strength may
For electrical applications, the dielectric properties of
be a result of the presence of imperfections in the ®bre
sisal ®bre at dierent temperature and frequency have
causing immediate failure.
also been studied [16]. Increase of frequency decreases
In Ref. [1], the micro®brillar angle and number of
the dielectric constant "0 value, while increase of tem-
strengthening cells in the sisal ®bres did not show any
perature increases "0 at all frequencies. Increasing the
appreciable variation in ®bre diameter. Hence, no
plant age shifts the dissipation factor ( tan ) peak to
appreciable change in values of Young's modulus and
higher temperature. These phenomena were explained
tensile strength were observed. As the test length
on the basis of structural changes. Water absorbed by
increases, the number of weak links or imperfections
sisal ®bres has OHÿ anions which act as dipoles. Other
also increases, thus resulting in reduction in tensile
than OHÿ anions, there are several impurities and ions
strength. However, with increasing ®bre length, sisal
on the ®bre. These dipoles and ions contribute to the "0
oers a higher resistance to applied stress as a result of
and tan behaviours of sisal ®bres. At low frequencies,
the involvement of more oriented cellulosic ®bres. This
high "0 and tan values in sisal ®bre are caused by the
probably also accounts for the higher modulus of the
dipolar contribution of absorbed water molecules. "0
®bres at longer test lengths. The reason for such beha-
values at intermediate frequencies are the result of con-
viour by the characteristics of natural ®bres such as
tributions from space charge polarisation. At high fre-
multi-cellular structures, visco-elastic nature and non-
quencies, the contribution of polarisation of absorbed
uniform structural inhomogeneity.
water molecules and space charge decreases and elec-
Chand et al. [12] reported the eects of testing speed
tronic and atomic polarisation becomes operative.
and gauge length on the mechanical properties of other
Increase in temperature aects the mobility of ions and
kinds of natural ®bres (sun-hemp ®bres). Their results
consequently changes the ionic contributions. The tem-
support the ®nding of Ref. [1], though the magnitudes
perature dependence of the dielectric behaviour of sisal
are much lower than those of sisal ®bres. (For example,
®bre is shown in Fig. 3.
when the gauge length is 50 mm and testing speed is 50
Yang et al. [17] used IR, X-ray diraction and TG to
mm/min, the tensile strength of sisal ®bre is 759 MPa.
study the eect of thermal treatment on the chemical
However, for sun-hemp ®bre, the tensile strength is only
structure and crystallinity of sisal ®bres. They concluded
that the IR spectrum did not change below 200C
The mechanical properties of sisal ®bres obtained
treatment while density and crystallinity increased. This
from dierent age at three dierent temperature were
means that the chemical structure of sisal ®bres will not
investigated by Chand and Hashmi [15]. The tensile
change below 200C while the degree of crystallinity can
strength, modulus and toughness (de®ned as energy
be increased and hence the density. There was a slight
absorption per unit volume) values of sisal ®bre
weight loss (2%) below 200C probably caused by the
decrease with increasing temperature. The relative eect
evaporation of water absorbed by sisal ®bres, sub-
of plant age on these mechanical properties is less pro-
stances of low boiling point and others that can be
minent at 100C than at 30C. This is attributed to the
decomposed below this temperature. However, the large
more intense removal of water and/or other volatiles (at
amounts of cellulose, semi-cellulose and glucans were
100C) originally present in the ®bres, which otherwise
not lost. Also, they found that thermal decomposition
act as plasticising agents in the chains of the cellulose
of sisal ®bre could be divided into three stages. The
macromolecules. It is, however, noted that at 80C both
thermal behaviours are essentially identical for heat
tensile strength and modulus decrease with age of the
treatment between 150 to 200C. Hence, thermal treat-
plant. This trend is dierent to testing at 100C. Table 3
ment of sisal ®bre can be carried out below 200C.
Y. Li et al. / Composites Science and Technology 60 (2000) 2037±2055
Comparisons of mechanical properties of sisal ®bres with dierent age at dierent temperature [15]
Toughness per unit volume (MJ/m3)
Tensile strength (MPa)
Tensile modulus (GPa)
Results of TG of treated and untreated sisal ®bresa,b
t1 (C) w1 (%) t2(C) w2 (%) t3 (C) w3 (%)
150C/4 h treated
200C/0.5 h treated 61
a Three-stage thermal decomposition [17].
b ti ith stage decomposition temperature; wi ith stage percentage
weight remnant.
able levels by better wetting and chemical bonding
between ®bre and matrix.
3.1. Treatment of sisal ®bre surface
Most previous studies were focused on ®bre-surface
treatment methods and the resultant eects on the phy-
sical and mechanical properties of dierent ®bre-matrix
composite systems. But what will happen to the ®bres
after being treated? Several investigators [20±22] have
studied the surface morphology, mechanical and degra-
dation properties of the treated ®bres.
Fig. 3. Variation of (a) dielectric constant "0 and (b) dissipation factor
Yang et al. [20] studied the relationship of surface
tan with temperature in 2-year-old plant ®bres [17].
modi®cation and tensile properties of sisal ®bres. Their
modi®cation methods include: alkali treatment, H2SO4
treatment, conjoint H2SO4 and alkali treatment, benzol/
Table 4 shows the TG results of untreated and heat-
alcohol dewax treatment, acetylated treatment, thermal
treated sisal ®bres.
treatment, alkali-thermal treatment and thermal-alkali
treatment. The results are summarised in Table 5.
Thermal treatment (at 150C for 4 h) seems to be the
3. Interface modi®cations
most desirable method in terms of strength and mod-
ulus properties because of the increased crystallinity
Interfaces play an important role in the physical and
(from 62.4% for untreated to 66.2% for 150C/4 h
mechanical properties of composites [18,19]. The
treated) of sisal ®bres. When the temperature reaches
hydroxyl groups which occur throughout the structure
200C, the tensile properties will drop greatly as a result
of natural ®bres make them hydrophilic, but many
of the degradation of ®bres. Other treatments increase
polymer matrices are hydrophobic so that sisal-polymer
the ductillity of sisal ®bres substantially but decrease the
composites have poor interfaces. Also, the hydrophilic
sisal ®bres will absorb a large amount of water in the
To improve the moisture-resistance, Chand et al.
composite leading to failure by delamination. Adequate
acetylated sisal ®bre and studied its tensile strength [23].
adhesion across the interface can be achieved at desir-
It was shown that acetylation could reduce the moisture
Y. Li et al. / Composites Science and Technology 60 (2000) 2037±2055
. Coupling agent 3:
Eect of treatment methods on tensile properties of sisal ®bres [20]
Treatment methods Tensile strength Tensile modulus Elongation
Acetic acid+alkali
. Coupling agent 4:
content from 11 to 5.45%. However, the tensile strength
of acetylated sisal ®bre was reduced from 445 to 320
MPa caused by the loss of the hemi-cellulose in the ®bre
during acetylation.
