Roadmarking materials guide rev 2 final july 2009.pdf
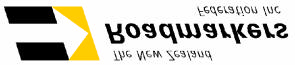
Developed with assistance from InfraTrain New Zealand Ltd, WITT Research
Committee and New Zealand Institute of Highway Technology Ltd
NZRF Roadmarking Materials Guide – Introduction
Introduction
The NZ Roadmarkers Federation developed the roadmarking materials guide in 2004, and
undertook a revision in 2009. It brings together technical information about the range of
marking materials, and associated products that are used by the pavement marking industry. The
Guide was written by Ross Ridings of Quality Surveillance Ltd.
This version of the Guide has involved input from a technical advisory group consisting of:
Alan Parker, 3M New Zealand Ltd
Alister Harlow, NZRF
Bob Carnaby, Potters Industries Pty Ltd
Bob Currie, Britesite (NZ) Ltd
David Goddard, Damar Industries (NZ) Ltd
Rob Dunne, Damar Industries (NZ) Ltd
Steven Borrie, Rohm & Haas
All information not contributed by these people or the companies they represent has been
sourced from the public domain.
The development of the document has been assisted by InfraTrain New Zealand Ltd, the WITT
Research Committee and New Zealand Institute of Highway Technology Ltd who use the
material as a training resource.
The guide should be regarded as a ‘work in progress' and we welcome feedback from industry to
make the document appropriate to users' needs. We particularly welcome information from users
on recorded environmental hazards, and recorded health and safety incidents.
REVIEW AND AMENDMENT
This document has been developed by Quality Surveillance Ltd (QSL) for the New Zealand
Roadmarkers Federation Inc (NZRF).
All information contained in it has been prepared in good faith by QSL and the NZRF and is, to the best of their knowledge, correct and complete. While every care has been taken in the preparation of the information provided, no warranty is given by either QSL or the NZRF as to the correctness of the information herein and no liabilities accepted for any statement or opinion, nor for any error or omission.
The writer may be contacted with regard to document content by either contacting the New Zealand Roadmarkers Federation or Quality Surveillance Ltd NZ Roadmarkers Federation Inc
Quality Surveillance Ltd
North Shore City
Phone 09 625 7470
Phone 09 483 8063
Email: [email protected]
Email: [email protected]
NZRF Materials Guide – Materials Covered
1 Materials covered
Waterborne Paint Polymer Modified Solvent Based Paint Chlorinated Rubber Modified Alkyd Alkyd Temporary / Removable
• Polymethyl Methacrylate (Cold-Applied Plastic) • Thermoplastic
Powder / granulated/ solid Pre-formed (sheet form)
• Self Adhesive Tapes
Permanent Standard Flat Permanent High Performance Temporary / Removable
• Glass Beads / Retroreflective Media
Standard Refractive Index Glass Beads High Index Glass Beads Retroreflective Elements
• Angular Material
Quartz Silica Corundum
Alkyd Paint Thinners Chlorinated Rubber Thinners Waterborne Thinners Cold Applied Plastic Thinners
Waterborne Paint Catalysts Benzyl Peroxide
• Raised Pavement Markers (RPM's)
Permanent Retroreflective (Type A AS 1906.3) Permanent Non Retroreflective (Type B AS 1906.3) Snow-Ploughable Retroreflective Road Studs Illuminated Temporary – "Flickies"
• RPM Adhesive
Bituminous Two Component Adhesive Self-adhesive Pads
NZRF Roadmarking Materials Guide – Materials Covered
• Pavement Overlay Binders
Epoxy Polyurethane
• Cement Based Coatings
Roller Applied Spray Applied
NZRF Roadmarking Materials Guide – Generic Headings
2 Generic Headings
• It is envisaged that each of the following headings is used to provide a repository for the
material relating specifically to the item being discussed. Where this material exceeds two paragraphs a summary will be provided.
1. General Description 2. Composition 3. Physical Properties 4. Performance Properties 5. Durability 6. Compatibility 7. Adhesion 8. Application Parameters 9. Manufacturing Process 10. Testing of Physical Properties 11. Handling, Storage & Packaging 12. Environmental Impacts 13. Occupational Health & Safety Hazards 14. Application Process 15. Process Monitoring Equipment 16. Post-Application Measuring Equipment 17. Test Methods 18. Quick Reference Safety Guide 19. Recorded Environmental Hazards 20. Recorded Health & Safety Incidents 21. Related National / International Standard Specifications 22. Useful References
NZRF Roadmarking Materials Guide – Heading Content & Scope
3 Heading Content & Scope
General Description
Basic description of the product / material. May include definition.
Composition
Description of the typical composition of the component parts of the raw materials used to
produce the item.
Physical Properties
List of the physical properties of the product / material, e.g. density, hardness, etc
Performance Properties
List of the performance properties relating to the use of the material in pavement marking, i.e.
properties such as skid resistance, retroreflectivity and colour as specified by the relevant Road
Controlling Authority, National, or International Specification.
Durability
Description of the typical performance of the product under prescribed pavement surface
conditions. Values for resistance to trafficking, UV exposure and weathering are provided where
these are available. The source of the material, e.g. NZTA M Series, International Standards
(AS 4049, EN 1824, etc), APAS, will be provided.
Compatibility
Description of the known compatibility of the product / material with common pavement
surfaces and other pavement marking materials currently in use. Will provide guidance to
known primers and or surface preparation adhesives where possible. (Surface preparation
adhesive is an American term used due to VOC classification considerations)
Adhesion
Description of the known adhesio n properties of the product / material to commonly used
pavement surfaces. Will provide guidance to known primers and surface preparation adhesives /
adhesion techniques where possible.
Application Parameters
Description of the parameters which need to be complied with for product to perform as intended
by the manufacturer / supplier.
Manufacturing Process
Brief description, where available, of the process by which the product / material is
manufactured or prepared for supply to the pavement marking contractor.
Testing of Physical Properties
Description of the testing methods relating to the product / materials physical properties.
Handling, Storage & Packaging
Description of the physical handling methods, storage requirements and packaging associated
with the product / material. Includes transport Dangerous Goods Information.
Note: Occupational Health & Safety Issues will be dealt with separately
NZRF Roadmarking Materials Guide – Heading Content & Scope
Environmental Impacts
Description, where available, of the possible / likely impact on the natural environment. May
include precautions or methods to manage these impacts in accordance with the New Zealand
Resource Management Act (RMA) 1991 and Hazardous Substances and New Organisms Act
(HSNO) 1996.
Occupational Health & Safety Hazards
Description of the Occupational Health & Safety issues relating the use / application of the
material / product. May include precautions for use to manage these risks in accordance with the
New Zealand Health and Safety in Employment Act (HSE) Act 1992, subsequent amendments
and associated Regulations.
Application Process
Description of the application process intended by the manufacturer / supplier or in common use.
Process Monitoring Equipment
Description of the process monitoring equipment and methods normally associated with the
application of the material / product.
Post - Application Measuring Equipment
Description of the measuring equipment commonly associated with the measurement of the
performance and / or characteristics of the product / material after application.
Test Methods
Description of the methods used to measure the parameters related to the installed product /
resultant markings.
Quick Reference Safety Guide
Brief description of the safety items relating to the material / product. Will summarise the
material on Safety Data Sheets.
Recorded Environmental Hazards
Recounted and reported stories of impacts on the environment encountered / observed by users /
suppliers.
Recorded Health & Safety Incidents
Recounted and reported occupational health & safety incidents.
Related Road Controlling Authority / National / International Standard Specifications
A catalogue of the Road Controlling Authority, National and International Standard
Specifications relevant to the use / application of the material / product.
Useful References
Identification of classic text / reference material relating to the product / material.
Note: these references will be in addition to those references made under the particular item
being discussed.
NZRF Roadmarking Materials Guide - General Descriptions
4 General Descriptions
4.1
A liquid containing pigments which converts to an opaque film on drying. Pigments are dispersed in a binder with a solvent that is either hydrocarbon based or water.
Roadmarking paints are specially blended to provide low gloss and low skid and slip values. Both solvent based and waterborne paint types are used. Solvent based paints can be modified by the addition of materials such as chlorinated rubber to enhance glass bead retention. Waterborne paints may be either catalysed or un-catalysed. Typically applied by spraying in dry film thicknesses varying typically from 70 µm to 500 µm. Application rate dependent on purpose, required life and type of surface dressing applied to marking. May include or have surface applied glass beads and / or reflective elements to provide retroreflectivity and improve skid resistance. May also include surface applied aggregate to provide appropriate skid and slip resistance values. Roadmarking paint was first applied as a centreline in Michigan, USA in 1911, followed by Europe shortly after. There has been an ongoing world-wide movement towards waterborne paint in an endeavour to limit the release of excessive quantities of volatile organic compounds (VOC) into the atmosphere. Of the 25 million litres of decorative paint manufactured in New Zealand in 2007, approximately 78% was waterborne. In Australia, the Australian Paint Approval Scheme (APAS) has set strict limits for VOC's. In New Zealand, the New Zealand Ecolabelling Trust requires that VOC's are limited (60 to 100 gm/l) for the paint to carry the Environmental Choice label. The level of solvents such as toluene in the solvent based paints, and the levels of ammonia in the current waterborne paints would preclude them from Ecolabelling A recent addit ion to the roadmarkers portfolio is temporary or removable paints used for delineation during special events. Paint is currently (2009) the most common form of marking applied in New Zealand.
NZRF Roadmarking Materials Guide - General Descriptions
Cold-Applied Plastic
A cold hardening 2-part poly methyl methacrylate (PMMA) resin material.
PMMA roadmarking material is tailored for specific application methods such as audio-tactile
profiled (ATP) markings, structured markings and plain flat markings. All types come in white
or lead free yellow. All are catalysed by benzoyl peroxide. Applied at thicknesses from 600 µm
up to 15 mm.
Glass beads and / or reflective elements are typically applied to the surface of the marking to
provide initial retroreflectivity, and skid and slip resistance.
PMMA was developed by Rohm and Haas in 1933 and manufactured for particular uses under
licence. Roadmarking (Degussa principal licence) forms have been used in Europe since 1966.
It was first used for pavement marking in New Zealand in 1968.
4.3
A material consisting of aggregate, pigment, binder, glass beads and extenders, capable of being softened by heating and hardened by cooling.
The material is manufactured to a variety of International Standards e.g. EN 1871, AS 4049.2,
AS 4049.4 etc.
Thermoplastic binders are either alkyd or synthetic. Roadmarking material is tailored for
specific application methods such as audio-tactile profile (ATP) markings, structured markings
and plain flat markings. All types come in white or lead free yellow.
Applied at thicknesses varying from 0.5 mm to 13 mm. The glass beads, normally in the range
of 20 to 40% by mass, and aggregates bound by the other material, progressively become
exposed with wear to maintain night visibility and skid and slip resistance.
Glass beads and / or reflective elements are typically surface applied to provide initial
retroreflectivity, and skid and slip resistance.
Developed in UK between 1939 - 1944 primarily to aid motorists during "blackout" periods.
Recent international developments in binder types and constituents have seen significant
increases in performance over older thermoplastic marking materials.
4.4
Self-Adhesive Tapes
A pre- formed adhesive backed product, generally in roll or pre-cut form relying on pressure on the adhesive to create a bond with the pavement surface.
A variety of materials may be used. Tapes may be either hot or cold applied. Tapes are classified as permanent or temporary / removable
NZRF Roadmarking Materials Guide - General Descriptions
Raised Pavement Markers
A "standard non retro-reflective raised pavement marker" "RPM" is a small ceramic, plastic or metallic object adhered to the pavement surface aimed at providing audible / tactile feedback to motorists.
Note: In common usage the term "RPM" can include both RPM's and RRPM's Definition:
A "standard retro-reflective raised pavement marker" "RRPM" is a small ceramic, plastic or metallic object adhered to the pavement surface aimed at providing both audible / tactile feedback and night-time delineation to motorists. The night-time delineation is provided by reflecting vehicle headlights in a narrow focused beam back to the motorist.
A "glass faced" or "ceramic faced" RRPM denotes a marker that has an additional protective layer over the lens to add retroreflective durability.
A "snow-ploughable" RRPM is one that has been designed in such a manner that the risk of it being damaged or removed by regular snow removal operations is minimised.
A "road stud" is a RRPM provided with a spigoted base, which is fitted into a hole, drilled into the road surface.
An "illuminated" RRPM is one which has been designed to project a beam of light towards motorists to replicate the function of standard RRPM's when illuminated by the motorist's headlights.
RRPM's were first developed in the UK in the mid 1930's.The nickname "cats' eyes" arose from
an incident that prompted the inventor to develop and patent a spherical lens device in 1935.
Illuminated RRPM's have been developed for a number of applications such as providing
delineation in tunnels and providing warning to motorists approaching pedestrian crossings
which have been activated by pedestrians wishing to cross, etc. Illuminated RRPM's are either
solar powered directly, wired directly or inductively powered from a solar or reticulated electric
power source.
4.6
RPM Adhesive
Material used to attach raised pavement markers (RPM's) to the road surface, where the RPM does not have adhesive attached.
RPM adhesive can be bituminous (hot-applied), single or two component material.
NZRF Roadmarking Materials Guide - General Descriptions
Glass Beads (Retroreflective Beads)
Small spherical silica glass beads applied to / in pavement markings to improve the night-time visibility by retro-reflecting vehicle headlights.
Roadmarking glass beads are available in a range of size, clarity and refractive index
classifications.
The higher index beads are aimed at specific applications such as airport markings and those
markings requiring superior performance in conditions of rain.
The size of retroreflective beads / elements applied needs to be matched to marking materials dry
film thickness to work effectively.
Roadmarking beads applied on NZTA funded / managed roading networks are required to
comply with Australian Standard AS 2009.
In addition to the RMA and HSNO requirements, NZTA have applied a limit for heavy metals
present in beads used on New Zealand Roads.
Glass beads have been most commonly used but new technology ceramic beads and bonded core
elements that enable reflectivity in wet conditions are also available.
4.8
Retroreflective Elements
Small spherical beads that are adhered to a core to provide an element of many microscopic retroreflective beads. May be described as bonded core elements.
A recent development has been the introduction of retroreflective elements which are aimed at
providing enhanced retroreflectivity of roadmarkings during the condition of rain. Elements
consist of glass beads bonded together or bonded to a suitable material to form an agglomerate
which provides retroreflectivity even if flooded by water.
4.9
Angular Material
Fine angular shaped aggregate applied to / in pavement markings to improve the skid and slip resistance of the marking over a range of conditions.