Surface modi®cation of sisal ®bre using coupling
agents was also studied by Singh et al. [24]. Sisal ®bres
were cut into short lengths (6 cm) and washed with dis-
tilled water to remove water solubles from the ®bre
surface completely. After being air-dried they were
The hydroxyl groups attached to the glucose units of
heated to 80C for 8 h to remove excess surface moist-
the cellulose will react with these coupling agents in the
ure. Then these ®bres were treated by dipping into the
presence of moisture by substituting the right part of the
coupling-agent solution and stirring slowly for 0.5 h.
dashed lines shown on the chemical structures of the
After that, the treated ®bres were washed with solvent
coupling agents.
to remove compounds not covalently bonded to the
The eects of these coupling agents on the moisture
®bres and then kept at 80C in an oven for 4 h to con-
content in sisal ®bre are obtained and discussed. It is
stant weight.
clear that moisture absorption of surface-treated ®bres
The four coupling agents used were: N-substituted
has been reduced signi®cantly by providing hydro-
methacrylamide (coupling agent 1); gamma-methacry-
phobicity to the surface via long-chain hydrocarbon
loxypropyl trimethoxy silane (coupling agent 2); neo-
attachment. In addition, these coupling agents penetrate
the cell wall through surface pores and deposit in the
(coupling agent 3); and neopentyl(diallyl)oxy, triacryl
inter®brillar regions and on the surface, restricting fur-
zironate (coupling agent 4). Their chemical structures
ther ingress of moisture.
and possible interactions with sisal are as follows:
3.2. Treatment of ®bre/matrix interfaces
. Coupling agent 1:
To make good use of sisal-®bre reinforcement in
composites, ®bre-surface treatment must be carried out
to obtain an enhanced interface between the hydrophilic
sisal ®bre and the hydrophobic polymer matrices.
Modi®cations of interfaces between sisal ®bre and
polyester, epoxy, polypropylene, etc., have been studied.
Both mechanical and moisture absorption resistance
properties can be improved. These results are described
in the following sub-sections.
. Coupling agent 2:
3.2.1. Sisal/polyester composites
The properties of sisal-®bre-reinforced polyester
composites can be improved when sisal ®bres were sui-
tably modi®ed with surface treatment [24]. The mod-
i®cation methods have been discussed in Section 3.1.
In the work by Singh et al. [24], it was explained that
the modi®ed interphase' is much less sti than the resin
Y. Li et al. / Composites Science and Technology 60 (2000) 2037±2055
matrix and provides a deformation mechanism to reduce
3.2.2. Sisal/epoxy composites
interfacial stress concentration [25]. Further, it may also
For the interface between sisal ®bres and epoxy,
prevent ®bre/®bre contacts, hence removing the sources
Bisanda and Ansell [8] adopted silane treatment meth-
of high stress concentrations in the ®nal composites.
ods to improve the adhesion and moisture resistance
The eect of ®bre-surface treatment on the mechan-
properties. The ®bres were ®rst dewaxed in 2000 ml
ical properties under wet environment has also been
solution of benzene and alcohol (methylated spirit), ratio
studied in [24]. The results in Fig. 4 clearly show that by
1:1, by soaking batches of about 200 g of sisal ®bres,
improving interfacial adhesion the moisture-induced
300 mm long, in a sealed glass vessel. The ®bres were
degradation of composites can be reduced. Treated ®bre
soaked for 24 h, rinsed in alcohol and distilled water.
composites absorb moisture at a slower rate than the
These ®bres were then mercerized by soaking in a 0.5 N
untreated counterparts, probably because of the forma-
solution of sodium hydroxide, for about 72 h, rinsed in
tion of a relatively more hydrophobic matrix interface
distilled water and dried.
region by co-reacting organo-functionality of the cou-
To study the moisture resistance of composites, the
pling agents with the resin matrix. Though signi®cant
®bres were treated using silane that had been diluted to
reductions in tensile strength (30±44%) and ¯exural
5% in methylated spirits. A 0.1 M solution of ceric
strength (50±70%) were observed for both untreated
ammonium nitrate (CAN) was used as catalyst. The
and surface-treated sisal composites (Table 6 and Fig.
®bres were treated in batches by soaking about 150 g of
4), the strength retention of surface treated composites
the mercerized ®bres in 1500 ml of the silane/CAN
is higher than that of composites containing untreated
solution (2:1), for about 24 h at room temperature. The
sisal ®bres. Fig. 4 also shows that N-substituted metha-
®bres were then rinsed in distilled water and dried.
crylamide treated sisal-®bre-reinforced polyester compo-
The reaction mechanisms are as follows. First, silane
sites generally exhibit better mechanical properties under
reacts with water to form a silanol and an alcohol:
dry and wet conditions. It should, however, be noted in
Table 6 that with sisal ®bres treated by N-substituted
methacrylamide and silane have relatively lower void
NH2
CH23Si
OC2H53 3H2O
contents compared to other ®bre-treated composites.
HO3Si
CH23NH2 3
C2H5OH
Then, in the presence of moisture, the silanol reacts
with the hydroxyl groups attached to the glucose units
(G) of the cellulose molecules in the cell wall, thereby
bonding itself to the cell wall with further rejection of
NH2
CH23Si
OH3 H2O GOH
NH2
CH23Si
OH2OG 2H2O
It is found that the treatment of sisal ®bres in silane,
Fig. 4. Eect of wet environment on tensile strength of sisal/polyester
preceded by mercerization, provides improved wettabil-
composites (®bre content 50 vol.%) for 35 days: 1, untreated; 2, N-
substituted methyacrylamide treated; 3, silane treated; 4, titanate
lity, mechanical properties and water resistance of sisal-
treated; 5, zirconate treated. RH, relative humidity [24].
epoxy composites. The results are shown in Table 7.
Eect of surface treatments of sisal ®bres on the properties of sisal/polyester compositesa [24]
Zirconate treated
methacrylamide treated
Tensile strength (MPa)
Tensile modulus (GPa)
Energy to break (MJ/m2) 105
Flexural strength (MPa)
Flexural modulus (GPa)
a Fibre content 50 vol%.
Y. Li et al. / Composites Science and Technology 60 (2000) 2037±2055
Mechanical and physical properties of sisal/epoxy compositesa [8]
Compressive strength
Flexural strength
Water absorbed (%)
a Fibre volume fraction: 0.4.
Mercerization has greatly improved resin pick-up, or
initially alkali treated and then grafted with vinyl acid in
wettability, of the ®bres because of the increase in den-
an acid medium under N2 atmosphere with a grafting
sity of the composite. It is believed that, by providing
rate of 5.7%. The mechanical behaviour, water-resis-
additional sites of mechanical interlocking, this treat-
tance and ¯exible fracture morphology of short sisal/
ment leads to improvement of interfacial bonding,
phenol formaldehyde composites have all been mea-
hence promoting resin/®bre interpenetration at the
sured. The results show that cohesiveness between rigid
interface. The high hydrophobic resin pick-up could
sisal ®bre and brittle phenol formaldehyde can be
also account for the reduction in water absorption and
improved when sisal ®bre is treated with silane so that
hence improved mechanical properties under wet con-
the mechanical properties of the composites can be
increased. Water-resistance of the composites can be
Though treatment of sisal ®bres in silane preceded by
improved after being treated by grafting and silane
mercerization produces very little change in the
mechanical properties of dry composites, mechanical
performance of wet composites, and hence water resis-
3.2.4. Sisal/polyethylene composites
tance, can be improved. The treatment in 100% silane
Owing to the increasing use of thermoplastics, sisal
produces ®bres that are almost hydrophobic. This may
®bre reinforced-thermoplastics have become increas-
be a result of improved interfacial bonding arising from
ingly important. Joseph et al. [6] reported the eect of
the use of the silane. Water molecules at the interface
chemical treatment on the tensile properties of short-
tend to replace the resin-®bre covalent bond by weaker
sisal-®bre reinforced-polyethylene (PE) composites (both
hydrogen bonds, hence silane plays an important role in
randomly and unidirectionally oriented) and analysed
reducing water absorption in cellulosic-®bre-reinforced
the mechanisms of dierent treatment methods.
The treatment methods and their mechanisms are:
Sisal ®bres have a central hollow region, the lumen,
which gives access to water penetration by capillarity,
a. Alkali treatment: Alkali treatment can remove
especially when composites have high ®bre content. So,
natural and arti®cial impurities and produce a
although silane treatment can create a hydrophobic
rough surface topography. In addition, alkali
®bre surface, it is not possible to prevent water from
treatment leads to ®bre ®brillation, i.e. breaking
entering the composite by capillary action, as long as
down the ®bre bundle into smaller ®bres. This
the ®bre ends are exposed. It is recommended that, for
increases the eective surface area available for
practical purposes, it may be necessary to seal o the
wetting by the matrix resin. Hence, increasing the
external surfaces by water-repellents so as to keep water
®bre aspect ratio caused by reduced ®bre diameter
uptake in the composite to a minimum.
and producing a rough surface topography oer
better ®bre/matrix interface adhesion and increase
3.2.3. Sisal/phenol formaldehyde composites
in mechanical properties.
Yang et al. [26] using NaOH, silane (3-aminopropyl-
b. Isocyanate treatment: The hydrophilic nature of
triethoxy silane), chemical grafting and thermal treat-
sisal ®bres can be reduced by treating the ®bres
ment methods studied the eects on sisal/phenol
surface with urethane derivative of cardanol
formaldehyde composites. Alkali and thermal treatment
(CTDIC) because of the linkage of the long chain
methods have already been discussed in Section 3.1 [20].
structure of CTDIC to the cellulosic ®bres. This
For silane treatment, the ®bre was ®rstly treated by
makes sisal ®bres compatible with the PE matrix,
alkali and then immersed in the silane alcohol solution.
thus resulting in a strong interfacial bond between
After that, it was air-dried and followed by heating at
these two constituents with improved mechanical
100C. While for chemical grafting the sisal ®bre is
Y. Li et al. / Composites Science and Technology 60 (2000) 2037±2055
c. Peroxide treatment: The function of peroxide
. Sisal-®bre-reinforced thermosets
treatment is that it can graft PE on to the cellulose
. Sisal-®bre-reinforced thermoplastics
surface. The grafting reaction is a result of the
. Sisal-®bre-reinforced rubbers
peroxide-initiated free radical reaction between the
. Sisal-®bre-reinforced cement and gypsum
PE matrix and cellulose ®bres as shown below:
The number of papers published since 1987 are listed
in Table 8. It is shown that the most widely used matrix
RO: PE-H ! ROH PE:
for sisal-®bre-reinforced composites has changed from
gypsum and cement to rubber and polyethylene. Ther-
RO: Cellulose-H ! ROH Cellulose:
mosetting matrices such as epoxy and polyester have
also been used for sisal-®bre-reinforced composites.
PE: Cellulose: ! PE-Cellulose
4.1. Sisal-®bre-reinforced thermoset matrices
The tensile strength of the composites increases with
peroxide concentration up to a critical level depending on
The most widely used thermosetting matrix reinforced
the ®bre content and then remains constant. The exis-
by natural ®bres is polyester [27±30]. Compression
tence of a critical concentration of peroxide suggests that
moulding is the most widely used and convenient
the peroxide-initiated grafting reactions terminate when
method to make these composites, whether the ®bre is
the ®bres are covered with grafted PE and excess peroxide
long or short. The tensile and impact properties of this
causes some crosslinking of the PE molecules themselves.
kind of composites have been obtained by Sanadi et al.
d. Permanganate treatment: Permanganate is thought
It is shown that the tensile strength and elastic mod-
to induce grafting reactions between sisal ®bres
ulus of the composites containing up to 40% ®bre-
and PE matrix [6]. Joseph et al. have attempted to
volume fraction (Vf) increase linearly with Vf in good
explain the initiating graft copolymerisation but
agreement with the rule of mixtures. The work of
the conditions for this to occur are quite critical
fracture, as determined by Izod impact test, also
and cannot be ful®lled easily. (It is also dicult to
increases linearly with Vf. Analysis of the energy-
justify the di-valency of H in reactions given in
absorption mechanisms during impact fracture shows
[6].) Instead, oxidisation between permanganate
that ®bre pull-out and interface fracture are the major
and sisal ®bre will take place. So, the mechanism
contributors to the high toughness of these composites.
for improvement of the interfacial properties by
This result indicates that sisal ®bres have potential to
permanganate treatment is that the permanganate
produce inexpensive materials with high toughness.
roughens the ®bre surface and produces mechan-
Comparison of the impact properties of dierent nat-
ical interlocks with the matrix. Hence, the inter-
ural ®bre-reinforced composites, including sisal, pine-
facial bonding between permanganate treated sisal
apple, banana and coir shows that sisal-®bre composites
®bre and matrix is improved.
possess the highest impact toughness owing to the opti-
mal micro-®brillar angle of the ®bre (21 for sisal, 12
The permanganate concentration used is a critical
factor for the mechanical properties of the composite. It
is observed that the tensile strength reaches a maximum
Number of papers related to sisal ®bres published in the period (1987±
at a permanganate concentration of 0.055% and then
decreases sharply with further increase in permanganate
1987±1990 1991±1994 1995±1998
concentration. This is caused by the degradation of cel-
lulosic ®bres at high permanganate concentration.
Tensile properties of these sisal/PE composites with
[6, 44,51±52,67±68]
dierent treatment methods were compared. It appears
that the increase in properties as a result of these treat-
ments are in the order: DCP (dicumyl peroxide)
4. Properties of sisal-®bre-reinforced composites
According to the types of matrices used in sisal-®bre-
reinforced composites, they can be divided into the
following categories:
a Data taken from Compendex (Computerised Engineering Index).
Y. Li et al. / Composites Science and Technology 60 (2000) 2037±2055
for banana, 14 for pineapple and 45 for coir). It has
of these composites rather than sisal-®bre-reinforced
been proven by Gordon and Jeronimidis [31] that the
thermosets. Such properties include mechanical, envir-
toughness of composites increases with the micro-
onmental, electrical and dynamic.
®brillar angle of the ®bres and reaches a maximum at
15±20. It will then decrease with increasing angle. The
4.2.1. Processing methods
optimal micro-®brillar angle of sisal ®bre (21) leads to
The mixing methods so far used are: melt mixing and
better impact resistance with a work of fracture of 98.7
solution mixing. In melt mixing, the ®bre is added to a
KJ/m2 when the ®bre-volume fraction is 50%. For the
melt of thermoplastics and mixing is performed using a
same volume fraction of pineapple ®bres, this is 79.5
mixer at a speci®ed temperature and speed for a speci-
KJ/m2; for banana and coir ®bres, they are 51.6 and
®ed time. Then the mix is taken out from the mixer
43.5 KJ/m2, respectively. When compared to synthetic
while hot and is extruded using an injection moulding
®bre composites, the speci®c impact work of fracture
machine as long and thick rods.
for the natural ®bre composites is not much worse. The
In the solution mixing method, the ®bres are added to
speci®c work of fracture (ie toughness per unit density)
a viscous solution of thermoplastics in a solvent in a
of 60% volume fraction sisal ®bre/polyester composites
stainless-steel beaker with a stainless-steel stirrer. The
is 115 KJ mÿ2/g, while for ultra-high-modulus poly-
temperature is maintained for some time and the mix
ethylene (UHMPE) and E-glass ®bres, these values are
transferred to a ¯at tray and kept in a vacuum oven to
125 and 165 KJ mÿ2/g, respectively.
remove the solvent. The solution-mixing procedure
Rong et al. studied the eect of ®bre pre-treatment
avoids ®bre damage that normally occurs during blend-
and water absorption on the impact properties of sisal
ing of ®bre and thermoplastics by melt-mixing [34].
®bre reinforced polyester and epoxy matrices [32,33].