Angular material is generally surface applied to pavement markings to enhance the skid and slip
resistance. The addition of angular material with glass beads must be well controlled to ensure
that retroreflectivity is not compromised.
4.10 Modified Epoxy Resin
Definition:
A cold-hardening 2 part epoxy resin modified to bind fine angular shaped aggregate to pavement surfaces.
Epoxy paving aggregate binding material is tailored for specific application methods. Typically applied at 1 to 2.5 kg/m² .
NZRF Roadmarking Materials Guide - General Descriptions
4.11 Modified Polyurethane Resin
Definition:
A cold-hardening 2 part polyurethane resin modified to bind fine angular shaped aggregate to pavement surfaces.
Polyurethane paving aggregate binding material is tailored for specific application methods.
Typically applied at 1.35 to 2.6 kg/m².
4.12 Cement Based Coatings
Definition:
A compound consisting of white cement and aggregates which when mixed with water cures by hydration.
Applied at thicknesses of 2 to 3 mm to vertical and inclined surfaces such as kerbs, New Jersey barriers and roundabout faces. Greater thicknesses can be achieved by layering. Glass beads and / or reflective elements are injected into the surface under pressure to provide retroreflectivity.
NZRF Roadmarking Materials Guide - Roadmarking Material Classification Schemes
5 Roadmarking Material Classification Schemes
5.1 New Zealand Transport Agency
Most of the roadmarking materials used on New Zealand roads are tested and approved against
physical and performance requirements specified in NZTA specifications.
Paint
Paints are principally tested and approved against the requirements of NZTA M 7 – Specification
for Roadmarking Paints. Approved materials are reported in NZTA M 7 Notes – Notes to
Specification for Roadmarking Paints.
There are three classifications, A, B and C. An A classification means that the paint has been
tested and found to maintain the performance required up to 1 Million vehicle passes. B
classification passed the requirements after 1.5 Million vehicle passes and C classification means
that it performed in excess 2 Million vehicle passes.
The material results are reported for the specific application parameters at which they were
tested and complied, i.e. at 180 µm, 220 µm, or 300 µm, and all markings are recorded as
reflectorised or unreflectorised.
Long-life Markings
Long- life markings, (CAP, thermoplastic, etc), are tested and approved under NZTA M 20 –
Specification for Long- life Roadmarking Materials with the M 20 Notes – Notes to Specification
for Long- life Roadmarking Materials providing the approvals record.
The current M 20 (NZTA M 20:2003) has a single performance classification of 3 Million
vehicle passes.
Raised Pavement Markers
Raised pavement markers, both reflectorised and non-reflectorised, are tested and approved
under NZTA M 12 – Specification for Raised Pavement Markers, with the M 12 Notes – Notes
to Specification for Raised Pavement Markers to providing the approvals.
The performance requirements are principally those required by Australian Standard AS 1906.3
– Retroreflective Materials and Devices for Road Traffic Control Purposes.
5.2 Australian Paint Approval Scheme (APAS)
The Australian Government operates the APAS approval scheme which sets criteria for material
performance, environmental heath and safety and quality assurance.
NZRF Roadmarking Materials Guide – Waterborne Paint
6 Waterborne Paint
General Description
• A high-solids quick drying water-based acrylic pavement marking paint
• May be formulated for use with catalysts to accelerate dry-time and / or enhance performance.
• Glass beads and / or reflective elements are surface applied to provide retroreflectivity where
Composition
• Typically 60 to 68 per cent volume solids
• Water miscible solvents used in formulation
• Thinned with water-based thinners.
Physical Properties
• Fast drying – "No-pickup" time 7-15minutes as per AS/NZS 1580 401.8. "Dry-through"
times in the range of 40 to 60 minutes. Drying time dependent on film thickness, relative humidity, temperature and airflow
• Specially formulated waterborne paints used with catalysts have "no-wash-out" times of
• Self cleaning
• Colours: Full range including White, Yellow, & Black
• Holds beads, (particularly Class D), better than standard alkyd paints
• pH of approximately 10
• High miscibility in water.
•
Performance Properties
• Skid Resistance: not less than 45 BPN when tested in accordance with Appendix B of NZTA
• Without the aid of surface applied particles skid resistance can be as low as 30 BPN
• Retroreflectivity: No values available for un-beaded paint
• When tested in accordance with either Appendix B or Appendix C of NZTA M 7, the
retroreflectivity of a beaded test paint film after the required number of vehicle passes shall not be less than 100 mcd/m²/lux for white paint and 80 mcd/m²/lux for yellow paint
• Colour: White equal to or whiter than Y35 "Off White" (NZTA M 7), Yellow between Y13
"Vivid Yellow" and Y14 "Golden Yellow" of AS 2700S (NZTA M 7) or approximately match Y14, (AS 4049.3).
•
Durability
• The durability of a waterborne paint system is dependent on its formulation and the beads /
aggregate applied to it. Waterborne paint systems (with appropriate formation and application) are capable of achieving the requirements of NZTA P 30 Specification for High Performance Roadmarking
• Thickness of application necessitates repeated application compared to "long-life" materials
such as cold applied plastics or thermoplastic, however, this depends on traffic volumes, pavement surface and applied thickness
NZRF Roadmarking Materials Guide – Waterborne Paint
• Material remains "plastic" throughout ageing process
• When applied at 180 µm dry performance is generally better than 1 million vehicle passes
when tested in accordance with NZTA M 7 – Refer to latest version of NZTA M 7 Notes
• When applied at 220 µm dry performance is generally better than 1.5 million vehicle passes
when tested in accordance with NZTA M 7 – Refer to latest version of NZTA M 7 Notes
• When applied at 300 µm dry performance is generally better than 2.0 million vehicle passes
when tested in accordance with NZTA M 7 – Refer to latest version of NZTA M 7 Notes.
Compatibility
• Can be used on most types of surfaces and for longitudinal, transverse and other markings
• No compatibility problems observed. Water based paint appears to adhere well to
thermoplastic, solvent based paint and itself
• Should not be applied on metal substrates without the use of an appropriate anticorrosive
Adhesion
• Does not perform well on mechanically trowelled / polished concrete. All paints are sensitive
to the alkalinity of fresh concrete. Concrete curing agents may have adverse effect on paint adhesion. New concrete and asphalt should be aged for a minimum of 30 days prior to painting (The USA, with history in concrete road formation, recommends 90 days open to traffic for new concrete to wear off curing compound). Sealers and primers may be used.
Application Parameters
• Markings must be protected from traffic until thoroughly dry. Refer to Chart for Dry Time of
Waterborne Paint contained in RTA Use of Waterborne Paints with Large Glass Beads
• Road and air temperatures should be 10oC and rising
• Relative humidity should be 85% Rh and decreasing.
• Evening and night applications should be avoided
• Paint should not be applied if dew is expected in 2 hours
• Paint should not be applied if precipitation is expected in 24 hours
• Spray application recommended, thinning normally not recommended.
• Substrate prepared by hand / mechanical brooming or use of high velocity / high pressure air
blowing to remove loose paint, dust and dirt
• Application by brush / roller not recommended
• Public roads and thoroughfares
• Recommended film thickness varies, dependent on proposed life and size of glass beads being
• 300 µm wet – approximately 200 µm dry – approximately 3.3 square metres / litre for drop on
beads [Source Damar Aqua 98]
• 500 µm wet – approximately 300 µm dry – approximately 2.0 square metres / litre for
Visibeads [Source Potters AU006]
• 650um wet – approximately 450um dry – approximately 1.6 square metres / litre for Elements
[Source 3M Wet Reflective Series 90 Elements]
• Asphalt designed for low traffic density e.g. car parks and tennis courts
• Higher application rates with traditional waterborne paints can lead to problems. As the paint
dries, it shrinks with a tendency to curl and tear the asphalt around the marking. Two applications at 75 µm wet – 45 µm dry may reduce the problem.