Generally, randomly oriented sisal-®bre-reinforced
Three ®bre-surface treatment methods including alkali
composites are prepared by standard injection moulding
treatment, coupling agent treatment and heat treatment
of the blends. Oriented sisal composites are processed
were used. They indicated that ®bre-surface treatment
by aligning the long extruded rods with compression
has a strong eect on the impact behaviour of the com-
posites and the eects are dierent for dierent matri-
Polyethylene is the most widely used thermoplastics
ces. It is observed that ®bre pull-out is the major
matrix [34±37]. For other natural ®bre composites,
contributor to the energy absorption. Increased ®bre-
polypropylene is also a major matrix material [38±41].
tensile strength promoted by thermal treatment can
Recently, sisal ®bre-reinforced polystyrene and PVC
increase the impact performance of the composites.
have also been studied [42,43].
Water absorption in sisal ®bre composites is mainly
caused by the ®bres and leads to a very poor interface
4.2.2. Properties of sisal ®bre reinforced polyethylene
between the sisal ®bre and the matrix. Dierent matrix
4.2.2.1. Mechanical properties. Joseph et al. [35] studied
systems have dierent interface characteristics. Gen-
the tensile properties of short sisal ®bre/polyethylene
erally, water absorption in sisal/polyester composite is
composites in relation to processing methods and the
two to three times that in sisal/epoxy composite and this
eects of ®bre content, length and orientation (see
leads to their dierent impact properties. For sisal/epoxy
Tables 9 and 10). As expected, the tensile properties
composite, the impact strength improves with water
show a gradual increase with ®bre length reaching a
absorption as a result of an acceptable level of interface
maximum at about 6 mm (12.5 MPa) and then decrease
debonding, but for sisal/polyester composites, the impact
(e.g. 10.24 MPa at 10 mm). Unidirectional short ®bres
strength decreases through the complete destruction of
achieved by extrusion enhance the tensile strength and
the interface.
elastic modulus of the composites along the axis of ®bre
From the viewpoint of interface enhancement,
alignment by more than two-fold compared to ran-
Bisanda and Ansell [8] studied the mechanical and phy-
domly oriented ®bre composites.
sical properties of sisal/epoxy composites and Yang et
Dierent processing methods lead to dierent extent
al. [26] investigated sisal/phenol formaldehyde compo-
of ®bre damage, dierent ®bre-length distribution and
sites. The properties of these two composite systems
hence dierent mechanical properties. The eect of ®bre
have already been discussed in Sections 3.2.2 and 3.2.3.
length on the mechanical properties can be explained by
the fact that long ®bres tend to bend or curl during
4.2. Sisal-®bre-reinforced thermoplastics matrices
moulding. This causes a reduction in the eective length
of the ®bre below the critical ®bre length in a particular
In recent years, sisal-®bre-reinforced thermoplastics
direction and hence a decrease of mechanical properties.
composites have gained much more interest among
The experimental tensile properties of short sisal-
materials scientists and engineers than thermosets
®bre-reinforced LDPE with dierent ®bre-volume frac-
because of their low cost and recyclable properties. Many
tions have been compared with existing theories of
papers have now been published to study the properties
reinforcement [44]. The models selected were series and
Y. Li et al. / Composites Science and Technology 60 (2000) 2037±2055
Variation of tensile properties of melt mixing composite (MMC) and solution mixing composite (SMC) with ®bre content [35]a
Elongation at break
Elongation at break
a Average ®bre length: 5.8 mm; values given in parentheses are the properties of unidirectionally aligned ®bre composites.
c x
MmVm Mf Vf
1 ÿ x
Variation of tensile properties of solution mixing composite (SMC)
with repeated extrusion of the blends [35]a
Elongation at break
c x
TmVm Tf Vf
1 ÿ x
where x is a parameter which determines the stress
transfer between ®bre and matrix. It is always assumed
that x is determined mainly by ®bre orientation, ®bre
a Average ®bre length: 5.8 mm, ®bre content: 20 wt.%.
length l and stress ampli®cation eect at the ®bre ends.
This model is in fact a combination of the parallel and
series models.
parallel [45], Hirsch [46], Halpin-Tsai [47], modi®ed
Halpin-Tsai [48], Cox [49] and modi®ed Bowyer and
. Halpin-Tsai model [47]
Bader [50] models. These models are given below for
. Parallel and series model [45]:
Mc MfVf MmVm
Tc TfVf TmVm
where A is a factor determined by ®bre geometry, ®bre
distribution and ®bre-volume fraction. and account
for the relative moduli and strength of ®bre and matrix,
. Modi®ed Halpin-Tsai equation [48]
where M, T and V are Young's moduli, tensile strength
and volume fraction, respectively. The subscripts c, m
and f represent composite, matrix and ®bre, respec-
. Hirsch's model [46]
Y. Li et al. / Composites Science and Technology 60 (2000) 2037±2055
where lc is the critical ®bre length.
Experimental results and theoretical values obtained
from the above models were compared. It is observed
that all models except the series and parallel models
The modi®ed Halpin-Tsai equation includes the max-
show reasonable agreement with experimental data of
imum packing fraction, max, of the reinforcement. max
longitudinally oriented composites, especially at low
equals 0.785 for square arrangement of ®bres, 0.907 for
®bre-volume fractions. But, the Hirsch and modi®ed
hexagonal array of ®bres and 0.82 for random packing
Bowyer and Bader equations show the closest agree-
of ®bres. and are given by Eqs. (9) and (10),
ment with test results. However, agreement with the
respectively, and depends on the particle packing
experimental data of randomly oriented composites
fraction. l=d is the ®bre aspect ratio.
cannot be accurately predicted with these two models as
shown in Figs. 5 and 6. All theoretical models indicate
that the tensile properties of short-®bre-reinforced com-
posites strongly depend on ®bre length, ®bre volume
fraction, ®bre dispersion, ®bre orientation and ®bre/
c Mf Vf
1 ÿ
matrix interfacial strength.
4.2.2.2. Dynamic mechanical properties. The eects of
®bre length, orientation, volume fraction and ®bre sur-
face treatment on the dynamic mechanical properties of
sisal-®bre-reinforced PE including storage modulus, loss
modulus and damping characteristics have also been
where r is the radius of the ®bre, Gm is the shear mod-
studied [34]. It is found that addition of 10% of short
ulus of matrix, Af is the area of the ®bre and R is the
sisal ®bres into LDPE increases the storage moduli and
centre-to-centre distance of the ®bres. For hexagonally
loss moduli of the composites, levelling o at higher
volume fraction. This is believed to be caused by the
increasing ®bre-to-®bre interaction at high volume frac-
R
p 1
tions resulting in poor dispersion. Both storage and loss
moduli decrease with increase of temperature. The
damping properties of the composites decrease with
For square packed ®bres
addition of ®bres and are strongly in¯uenced by ®bre
orientation. The storage and loss moduli of randomly
oriented composites were intermediate between those of
longitudinally and transversely oriented composites.
The in¯uence of ®bre length indicates that a critical
. Modi®ed Bowyer and Bader's model [50]
length of 6 mm is needed to obtain maximum dynamic
moduli. This suggests that a critical length exists for
Bowyer and Bader's model indicates that the tensile
maximum stress transfer between ®bre and matrix. The
strength of short-®bre-reinforced thermoplastic compo-
storage and loss moduli of the isocyanate-treated com-
sites is the sum of contributions from sub-critical and
posites are higher than those of the untreated composites
super-critical ®bres and that from the matrix.
as a result of the improved ®bre/matrix interface adhe-
sion. Some dynamic mechanical results are shown in
Mc MfK1K2Vf MmVm
Figs. 7 and 8.
4.2.2.3. Electrical properties. The electrical properties of
Tc TfK1K2Vf TmVm
sisal-®bre-reinforced LDPE have been studied with
respect to the eects of frequency, ®bre content and
where K1 is the ®bre orientation factor and K2 is the
®bre length on the dielectric constant, volume resistivity
®bre length factor. If ®bre length l > lc,
and dielectric loss factor [51]. The dielectric constant
increases steadily with increasing ®bre content for all
frequencies in the range 1 to 107 Hz. It is also noted that
dielectric constant decreases with increase of ®bre length
If ®bre length l < lc,
and frequency. Maximum dielectric constant values are
Y. Li et al. / Composites Science and Technology 60 (2000) 2037±2055
Fig. 5. Variation of experimental and theoretical tensile properties of
Fig. 8. Variation of loss moduli with temperature for untreated (ran-
randomly oriented composites as a function of ®bre-volume fraction
domly oriented) sisal/LDPE composites at dierent ®bre content.
[44] ( Ð ) strength (- - - -) modulus.
Fibre length=6 mm, frequency=10 Hz [34].
dielectric constants of the latter composites with fre-
quency and ®bre content are smaller as a result of their
lower interfacial polarisation. The dielectric constant,
dielectric loss factor and electrical conductivity of 25%
sisal/LDPE can be increased considerably by adding
5% carbon black. The electrical conductivity of hydro-
phobic LDPE can also be improved by mixing it with
hydrophilic ligno-cellulosic ®bres. Solution mixing
technique has no adverse eects. Finally, it is important
to mention that a 25% sisal/LDPE composite contain-
ing 5% carbon black can be used in anti-static applica-
tions to dissipate static charges.
Fig. 6. Variation of experimental and theoretical tensile properties of
randomly oriented composites as a function of ®bre length [44]. For
keys, see Fig. 5.
4.2.2.4. Ageing properties. The environmental proper-
ties of sisal-®bre composites are very important because,
as a natural ®bre, sisal ages and causes degradation. The
eects of aging on the physical and mechanical proper-
ties of sisal-®bre-reinforced polyethylene composites
have been studied [52]. The tensile properties and
dimensional stability are evaluated under two dierent
ageing conditions: one is by immersing samples in boil-
ing water for 7 h under atmospheric pressure; and the
other is by heating the samples at 70C in an air circu-
lating oven for 7 days. Both cardanol derivative of tol-
uene di-isocyanate (CTDIC) treated and untreated sisal-
®bre-reinforced composites have been studied. The age-
ing properties of the sisal composites are also compared
Fig. 7. Storage moduli and mechanical-loss factor versus temperature
to those of glass-®bre composites aged under identical
for untreated (randomly oriented) sisal/LDPE composites at dierent
conditions. It is concluded that CTDIC-treated compo-
®bre content. Fibre length=6 mm, frequency=10 Hz [34].
sites showed better mechanical properties and dimen-
sional stability as compared to untreated composites as
obtained at low frequencies. Sisal/LDPE composites of 1
a result of the existence of an eective interfacial bond
mm ®bre length and 30% ®bre content have the highest
between ®bre and matrix. Better dimensional stability is
values of dielectric constants at all frequencies. The
oered by glass/LDPE composite because of the
volume resistivity values decrease with increase of fre-
hydrophobic nature of the glass ®bre. With suitable
quency and ®bre content, i.e. the electric conductivity of
®bre-surface treatment, mechanical properties such as
composites are greater than neat LDPE. When com-
strength and elastic modulus of sisal/LDPE composites
pared to glass/LDPE composites, the same trend in elec-
can be improved to comparable levels as those of glass/
trical properties is observed, but the changes of
Y. Li et al. / Composites Science and Technology 60 (2000) 2037±2055
4.2.3. Properties of sisal ®bre-reinforced polystyrene
leads to the poor immersion of ®bres in the PVC matrix.
Also, both treated and untreated sisal/PVC composites
For other thermoplastics matrices, Manikandan et al.
have quite good moisture resistance.
[43] studied the tensile properties of short sisal-®bre-
reinforced polystyrene composites. Untreated and ben-
4.3. Sisal-®bre-reinforced rubber matrix
zoylated sisal ®bres were used to produce the compo-
sites and the in¯uences of ®bre length, ®bre content,
Table 8 shows that rubber is the second most widely
®bre orientation and ®bre benzoylation were investi-
used matrix for sisal ®bre composites behind poly-
ethylene [53±59]. Rubber matrices include natural rub-
Variation in ®bre length produces no considerable
ber and styrene±butadiene rubber. The main research
change in the modulus of the composites but gives
areas concern the eect of ®bre length, orientation,
maximum tensile strength (25 MPa) at a ®bre length of
loading, type of bonding agent and ®bre/matrix inter-
about 10 mm (aspect ratio=82). This critical ®bre
action on the properties of the composites which include
length is quite dierent to the sisal/PE composite which
mechanical properties, rheological behaviour, thermal
is 6 mm. Table 11 shows the eect of ®bre-volume frac-
ageing, gamma-radiation and ozone resistance.
tion on the mechanical properties. There is an initial
Experimental results show that, for best balance of
reduction in tensile strength at Vf 10% followed by
properties, the ®bre length is about 6 mm. This is the
an increase to Vf 20% and remains constant at even
same as the sisal/PE composites. Orientation eects are
higher Vf. These results are also dierent to sisal/PE
as expected. Addition of short sisal ®bres to rubber oers
composites which conform to the rule of mixtures. The
good reinforcement, which can be further strengthened
orientation eects on the mechanical properties of sisal/
by a suitable coupling agent such as a resorcinol/heca
PS composites are also given in Table 11.
bonding system.
A two-stage stress relaxation has been observed in
4.2.4. Properties of sisal-®bre-reinforced PVC composite
acetylated sisal-®bre-reinforced natural rubber compo-
Yang et al. [42] studied sisal/PVC composites with
sites. Initial relaxation occurs at short times (200 s), and
respect to the eects of ®bre and matrix modi®cation,
second-stage relaxation takes much longer to complete.
processing parameters on the mechanical and water
The initial mechanism is a result of the ®bre/rubber
resistance properties. Their main objective is to obtain
attachments and the latter to the physical and chemical
the best processing parameters and interface modi®ca-
relaxation processes of the natural rubber molecules.
tion to make novel sisal/PVC composites. To make good
The relaxation is in¯uenced by the coupling agent indi-
use of sisal ®bre and PVC, it is important to improve the
cating that the ®bre/rubber interface is involved. Gum
interface so that better mechanical properties of the
vulcanite shows only one relaxation process, the rate of
composite can be obtained. But, unfortunately,their
which is almost independent of the strain level. For the
results show that thermal treatment, acetylation and
composite without a coupling agent, the rate of relaxa-
coupling agent improve neither the interface nor the
tion increases with strain level and vice versa. The initial
mechanical properties. On the contrary, the untreated
rate of the stress-relaxation process diminishes after
sisal-®bre-reinforced PVC composite possesses better
ageing (at 70 and 100C for 4 days).
mechanical properties. These results have been explained
Varghese et al. [57] studied the eect of acetylation
by the small ®bre-volume fraction (18.5%) of their
and bonding agent on the ageing properties of sisal-®bre-
composites and the melting processing method that
reinforced natural rubber composites which include
Tensile properties of sisal-polystyrene composites as a function of ®bre content and ®bre orientation [43]a
Fibre Content (wt%)
Ultimate tensile strength (MPa)
Young's modulus (MPa)
Elongation at break (%)
a Fibre length was 6 mm. The values in parentheses give the properties of untreated ®bre composites. L, longitudinal; T, transverse; R, randomly
Y. Li et al. / Composites Science and Technology 60 (2000) 2037±2055
thermal ageing, gamma radiation and ozone resistance.