NZRF Roadmarking Materials Guide – Waterborne Paint
Manufacturing Process
• The coloured and extender pigments are intimately mixed into the binder, using a High Speed
Dispenser or similar machine and then "let down" with solvents and various chemical additives to form the finished paint
• After laboratory QC testing the paint is filtered and packaged, labelled, and issued with a
Standard QC Certificate confirming its conformity to NZTA requirements or APAS Specification.
Testing of Physical Properties
• Paint may be tested to NZTA specification M 7, AS 4049.3, AS 4049.4 and / or APAS
Handling, storage & packaging
• 20L plastic or lacquer lined steel pails, 200L plastic or lacquer lined steel drums & 500L and
• May be or not be classified Non-Hazardous according to NZ Dangerous Goods and Toxic
Substances Regulations [Source Resene SDS]
• Empty Drums not usually considered hazardous
• Storage temperatures 1oC to 40oC
• Avoid freezing, excessive heat and changes in temperature
• Incompatible substances are strong oxidisers and acids
• Paint transfer pumps must be of low shear type, e.g. diaphragm or piston pumps not gear
• Typical Classification – refer to product specific data sheets
• Shipping Name: NONE
• Transport Hazard Class: None, None
• UN/NA Number: None
• ADR Number: None
• Packing Group: None
Environmental Impacts
• VOC in the range of 100 to 150 gm/l
• Waterborne paints are extremely miscible in water, care must be taken to ensure that any
spills or cleaning materials do not enter or contaminate soil or waterways
• Refer to NZRF Roadmarking Note # 11 HSNO Regulations Emergency Management
Requirements - Guideline
• In the period of 1st April 2007 to 31st March 2009, at least 12 incidents related to paint, one of
which was roadmarking related, were reported to ERMA.
Occupational Health & Safety Hazards
• Fluid Injection via spray equipment
• Fumes, Gases, Vapours
• Potential to Poison
• Potential to Infection
• Lack of Oxygen (also Fumes vapours & Gases). Confined Spaces. Vapours are heavier than
air and may pool in depressions resulting in oxygen deficit.
NZRF Roadmarking Materials Guide – Waterborne Paint
Application Process
• Painted pavement markings are applied by an applicator which sprays paint from a fixed
nozzle, connected to paint supply system (typically a high pressure paint pump), while the applicator is driven at a uniform speed following the existing markings (or set-out spots in the case of new work)
• The applicator driver normally controls the entire process
• Tip size, fluid pressure, atomising air pressure, paint viscosity and paint temperature are all
critical to the appearance, consistency and performance of the product
• Paint application plant requires verification / calibration to ensure application requirements
are known. Refer to NZTA/NZRF T 8
• Paint dispensing equipment must be made with 304 or higher grade stainless steel or other
material that will not react with the paint and cause application or storage problems
• Paint may be heated to give optimum drying times. Paint temperatures used typically lie
between 35oC and 45oC. If heat exchangers are used, care needs to be taken to ensure that paint temperature does not go above 50oC
• For high pressure airless spray equipment, water based paint may need lower paint pump
pressures than solvent based paint
• With conventional spray equipment, water based paints may need higher paint and
atomisation pressures than solvent based paints
• Commonly used nylon lined hoses may degrade with waterborne paint and should be replaced
with Teflon lined hoses
• Single spray guns angled backwards by 5 to 10 degrees may assist with even line spread
• Double gun operation recommended for heavier film builds
• Equipment cleaned / flushed with water or mixture of water and methylated spirits (3/1 ratio)
or ammonia and / or detergent. Window cleaning solutions work well on tips and hose connections.
Process Monitoring Equipment
• Portable environmental measuring devices for temperature & humidity
• Paint application rate computers
• Electronic scales / bead bucket and stop watch for glass bead application rate
• Applicator speedometers, calibrated over range of applicator speeds
• Paint pressure and / or hydraulic/air pressure gauges
• Wet film gauges
• Bead application comparison plates.
Post-Application Measuring Equipment
• Non-destructive eddy current device such as the Elcometer and steel test plates for dry film
• Retroreflectometers
• Skid resistance testers.
NZRF Roadmarking Materials Guide – Waterborne Paint
Test Methods
• Colour, Dry Film thickness, Skid Resistance and Retroreflectivity tested to NZTA M 7,
NZTA M 20 and NZTA T 16
• Dry film in accordance with Appendix A of NZTA P 22
• Alternative dry film method provided in NZTA/NZRF T 8
• Retroreflectivity refer also to Glass Beads
• Skid Resistance refer also to Glass Beads and Angular Material.
Quick Reference Safety Guide
• Provide adequate ventilation during use
• Avoid contact with skin and eyes
• Avoid breathing the vapour and spray mist (may cause respiratory irritation). • Inhalation: Half face-piece class P1 Organic vapour respirator conforming to AS 1716
• Eye Protection: If spray mist is encountered, goggles conforming to AS 1337
• Skin Protection: Wear overalls and gloves. Gloves of neoprene, nitrile rubber or PVC
industrial-weight lined gauntlet as per NZS 5812:1982 4.5.2(b). Use of silicone free barrier cream.
• If fluid injection occurs, contact a Doctor immediately. Injection of paint or solvents into the
skin may cause serious injury both from traumatic compression of structures and inflammation and damage from the solvents or paint itself. It is important to treat the injury surgically as soon as possible.
• If inhaled, provide fresh air, rest and keep warm. If breathing shallow, give oxygen. Contact
a Doctor or Poisons Information Centre.
• If swallowed, DO NOT induce vomiting; give several glasses of water. Contact a Doctor or
Poisons Information Centre.
• If eye contact, wash with running water for at least 15 minutes. Seek medical attention.
• If skin contact, wash affected area thoroughly with soap and water. Wash contaminated
Recorded Environmental Hazards
Recorded Health & Safety Incidents
Related National / International Standard Specifications
• APAS 0041 – Australian Paint Approval Scheme Specification 0041, Pavement Marking
• AS 4049.4 – Paints and related materials – Pavement marking materials Part 4: High
performance pavement marking systems
• AS 4049.3 - Paints and related materials – Roadmarking materials, Part 3: Waterborne paint
for use with drop-on beads
• AS/NZS 1580 401.8 - Methods of test for paints and related materials
• EN 1871 – Roadmarking Materials – Physical properties
• EN 1436 - Roadmarking Material – Road marking performance for road users
• EN 1824 - Road marking materials. Road trials
• NZTA M 7 - Specification for Roadmarking Paints
• NZTA M 20 – Specification for Long-life Roadmarking Materials
NZRF Roadmarking Materials Guide – Waterborne Paint
Useful References
• Safety Data Sheets
Damar Industries (NZ) Ltd
Dulux Paints Ltd
Resene Paints Ltd
• Damar / Linaro Technical Data Sheets
Highway BST Roadmarking Paint
Linaro Linaqua QL 90 Waterborne Roadmarking Paint
Highway Aqua 98 Roadmarking Paint
• Roads and Traffic Authority (RTA) New South Wales - Chart for Dry Time of Waterborne
Paint found in "The Use of Waterborne Paints with Large Glass Beads"
• Rohm & Haas Ltd – "Water based Acrylic Road Marking Paints – A User's Guide"
• Prosign / Rohm & Haas Ltd – "The ecoprofile of Typhon paint"
• Potters Industries Pty Ltd – A new line marking system
• Ennis Paints – Guidelines for Using Waterborne Traffic Paint.