®re behaviour of sisal short-®bre-reinforced gypsum
High ®bre-volume fraction shows better resistance to
using specially designed testing equipment. Though
ageing, especially with ®bre-surface treatment. Fibre
gypsum itself has good combustion-resistance, with
orientation is also found to reduce the extent of degra-
increasing water reduction as a result of increasing
dation under these ageing conditions. Increasing the
temperature, there is a progressive shrinkage process
dosage of gamma radiation was found to increase the
that promotes surface ®ssuration. Adding sisal ®bres
extent of the ageing process.
into the gypsum matrix increases the ®re insulating per-
formance and delays the occurrence of surface ®ssura-
4.4. Sisal-®bre-reinforced gypsum and cement matrices
Swift [66] studied sisal/cement composites and their
For applications as building materials, sisal-®bre-
potential for rural Africa. He studied the mechanical
reinforced gypsum and cement composites have long
properties including ¯exural, energy absorption and
been studied before 1994 [60±65]. The majority of these
pointed out that a composite material formed by sisal
works are focused on interface, mechanical, ®re and
®bre and cement is suitable for applications in several
environmental properties and their applications.
structures. For example, cladding walls to produce
Bessell and Mutuli [65] studied the interfacial bond
earthquake-resistant adobe structures for houses, roof-
strength of sisal/cement composites using a tensile spe-
ing sheets and tiles, grain storage bins and water ducts.
cimen containing a single ®lament in the brittle matrix.
The crack spacing in the matrix was measured and used
4.5. Other matrix systems
to evaluate the ®bre/matrix bonding strength. It is
shown that the interfacial bond of sisal/cement compo-
Bisanda and Ansell [3] used cashew nut shell liquid
site is lower than that of other composites because sisal
(CNSL) as a matrix to make sisal-®bre-reinforced com-
®bre absorbs moisture from cement thus leading to a
posites. CNSL is a natural monomer blend that has
very poor interface.
been condensation polymerized with formaldehyde
The following aspects of sisal-®bre-reinforced cement
in the presence of an alkaline catalyst to produce a
or gypsum composites have also been studied pre-
thermosetting resin. It can be used to bind sisal ®bres to
viously. For example, Hernandez et al. [61] studied the
produce a cheap and useful composite. The resin is
Variation of mechanical properties with volume fraction of GRP in sisal/glass hybrid composites [68]ab
Volume fraction of ®bres
Elongation at break
a SRP, sisal-®bre-reinforced plastics; GRP, glass-®bre-reinforced plastics.
b Values in parentheses are properties of randomly oriented composites.
Properties of 50:50 sisal/glass hybrid composites containing alkali-treated and untreated sisal ®bre [68]a
Tensile strength (MPa)
Young's modulus (MPa)
Elongation at break (%)
Tear strength (N/mm) Hardness (Shore D)
a L, longitudinal oriented; R, random oriented.
Y. Li et al. / Composites Science and Technology 60 (2000) 2037±2055
thermally stable up to 230C and is further cross-linked
when exposed to simulated sunlight. The plain woven
mats of mercerized sisal ®bre when impregnated with
Sisal ®bre is an eective reinforcement of polymer,
CNSL/fomaldehyde resin produced plain and corru-
rubber, gypsum and cement matrices. This has created a
gated laminated composites showing mean tensile
range of technological applications beyond its tradi-
strength of 94.5 MPa and Young's modulus of 8.8 GPa
tional usage as ropes, carpets, mats, etc.
[3]. It is recommended that these low-cost corrugated
The mechanical and physical properties of sisal ®bre
panels can be used for roo®ng applications as a
not only depend on its source, position and age which
result of their adequate crush bending strength (13.9
will aect the structure and properties, but also depend
on the experimental conditions, such as ®bre diameter,
gauge length, strain rate and test temperature.
Fibre-surface treatment can improve the adhesion
5. Sisal and synthetic hybrid-®bre composites
properties between sisal ®bre and matrix and simulta-
neously reduce water absorption. Such methods include:
Reinforcement by two or more ®bres in a single
(a) silane and other coupling agents to introduce long
matrix leads to hybrid composites with a great diversity
chain structures onto the sisal ®bre to change its
of material properties. It appears that the behaviour of
hydrophilic characteristics; (b) peroxide to promote
hybrid composites is simply a weighted sum of the indi-
grafting reactions; (c) permanganate and alkali to
vidual components so that there is a more favourable
increase the roughness of ®bre surface hence increasing
balance of properties in the resultant composite mate-
the surface area available for contact with the matrix;
rial. Sisal and glass ®bres are one good example of
and (d) thermal treatment.
hybrid composites [67±69] possessing very good com-
Dierent matrix systems have dierent properties.
bined properties.
The mechanical and physical properties of sisal-®bre-
For sisal/glass-®bre-reinforced LDPE hybrid compo-
reinforced composites are very sensitive to processing
sites, the eects of ®bre orientation, composition and
methods, ®bre length, ®bre orientation and ®bre-volume
®bre-surface treatment on the mechanical properties
have been studied and the results are shown in Table 12.
Sisal and glass ®bres can be combined to produce
Owing to the superior properties of glass ®bres the
hybrid composites which take full advantage of the best
mechanical properties of the hybrid composites increase
properties of the constituents. Almost all the mechanical
with increasing volume fraction of glass ®bres. Positive'
properties show positive' hybrid eects.
or negative' hybrid eect is de®ned as larger' or smal-
ler' than the properties calculated from the rule of mix-
tures of the two constituent ®bre-reinforced composites.
A positive hybrid eect has been observed for all
mechanical properties except elongation at break. This
From this review, it is clear that chemically treated or
eect is a consequence of increased ®bre dispersion and
modi®ed sisal-®bre-reinforced composites are potential
orientation with increasing volume fraction of glass
structural materials as a result of their good mechanical,
environmental and economic properties. The following
The eect of chemical modi®cation (alkali treatment)
areas of research are, however, needed to realise wider
of sisal ®bres on the mechanical properties of a 50:50
applications of sisal ®bres in engineering:
sisal/glass hybrid composite is shown in Table 13 and
the improvement is generally less than 10%. Water
absorption of the composite is reduced from 11.6 to
. Sisal-textile-reinforced composite is an important
3.1% compared to the non-hybridized sisal-®bre com-
area in which little work has been done [3]. Sisal
®bres can be woven into textile preforms and
Yang et al. [69] studied the mechanical and interface
impregnated with resins by resin transfer moulding
properties of sisal/glass-®bre-reinforced PVC hybrid
(RTM) or resin ®lm infusion (RFI) to make
composites before and after immersion in water. It is
superior but more economical composites.
found that there exists a positive' hybrid eect for the
. Microstructure of the interface between sisal ®bre
¯exural modulus and unnotched impact strength but a
and matrix still needs to be investigated and the
negative' hybrid eect for the ¯exural strength. It is
interfacial properties should be studied with more
suggested that the negative' hybrid eect is caused by
rigorous single ®bre pullout and fragmentation
the poor interface between sisal, glass ®bres and PVC
tests [70]. The relationship between interface and
matrix. They also suggested that water will have a det-
bulk composite properties should be established.
rimental eect on the ®bre/matrix interface leading to
. Fracture toughness and fracture mechanisms of
reduced properties.
sisal-®bre composites do not seem to have been
Y. Li et al. / Composites Science and Technology 60 (2000) 2037±2055
studied in any depth in previous published works.
on the tensile properties of short sisal ®bre-reinforced poly-
This is important if new improved materials are to
ethylene composites. Polymer 1996;37:5139±49.
be developed for safe usage against crack growth.
[7] Chand N, Hashmi SAR. Metals Materials and Processes
. Mechanical properties of sisal-®bre composites
[8] Bisanda ETN, Ansell MP. The eect of silane treatment on the
measured from tests quite often disagree with the
mechanical and physical properties of sisal±epoxy composites.
rule of mixtures. A full explanation can only be
Composites Science and Technology 1991;41:165±78.
obtained if the interface strength and the failure
[9] Li H, Zadorecki P, Flodin P. Cellulose ®bre±polyester composites
mechanisms are known. Further work is needed
with reduced water sensitivity. (1) Chemical treatment and
particularly to explain hybrid' eects in sisal/glass
mechanical properties. Polymer Composites 1987;8:199±207.
[10] Chand N, Sood S, Rohatgi PK, Sayanarayana KG. Resources,
structure, properties and uses of natural ®bres of madhya pra-
. Economical processing methods must be devel-
desh. Journal of Scienti®c and Industrial Research 1984;43:489±
oped for the composites because of the very low
price of sisal ®bres. The relationship between
[11] Bisanda ETN. The manufacture of roo®ng panels from sisal ®bre
mechanical properties and processing methods
reinforced composites. Journal of Materials Processing Technol-
should be established.
[12] Chand N, Satyanarayana KG, Rohatgi PK. Mechanical char-
. New applications should be found for sisal-®bre-
acteristics of sunhemp ®bres. Indian Journal of Textile Research
based composites. Hybrid ®bre composites with
sisal and other ®bres rather than glass may open
[13] Hornsby PR, Hinrichsen E, Tarverdi K. Preparation and prop-
up new applications. For example, from the eco-
erties of polypropylene composites reinforced with wheat and ¯ax
straw ®bres. Part 1, ®bre characterisation. Journal of Materials
nomics point of view, sisal ®bres may be hybri-
dised with carbon or aramid ®bres to reduce the
[14] Satyanarayana KG, Sukumaran K, Mukherjee PS, Pavithran C,
costs of these expensive ®bres reinforced compo-
Pillai SG. Natural ®bre-polymer composites. Cement & Concrete
sites whilst maintaining their good mechanical
[15] Chand N, Hashmi SAR. Mechanical properties of sisal ®bre at
. Recycling (including burning) characteristics and
methods of sisal-®bre-reinforced composites are
[16] Chand N, Joshi SK. Temperature dependence of dielectric beha-
important aspects of this new material but there
viour of sisal ®bre. Journal of Materials Science Letters
are very few published data to date. Recycling is
an attractive future research direction that will
[17] Yang GC, Zeng HM, Zhang WB. Thermal treatment and ther-
mal behaviour of sisal ®bre. Cellulose Science and Technology
provide socio-economic bene®ts.
[18] Zhou LM, Mai Y-W, Ye L, Kim JK. Techniques for evaluating
interfacial properties of ®bre-matrix composites. Key Engineering
[19] Kim JK, Zhou LM, Mai Y-W. Interfacial debonding and ®bre
pull-out stresses. Part III. Interfacial properties of cement matrix
Y. Li would like to thank the University of Sydney
composites. Journal of Materials Science 1993;28:3923±30.
for an Overseas Postgraduate Research Scholarship
[20] Yang GC, Zeng HM, Li JJ, Jian NB, Zhang WB. Relation of
(OPRS) and an International Postgraduate Award
modi®cation and tensile properties of sisal ®bre. Acta Scien-
(IPA). Y.-W. Mai also thanks the Australian Research
tiarum Naturalium Universitatis Sunyatseni 1996;35:53±7.
Council for the continuing support on the ®bre/matrix
[21] El-Naggar AM, El-Hosamy MB, Zahran AH, Zondy MH. Sur-
face morphology/mechanical/dyeability properties of radiation-
interface research project.
grafted sisal ®bres. American Dyestu Reporter 1992;81:40±4.
[22] Sabaa MW. Thermal degradation behaviour of sisal ®bres graf-
ted with various vinyl monomers. Polymer Degradation & Stabi-
[23] Chand N, Verma S, Khazanchi AC. SEM and strength char-
[1] Murherjee PS, Satyanarayana KG. Structure and properties of
acteristics of acetylated sisal ®bre. Journal of Materials Science
some vegetable ®bres, part 1. Sisal ®bre. Journal of Materials
[24] Singh B, Gupta M, Verma A. In¯uence of ®bre surface treatment
[2] Chand N, Tiwary RK, Rohatgi PK. Bibliography resource
on the properties of sisal±polyester composites. Polymer Com-
structure properties of natural cellulosic ®bres Ð an annotated
bibliography. Journal of Materials Science 1988;23:381±7.
[25] Kim JK, Lu S, Mai Y-W. Interfacial debonding and ®bre pull-
[3] Bisanda ETN, Ansell MP. Properties of sisal±CNSL composites.
out stresses Part IV: In¯uence of interface layer on the stress
Journal of Materials Science 1992;27:1690±700.
transfer. Journal of Materials Science 1994;29:554±61.
[4] Wilson PI. Sisal, vol. II. In Hard ®bres research series, no. 8,
[26] Yang GC, Zeng HM, Li JJ. Study of sisal ®bre/phenol for-
Rome: FAO, 1971.
maldehyde resin composites. Fibre Reinforced Plastics/Compo-
[5] Rowell RM. In: Rowell RM, Schultz TP, Narayan R, editors.
Emerging technologies for materials & chemicals for biomass,
[27] Sanadi AR, Prasad SV, Rohatgi PK. Sunhemp ®bre-reinforced
ACS Symposium Ser, 476, 1992. p. 12.
polyester Part 1 Analysis of tensile and impact properties. Jour-
[6] Joseph K, Thomas S, Pavithran C. Eect of chemical treatment
nal of Materials Science 1986;21:4299±304.
[28] Pavithran C, Mukherjee PS, Brahmakumar M, Damodaran AD.
Y. Li et al. / Composites Science and Technology 60 (2000) 2037±2055
Impact properties of natural ®bre composites. Journal of Mate-
[48] Nielson LE. Mechanical properties of polymers and composites,
rials Science Letters 1987;6:882±4.
vol. 2. New York: Marcel Dekker, 1974.
[29] White NM, Ansell MP. Straw-reinforced polyester composites.
[49] Cox HL. The elasticity and strength of paper and other ®brous
Journal of Materials Science 1983;18:1549±56.
materials. British Journal of Applied Physics 1952;3:72±9.
[30] Pavithran C, Mukherjee PS, Brahmakumar M, Damodaran AD.
[50] Bowyer WH, Bader MG. On the re-enforcement of thermo-
Impact performance of sisal±polyester composites. Journal of
plastics by imperfectly aligned discontinuous ®bres. Journal of
Materials Science Letters 1988;7:825±6.
Materials Science 1972;7:1315±21.
[31] Gordon JE, Jeronimidis. Philosophical Transactions. Royal
[51] Paul A, Thomas S, Pavithran C. Electrical properties of natural-
Society of London, Series A: Mathematical and Physical Sciences
®ber reinforced low density polyethylene composites: a compar-
ison with carbon black and glass-®bre ®lled low density poly-
[32] Rong MZ, Li RKY, Ng CN, Tjong SC, Mai Y-W, Zeng HM.
ethylene composites. Journal of Applied Polymer Science 1997;
Eect of ®bre pretreatment on the impact fracture toughness of
sisal ®bre reinforced polymer composites. In Proc. First Asian±
[52] Joseph K, Thomas S, Pavithran C. Eect of ageing on the physi-
Australian Conference on Composite Materials (ACCM- 1), 7±9
cal and mechanical properties of sisal-®bre-reinforced poly-
October 1998, Oseka, Japan. p 433-1±4.
ethylene composites. Composites Science and Technology
[33] Rong MZ, Li RKY, Ng CN, Tjong SC, Mai Y-W, Zeng HM.