NZRF Roadmarking Materials Guide - Polymer Modified Solvent Based Paint
7 Polymer Modified Solvent Based Paint
General Description
• A solvent thinned quick drying pavement marking paint modified by the addition of polymers
to enhance particular performance characteristics
• Glass beads and / or reflective elements are surface applied to provide retroreflectivity where
• Note: As the selection of particular resins and the application of particular polymers may be
aimed at enhancing particular performance characteristics and or particular application environments, the manufacturer's technical data should be referred to for specific details.
•
Composition
• Various formulations provided by individual paint manufacturers
• May be covered by licence agreements and trade names/marks
• Typically 50 to 65 per cent volume solids
• Petroleum based solvents used in formulation.
• Solvent based formulation includes modified alkyd extenders.
Physical Properties
• Rapid drying – No pickup time 1-15 minutes as per AS/NZS 1580 401.8
• Self cleaning
• Colours: Range may include White, Yellow, & Black
• Formulations aimed at bead retention, durability and range of available application conditions.
• Solubility in water less than 50gm/l at 20oC
• Formulations may include those aimed at providing high bead retention strength.
Performance Properties
• Skid Resistance: not less than 45 BPN when tested in accordance with Appendix B of NZTA
• Retroreflectivity: No values available for un-beaded paint
• When tested in accordance with either Appendix B or Appendix C of NZTA M 7, the
retroreflectivity of a beaded test paint film after the required number of vehicle passes shall not be less than 100 mcd/m²/lux for white paint and 80 mcd/m²/lux for yellow paint
• Colour: White equal to or whiter than Y35 "Off White" (NZTA M 7), Yellow between Y13
"Vivid Yellow" and Y14 "Golden Yellow" of AS 2700S (NZTA M 7) or approximately match Y14, (AS 4049.3).
Durability
• Greater life than the traditional chlorinated rubber modified paints, performance may match
or better that of waterborne paints
• The polymers used are selected on the basis of their durability and UV resistance
• Thickness of application necessitates repeated application compared to "long life" materials;
however, this depends on traffic volumes, pavement surface and applied thickness
• In general the durability may range between 1 and 2 million vehicle passes. The durability
achieved is dependent on the polymers used, application thickness and the substrate to which the material is applied. Reference should be made to individual supplier data sheets.
NZRF Roadmarking Materials Guide - Polymer Modified Solvent Based Paint
Compatibility
• Can be used on most types of surfaces for longitudinal, transverse and other markings.
Adhesion
• Generally does not perform well on mechanically trowelled / polished concrete. All paints are
sensitive to the alkalinity of fresh concrete. Concrete curing agents may have adverse effect on paint adhesion. New concrete and asphalt should be aged for a minimum of 30 days prior to painting. Sealers and primers may be used
• Specific formulations may be available, aimed at providing good adhesion to particular
Application Parameters
• Markings must be protected from traffic until thoroughly dry. Refer to Manufacturer's
Technical Data Sheets
• Road and air temperatures should be 10oC and rising
• Relative humidity should be 85% Rh and decreasing.
• Paint should not be applied if dew is expected in 2 hours
• Precipitation in the 24hrs following application may adversely affect paint performance
• Spray application recommended, thinning normally not recommended
• Substrate prepared by hand / mechanical brooming or use of high velocity / high pressure air
blowing to remove loose paint, dust and dirt
• Application by brush / roller not recommended
• Public roads and thoroughfares
• Recommended film thickness varies dependent on proposed life and size of glass beads being
applied: Typical application rates include;
• 360 µm wet – approximately 200 µm dry – approximately 3 square metres / litre for drop on /
• 540 µm wet – approximately 300 µm dry – approximately 2 square metres / litre for
Visibeads / large beads
• Asphalt designed for low traffic density e.g. car parks and tennis courts
• Higher application rates can lead to problems. As the paint dries, it shrinks with a tendency to
curl and tear the asphalt around the marking. Two applications at 75 µm wet – 45 µm dry may reduce the problem
Manufacturing Process
• The coloured and extender pigments are intimately mixed into the binder, using a High Speed
Dispenser or similar machine and then "let down" with solvents and various chemical additives to form the finished paint
• After laboratory QC testing the paint is filtered and packaged, labelled, and issued with a
Standard QC Certificate confirming its conformity to NZTA requirements or APAS Specification.
•
Testing of Physical Properties
• Paint may be tested to NZTA specification M 7, AS 4049.1, AS 4049.4 and / or APAS.
NZRF Roadmarking Materials Guide - Polymer Modified Solvent Based Paint
Handling, storage & packaging
• 20L steel and plastic pails, 200L steel drums, 1000L Haztainers
• Storage temperatures 1oC to 40oC, store at a constant temperature
• High flammability. Dangerous goods stores generally needed. Hazardous Goods Licence
generally required for transport
• Take precautions against static electricity
• Incompatible substances are strong oxidizers, acids & alkalis
• Extinguishing Media include Foam, Carbon Dioxide, Dry Chemical
• Typical Classification – refer to product specific data sheets
• Dangerous Goods Class 3.1b
• Haz Chem Code 3[Y]E
• UN Number 1263
• Packaging Group II
• Flash Point Less than 23oC
• Third on Toxic Substances Schedule.
Environmental Impacts
• VOC in the range of 400 to 500 gm/l
• High flammability, fumes heavier than air, can create explosion potential in enclosed spaces
• Heavier than water with low solubility in water
• Refer to NZRF Roadmarking Note # 11 HSNO Regulations Emergency Management
Requirements - Guideline
• In the period of 1st April 2007 to 31st March 2009, at least 12 incidents related to paint, one of
which was roadmarking related, were reported to ERMA.
Occupational Health & Safety Hazards
• Fluid Injection
• Fire and explosion
• Hazardous decomposition products on burning
• Fumes, Gases, Vapours
• Potential to Poison
• Potential to Infection
• Lack of Oxygen (also Fumes vapours & Gases). Confined Spaces. Vapours are heavier than
air and may pool in depressions resulting in oxygen deficiencies
• Repeated and prolonged occupational overexposure to solvents can damage liver, brain and
central nervous system.
Application Process
• Painted pavement markings are applied by an applicator which sprays paint from a fixed
nozzle, connected to paint supply system (typ ically a high pressure paint pump), while the applicator is driven at a uniform speed following the existing markings (or set-out spots in the case of new work)
• The applicator driver normally controls the entire process.
• Tip size, fluid pressure, atomising air pressure, paint viscosity and paint temperature are all
critical to the appearance, consistency and performance of the product
NZRF Roadmarking Materials Guide - Polymer Modified Solvent Based Paint
• Paint application plant requires verification / calibration to ensure application requirements
are known. Refer to NZTA/NZRF T 8
• Single spray guns angled backwards by 5 to 10 degrees may assist with even line spread
• The compatibility of each particular product with other roadmarking paints may vary
significantly from product to product. Manufacturer's flushing and thinning procedures need to be strictly adhered to.
Process Monitoring Equipment
• Paint application rate computers
• Electronic scales for glass bead application rate
• Speedometers
• Paint pressure and or hydraulic/air pressure gauges
• Wet film gauges
• Bead application comparison plates.
Post-Application Measuring Equipment
• Dry Film Thickness measured using non-destructive eddy current device such as the
• Steel test plates
• Retroreflectometers
• Skid resistance testers
Test Methods
• Dry Film thickness, Skid Resistance and Retroreflectivity tested to either NZTA P 12,
• Dry film in accordance with Appendix A of NZTA P 12 / P 22
• Dry film in accordance with NZTA/NZRF T 8
• Retroreflectivity refer to Glass Beads
• Skid Resistance refer also to Glass Beads and Angular Material.
Quick Reference Safety Guide
• Provide adequate ventilation during use
• Keep away from heat and naked flame
• Avoid contact with skin and eyes
• Avoid breathing the vapour and spray mist
• Wash hands in soap and water prior to eating or smoking • Inhalation: Organic vapour respirator conforming to AS 1716
• Eye Protection: If spray mist is encountered, goggles conforming to AS 1337
• Skin Protection: Wear overalls and gloves. Use of silicone free barrier cream.
NZRF Roadmarking Materials Guide - Polymer Modified Solvent Based Paint
• If fluid injection occurs, contact a Doctor immediately. Injection of paint or solvents into the
skin may cause serious injury both from traumatic compression of structures and inflammation and damage from the solvents or paint itself. It is important to treat the injury surgically as soon as possible.
• If inhaled, provide fresh air, rest and keep warm. If breathing shallow, give oxygen. Contact
a Doctor or Poisons Information Centre.
• If swallowed, DO NOT induce vomiting, give several glasses of water. Contact a Doctor or
Poisons Informa tion Centre.
• If eye contact, wash with running water for at least 15 minutes. Seek medical attention.
Recorded Environmental Hazards
Recorded Health & Safety Incidents
Related National / International Standard Specifications
• APAS 0041 – Australian Paint Approval Scheme Specification 0041, Pavement Marking
• AS 4049.4 – Paints and related materials – Pavement marking materials Part 4: High
performance pavement marking systems
• AS 4049.3 - Paints and related materials – Roadmarking materials, Part 3: Waterborne paint
for use with drop-on beads
• AS/NZS 1580 401.8 - Methods of test for paints and related materials
• EN 1871 – Roadmarking Materials – Physical properties
• EN 1436 - Roadmarking Material – Road marking performance for road users
• EN 1824 - Road marking materials. Road trials
• NZTA M 7 - Specification for Roadmarking Paints
• NZTA M 20 – Specification for Long-life Roadmarking Materials
Useful References
• Safety Data Sheets and Technical Data Sheets
Damar Industries (NZ) Ltd
Linaro Paints (NZ) Ltd
• Damar / Linaro Technical Data Sheet
Linaro Ultrax CL Speciality Alkyd Modified Roadmarking Paint
• SADOT MAT TP901 – South Australia Department of Australia Determination of Wet Film
Thickness of Road Marking Paint / Glass Bead Application Rate, Plastic Bag Method
NZRF Roadmarking Materials Guide - Chlorinated Rubber Modified Alkyd Paint
8 Chlorinated Rubber Modified Alkyd Paint
General Description
• A high-solids alkyd, solvent thinned quick drying pavement marking paint modified by the
addition of chlorinated rubber
• Glass beads and / or reflective elements are surface applied to provide retroreflectivity where
• Note: this paint is not classified as "chlorinated-rubber" paint.
Composition
• Typically 45 to 65 per cent volume solids.
• Petroleum based solvents used in formulation.
• Solvent based formulation includes modified alkyd extenders
• Normally thinned with aromatic hydrocarbons.
Physical Properties
• Fast drying – No pickup time 7-15minutes as per AS/NZS 1580 401.8
• Self cleaning
• Colours: Full range including White, Yellow, & Black
• Appears to hold beads well, although typical application rates will not hold large beads
• Solubility in water less than 50gm/l at 20oC.
Performance Properties
• Skid Resistance: not less than 45 BPN when tested in accordance with Appendix B of NZTA
• Retroreflectivity: No values available for un-beaded paint
• When tested in accordance with either Appendix B or Appendix C of NZTA M 7, the
retroreflectivity of a beaded test paint film after the required number of vehicle passes shall not be less than 100 mcd/m²/lux for white paint and 80 mcd/m²/lux for yellow paint
• Colour: White equal to or whiter than Y35 "Off White" (NZTA M 7), Yellow between Y13
"Vivid Yellow" and Y14 "Golden Yellow" of AS 2700S (NZTA M 7) or approximately match Y14, (AS 4049.3).
•
Durability
• Greater life than the unmodified alkyd paints
• The addition of the chlorinated rubber modifiers reduces the rate at which the alkyd paint
becomes harder and more brittle as it ages
• Thickness of application necessitates repeated application compared to "long life" materials,
however, this depends on traffic volumes, pavement surface and applied thickness
• When applied at 180 µm dry, performance is generally less than 1.5 million vehicle passes
when tested in accordance with NZTA M 7 – Refer to latest version of NZTA M 7 Notes.
Compatibility
Can be used on most types of surfaces for longitudinal, transverse and other markings.
NZRF Roadmarking Materials Guide - Chlorinated Rubber Modified Alkyd Paint
Adhesion
• Does not perform well on mechanically trowelled / polished concrete. All paints are sensitive
to the alkalinity of fresh concrete. Concrete curing agents may have adverse effect on paint adhesion. New concrete and asphalt should be aged for a minimum of 30 days prior to painting. Sealers and primers may be used.
•
Application Parameters
• Spray application recommended, thinning normally not required / desirable
• Substrate prepared by hand / mechanical brooming or use of high velocity / high pressure air
blowing to remove loose paint, dust and dirt
• Application by brush / roller not recommended
• Public roads and thoroughfares
• Recommended film thickness 270 µm wet. 170 µm dry – approximately 3.7 square metres /
litre [Source Wattyl Streamline]
• Asphalt designed for low traffic density e.g. car parks and tennis courts
• Higher application rates can lead to problems. As the paint dries, it shrinks with a tendency to
curl and tear the asphalt around the marking. Two applications at 75 µm wet – 45 µm dry may reduce the problem.
•
Manufacturing Process
• The coloured and extender pigments are intimately mixed into the binder, using a High Speed
Dispenser or similar machine and then "let down" with solvents and various chemical additives to form the finished paint
• After laboratory QC testing the paint is filtered, packaged, labelled and issued with a Standard
QC Certificate confirming its conformity to NZTA requirements or APAS Specification.
Testing of Physical Properties
• Paint may be tested to NZTA specification M 7, AS 4049.1, AS4049.4 and/or APAS.
Handling, storage & packaging
• 20L steel pails, 200L recycled steel drums, 1000L Haztainers
• Storage temperatures 1oC to 40oC, store at a constant temperature
• High flammability. Dangerous goods stores generally needed. Hazardous Goods Licence
generally required for transport.
• Take precautions against static electricity.
• Typical Classification – refer to product specific data sheets
• Dangerous Goods Class 3.2
• Haz Chem Code 3[Y]E
• UN Number 1263
• Packaging Group II
• Incompatible substances are strong oxidisers, acids & alkalis
• Flash Point Less than 23oC
• Extinguishing Media include Foam, Carbon Dioxide, Dry Chemical
• Third on Toxic Substances Schedule.