Eect of water absorption on the impact behaviour of short sisal
[53] Prasantha RP, Kumar ML, Amma G, Thomas S. Short sisal ®bre
®bre reinforced polymer composites. In Proc. First Asian±Aus-
reinforced styrene±butadiene rubber composites. Journal of
tralian Conference on Composite Materials (ACCM-1), 7±9
Applied Polymer Science 1995;58:597±612.
October 1998, Oseka, Japan. p 438-1±4.
[54] Varghese S, Kuriakose B, Thomas S. Stress relaxation in short
[34] Joseph K, Thomas S, Pavithran C. Dynamic mechanical proper-
sisal-®bre-reinforced natural rubber composites. Journal of
ties of short sisal ®bre reinforced low density polyethylene com-
Applied Polymer Science 1994;53:1051±60.
posites. Journal of Reinforced Plastics and Composites
[55] Kumar RP, Thomas S. Short ®bre elastomer composites: eect of
®bre length, orientation, loading and bonding agent. Bulletin of
[35] Joseph K, Thomas S, Pavithran C, Brahmakumar M. Tensile
Materials Science 1995;18:1021±9.
properties of short sisal ®bre-reinforced polyethylene composites.
[56] Kumar PR, Thomas S. Tear and processing behaviour of short
Journal of Applied Polymer Science 1993;47:1731±9.
sisal ®bre reinforced styrene butadiene rubber composites. Poly-
[36] Joseph K, Kuriakose B, Premalatha CK, Thomas S. Melt rheo-
mer International 1995;38:173±82.
logical behaviour of short sisal ®bre reinforced polyethylene
[57] Varghese S, Kuriakose B, Thomas S. Short sisal ®bre reinforced
composites. Plastics Rubber & Composites Processing & Appli-
natural rubber composites: high-energy radiation, thermal and
ozone degradation. Polymer Degradation & Stability 1994;44:55±
[37] Joseph K, Thomas S, Pavithran C. Viscoelastic properties of
short-sisal-®bre-®lled low-density polyethylene composites: eect
[58] Varghese S, Kuriakose B, Thomas S, Koshy AT. Mechanical and
of ®bre length and orientation. Materials Letters 1992;15:224±8.
viscoelastic properties of short ®bre reinforced natural rubber
[38] Karmaker AC. Eect of water absorption on dimensional stabi-
composites: eects of interfacial adhesion, ®bre loading, and
lity and impact energy of jute ®bre reinforced polypropylene.
orientation. Journal of Adhesion Science & Technology 1994;
Journal of Materials Science Letter 1997;16:462±4.
[39] Garkhail S, Heijenrath R, Oever M, van den, Bos H, Peijs T.
[59] Varghese S, Kuriakose B, Thomas S, Premalatha CK. Rheologi-
Natural-®bre-mat-reinforced thermoplastic composites based on
cal behaviour of short sisal ®bre reinforced natural rubber com-
¯ax ®bres and polypropylene. In Scott M, editor. Proceedings of
posites. Plastics Rubber & Composites Processing & Applications
ICCM-11, vol. II, Fatigue, fracture and ceramic matrix compo-
sites, Gold Coast, Australia, 14±18 July 1997. p. 794±803.
[60] Singh M, Garg M. Gypsum-based ®bre-reinforced composites:
[40] Park BD, Balatinecz JJ. Eect of impact modi®cation on the
an alternative to timber. Construction & Building Materials
mechanical properties of wood-®bre thermoplastic composites
with high impact polypropylene (HIPP). Journal of Thermo-
[61] Hernandez OF, Oteiza IDe, Villanueva L. Fire behaviour of sisal
plastic Composite Materials 1996;9:342±63.
short ®bres reinforced gypsum. In Miraveter A, editor. Proceed-
[41] Hornsby PR, Hinrichsen E, Tarverdi K. Preparation and prop-
ings of the Ninth International Conference on Composite Mate-
erties of polypropylene composites reinforced with wheat and ¯ax
rials (ICCM/9), vol. 5, composites behaviour, Madrid, 12±16 July
straw ®bres. Part II. Analysis of composite microstructure and
mechanical properties. Journal of Materials Science 1997;32:
[62] Coutts RSP, Warden PG. Sisal pulp reinforced cement mortar.
Cement & Concrete Composites 1992;14:17±21.
[42] Yang GC, Zeng HM, Li JJ. The study of technology and prop-
[63] Mwafongo FG. Sisal-reinforced cement. Batiment International/
erties of composites for sisal ®bre reinforced PVC. Fibre Rein-
Building Research & Practice 1987;20:241±2.
forced Plastics/Composites 1995;6:22±6.
[64] Hernandez OF, Oteiza IDe, Villanueva L. Experimental analysis
[43] Manikandan KC, Nair SMD, Thomas S. Tensile properties of
of toughness and modulus of rupture increase of sisal short ®bre
short sisal ®bre reinforced polystyrene composites. Journal of
reinforced hemihydrated gypsum. Composite Structures 1992;
Applied Polymer Science 1996;60:1483±97.
[44] Kalaprasad G, Joseph K, Thomas S. Theoretical modelling of
[65] Bessell TJ, Mutuli SM. The interfacial bond strength of sisal±
tensile properties of short sisal ®bre±reinforced low-density poly-
cement composites using a tensile test. Journal of Materials Sci-
ethylene composites. Journal of Materials Science 1997;32:4261±7.
ence Letters 1982;1:244±6.
[45] Broutman LJ, Krock RH. Modern composite materials. Reading
[66] Swift DG. Sisal-cement composites and their potential for rural
(MA): Addison Wesley, 1967.
Africa. In: Marshall IH, editor. Composite structures 3, Elsevier
[46] Hirsch TJ. Modulus of elasticity of concrete aected by elastic
Applied Science Publisher. London/New York: p. 774±87.
moduli of cement paste matrix and aggregate. In Proceedings of
[67] Kalapradad G, Joseph K, Thomas S. In¯uence of short glass
the American Concrete Institute 1962;59(12):427±51.
®bre addition on the mechanical properties of sisal reinforced low
[47] Rosen BW. Fibre composite materials. Metals Park (OH):
density polyethylene composites. Journal of Composite Materials
American Society for Metals, 1965. p. 58
Y. Li et al. / Composites Science and Technology 60 (2000) 2037±2055
[68] Kalaprasad G, Thomas S, Pavithran C, Neelakantan NR,
[69] Yang GC, Zeng HM, Jian NB, Li JJ. Properties of sisal ®bre/
Balakrishnan S. Hybrid eect in the mechanical properties of
glass ®bre reinforced PVC hybrid composites. Plastics Industry
short sisal/glass hybrid ®bre reinforced low density polyethylene
composites. Journal of Reinforced Plastics and Composites
[70] Kim JK, Mai Y-W. Engineered interfaces in ®bre reinforced
composites. Oxford: Elsevier, 1998.
Source: http://www.agnieszka.slosarczyk.pl/serwis/repozytorium/data/wlokna/wlokna07.pdf
482586JBX18710.1177/1087057113482586Journal of Biomolecular ScreeningShadrick et al. Review Article Journal of Biomolecular Screening18(7) 761 –781 Discovering New Medicines Targeting © 2013 Society for LaboratoryAutomation and ScreeningDOI: 10.1177/1087057113482586 Helicases: Challenges and Recent Progress William R. Shadrick1, Jean Ndjomou1, Rajesh Kolli1,
Effects of a basic micronutrient supplement on physiological parameters Institute of science of sports University of Salzburg Mag. Michael G. Eder Responsible person: Univ.-Prof. Dr. Erich Müller St. Michael, 2005 Preface Who wants to build high towers, have to spend a lot of his time on the foundation. I want to thank Mr. Mag. Norbert Fuchs, who gave me a lot of inspiration, know how