NZRF Roadmarking Materials Guide - Chlorinated Rubber Modified Alkyd Paint
Environmental Impacts
• VOC in the range of 400 to 500gm/l
• High flammability, fumes heavier than air, can create explosion potential in enclosed spaces
• Heavier than water with low solubility in water.
• Refer to NZRF Roadmarking Note # 11 HSNO Regulations Emergency Management
Requirements - Guideline
Occupational Health & Safety Hazards
• Fluid Injection
• Fire and explosion
• Hazardous decomposition products on burning
• Fumes, Gases, Vapours
• Potential to Poison
• Potential to Infection
• Lack of Oxygen (also Fumes vapours & Gases). Confined Spaces. Vapours are heavier than
air and may pool in depressions resulting in oxygen deficiencies
• Repeated and prolonged occupational overexposure to solvents can damage liver, brain and
central nervous system.
Application Process
• Painted pavement markings are applied by an applicator which sprays paint from a fixed
nozzle, connected to paint supply system (typically a high pressure paint pump), while the applicator is driven at a uniform speed following the existing markings (or set-out spots in the case of new work)
• The applicator driver normally controls the entire process
• Tip size, fluid pressure, atomising air pressure, paint viscosity and paint temperature are all
critical to the appearance, consistency and performance of the product
• Paint application plant requires verification / calibration to ensure application requirements
are known. Refer to NZTA/NZRF T 8
• Single spray guns angled backwards by 5 to 10 degrees may assist with even line spread.
• Equipment cleaned / flushed with thinners such as Toluene.
Process Monitoring Equipment
• Paint application rate computers
• Electronic scales for glass bead application rate
• Speedometers
• Paint pressure and or hydraulic/air pressure gauges
• Wet film gauges
• Bead application comparison plates.
Post-Application Measuring Equipment
• Dry Film Thickness measured using non-destructive eddy current device such as the
• Steel test plates
• Retroreflectometers
• Skid resistance testers.
NZRF Roadmarking Materials Guide - Chlorinated Rubber Modified Alkyd Paint
Test Methods
• Dry Film thickness, Skid Resistance and Retroreflectivity tested to NZTA P 12, NZTA P 20
• Dry film in accordance with Appendix A of NZTA P 12
• Dry film in accordance with NZTA/NZRF T 8
• Retroreflectivity refer to Glass Beads
• Skid Resistance refer also to Glass Beads and Angular Material.
Quick Reference Safety Guide
• Provide adequate ventilation during use
• Keep away from heat and naked flame
• Avoid contact with skin and eyes
• Avoid breathing the vapour and spray mist
• Wash hands in soap and water prior to eating or smoking. • Inhalation: Organic vapour respirator conforming to AS 1716:1994
• Eye Protection: If spray mist is encountered, goggles conforming to AS 1337:1992
• Skin Protection: Wear overalls and gloves. Use of silicone free barrier cream. • If fluid injection occurs, contact a Doctor immediately. Injection of paint or solvents into the
skin may cause serious injury both from traumatic compression of structures and inflammation and damage from the solvents or paint itself. It is important to treat the injury surgically as soon as possible
• If inhaled, provide fresh air, rest and keep warm. If breathing shallow, give oxygen. Contact
a Doctor or Poisons Information Centre
• If swallowed, DO NOT induce vomiting; give several glasses of water. Contact a Doctor or
Poisons Informa tion Centre
• If eye contact, wash with running water for at least 15 minutes. Seek medical attention.
Recorded Environmental Hazards
Recorded Health & Safety Incidents
Related National / International Standard Specifications
• APAS 0041 – Australian Paint Approval Scheme Specification 0041, Pavement Marking
• AS 4049.4 – Paints and related materials – Pavement marking materials Part 4: High
performance pavement marking systems
• AS 4049.3 - Paints and related materials – Roadmarking materials, Part 3: Waterborne paint
for use with drop-on beads
• AS/NZS 1580 401.8 - Methods of test for paints and related materials
• EN 1871 – Roadmarking Materials – Physical properties
• EN 1436 - Roadmarking Material – Road marking performance for road users
• EN 1824 - Road marking materials. Road trials
• NZTA M 7 - Specification for Roadmarking Paints
NZRF Roadmarking Materials Guide - Chlorinated Rubber Modified Alkyd Paint
Useful References
• Safety Data Sheets
Damar Industries (NZ) Ltd
Dulux Paints Ltd
Resene Paints Ltd
• Damar Technical Data Sheet
Highway Beadlock
• Department of Labour Publication "Practical Guidelines for the Safe Use of Organic
• Health Safety & Environment Guide for Printing & Related Industries -
NZRF Roadmarking Materials Guide - Alkyd Paint
9 Alkyd Paint
General Description
• An alkyd, solvent thinned quick drying pavement marking paint
• Glass beads and / or reflective elements are surface applied to provide retroreflectivity where
Composition
• Typically 55 to 65 per cent volume solids for high solids alkyds
• Typically 45 to 55 per cent volume solids for low solids alkyds
• Petroleum based solvents used in formulation
• Thinned with organic solvents such as Toluene.
Physical Properties
• Fast drying – No pickup time 7-15minutes as per AS/NZS 1580 401.8
• Self cleaning
• Colours: Full range including White, Yellow, & Black
• Does not hold beads well, although high solids alkyd holds beads better than low solids alkyd.
Typical application rates will not hold large beads
• Solubility in water less than 50gm/l at 20oC.
Performance Properties
• Skid Resistance: not less than 45 BPN when tested in accordance with Appendix B of NZTA
• Retroreflectivity: No values available for un-beaded paint
• When tested in accordance with either Appendix B or Appendix C of NZTA M 7, the
retroreflectivity of a beaded test paint film after the required number of vehicle passes shall not be less than 100 mcd/m²/lux for white paint and 80 mcd/m²/lux for yellow paint
• Colour: White equal to or whiter than Y35 "Off White" (NZTA M 7), Yellow between Y13
"Vivid Yellow" and Y14 "Golden Yellow" of AS 2700S (NZTA M 7) or approximately match Y14, (AS 4049.3).
•
Durability
• Lowest life of all marking materials - highest life cycle cost
• Material becomes harder and more brittle as it ages
• Thickness of application necessitates repeated application compared to "long life" materials,
however, this depends on traffic volumes, pavement surface and applied thickness
• When applied at 180 µm dry performance is generally less than 1 million vehicle passes
when tested in accordance with NZTA M 7– Refer to NZTA M 7 Notes
• May be used as temporary marking prior to application of "long life" materials.
Compatibility
Can be used on most types of surfaces for longitudinal, transverse and other markings.
NZRF Roadmarking Materials Guide - Alkyd Paint
Adhesion
• Does not perform well on mechanically trowelled / polished concrete. All paints are sensitive
to the alkalinity of fresh concrete. Concrete curing agents may have adverse effect on paint adhesion. New concrete and asphalt should be aged for a minimum of 30 days prior to painting. Sealers and primers may be used.
•
Application Parameters
• Spray application recommended, thinning normally not required / desirable
• Substrate prepared by hand / mechanical brooming or use of high velocity / high pressure air
blowing to remove loose paint, dust and dirt
• Application by brush / roller not recommended
• Public roads and thoroughfares
• Recommended film thickness 270 µm wet. 170 µm dry – approximately 3.7 square metres /
litre [Source Wattyl Streamline]
• Asphalt designed for low traffic density e.g. car parks and tennis courts
• Higher application rates can lead to problems. As the paint dries, it shrinks with a tendency to
curl and tear the asphalt around the marking. Two applications at 75 µm wet – 45 µm dry may reduce the problem.
Manufacturing Process
• The coloured and extender pigments are intimately mixed into the binder, using a High Speed
Dispenser or similar machine and then "let down" with solvents and various chemical additives to form the finished paint
• After laboratory QC testing the paint is filtered, packaged, labelled and issued with a Standard
QC Certificate confirming its conformity to NZTA requirements or APAS Specification.
Testing of Physical Properties
• Paint may be tested to NZTA specification M 7, AS 4049.1 and / or APAS.
Handling, storage & packaging
• 20L steel pails, 200L recycled steel drums, 1000L Haztainers
• Storage temperatures 1oC to 40oC, store at a constant temperature
• High flammability. Dangerous goods stores generally needed. Hazardous Goods Licence
generally required for transport.
• Take precautions against static electricity.
• Typical Classification – refer to product specific data sheets
• Dangerous Goods Class 3.2
• Haz Chem Code 3[Y]E
• UN Number 1263
• Packaging Group II
• Incompatible substances are strong oxidisers, acids & alkalis
• Flash Point Less than 23oC
• Extinguishing Media include Foam, Carbon Dioxide, Dry Chemical
• Third on Toxic Substances Schedule.
NZRF Roadmarking Materials Guide - Alkyd Paint
Environmental Impacts
• VOC in the range of 400 to 500gm/l
• High flammability, fumes heavier than air, can create explosion potential in enclosed spaces
• Heavier than water with low solubility in water
• Refer to NZRF Roadmarking Note # 11 HSNO Regulations Emergency Management
Requirements - Guideline
• In the period of 1st April 2007 to 31st March 2009, at least 12 incidents related to paint, one of
which was roadmarking related, were reported to ERMA.
Occupational Health & Safety Hazards
• Fluid Injection
• Fire and explosion
• Hazardous decomposition products on burning
• Fumes, Gases, Vapours
• Potential to Poison
• Potential to Infection
• Lack of Oxygen (also Fumes vapours & Gases). Confined Spaces. Vapours are heavier than
air and may pool in depressions resulting in oxygen deficiencies
• Repeated and prolonged occupational overexposure to solvents can damage liver, brain and
central nervous system.
Application Process
• Painted pavement markings are applied by an applicator which sprays paint from a fixed
nozzle, connected to paint supply system (typically a high pressure paint pump), while the applicator is driven at a uniform speed following the existing markings (or set-out spots in the case of new work)
• The applicator driver normally controls the entire process
• Tip size, fluid pressure, atomising air pressure, paint viscosity and paint temperature are all
critical to the appearance, consistency and performance of the product
• Paint application plant requires verification / calibration to ensure application requirements
are known. Refer to NZTA/NZRF T 8
• Single spray guns angled backwards by 5 to 10 degrees may assist with even line spread
• Equipment cleaned / flushed with thinners such as Toluene
Process Monitoring Equipment
• Paint application rate computers
• Electronic scales for glass bead application rate
• Speedometers
• Paint pressure and or hydraulic/air pressure gauges
• Wet film gauges
• Bead application comparison plates.
NZRF Roadmarking Materials Guide - Alkyd Paint
Post-Application Measuring Equipment
• Dry Film Thickness measured using non-destructive eddy current device such as the
• Steel test plates
• Retroreflectometers
• Skid resistance testers.
Test Methods
• Dry Film thickness, Skid Resistance and Retroreflectivity tested to NZTA P 12, NZTA P 20,
• Dry film in accordance with NZTA/NZRF T 8
• Retroreflectivity refer to Glass Beads
• Skid Resistance refer also to Glass Beads and Angular Material.
Quick Reference Safety Guide
• Provide adequate ventilation during use
• Keep away from heat and naked flame
• Avoid contact with skin and eyes
• Avoid breathing the vapour and spray mist
• Wash hands in soap and water prior to eating or smoking. • Inhalation: Organic vapour respirator conforming to AS 1716:1994
• Eye Protection: If spray mist is encountered, goggles conforming to AS 1337:1992
• Skin Protection: Wear overalls and gloves. Use of silicone free barrier cream • If fluid injection occurs, contact a Doctor immediately. Injection of paint or solvents into the
skin may cause serious injury both from traumatic compression of structures and inflammation and damage from the solvents or paint itself. It is important to treat the injury surgically as soon as possible.
• If inhaled, Provide fresh air, rest and keep warm. If breathing shallow, give oxygen. Contact
a Doctor or Poisons Information Centre.
• If swallowed, DO NOT induce vomiting; give several glasses of water. Contact a Doctor or
Poisons Information Centre.
• If eye contact, wash with running water for at least 15 minutes. Seek medical attention.
Recorded Environmental Hazards
Recorded Health & Safety Incidents
NZRF Roadmarking Materials Guide - Alkyd Paint
Related National / International Standard Specifications
• APAS 0041 – Australian Paint Approval Scheme Specification 0041, Pavement Marking
• AS 4049.4 – Paints and related materials – Pavement marking materials Part 4: High
performance pavement marking systems
• AS 4049.3 - Paints and related materials – Roadmarking materials, Part 3: Waterborne paint
for use with drop-on beads
• AS/NZS 1580 401.8 - Methods of test for paints and related materials
• EN 1871 – Roadmarking Materials – Physical properties
• EN 1436 - Roadmarking Material – Road marking performance for road users
• EN 1824 - Road marking materials. Road trials
• NZTA M 7 - Specification for Roadmarking Paints
NZRF Roadmarking Materials Guide - Alkyd Paint
Useful References
• Safety Data Sheets
Damar Industries Ltd
Dulux Paints Ltd
Resene Paints Ltd
• Damar Technical Data Sheets
Highway Alkyd HP98 Roadmarking Paint
Highway Super Alkyd
• Department of Labour Publication "Practical Guidelines for the Safe Use of Organic
• Health Safety & Environment Guide for Printing & Related Industries -
NZRF Roadmarking Materials Guide - Temporary / Removable Paint
10 Temporary / Removable Paint
General Description
• A high-solids quick drying water-based acrylic pavement marking paint specifically
formulated for temporary / removable paint applications for such events as Santa parades, street racing, etc.
• Material is applied as for traditional waterborne roadmarking paint but is removed after use
by the application of a "neutraliser"
• Products manufactured / distributed under licence
• Glass beads and / or reflective elements are surface applied to provide retroreflectivity where
Composition - Paint
• Typically 60 to 68 per cent volume solids
• Water miscible solvents used in formulation
• Thinned with water-based thinners.
Composition – Neutraliser
• Aminomethyl propanol
• Ethanol
Physical Properties - Paint
• Drying time dependent on film thickness, relative humidity, temperature and airflow.
• Self cleaning
• Colours: Full range including White, Yellow, & Black
• Holds beads better than solvent based paints, particularly large beads
• pH of approximately 10
• High miscibility in water.
• Physical Properties – Neutraliser
• Clear colourless liquid having alcoholic solvent odour
• Flash point 23ºC
• Insoluble in water.
•
Performance Properties
• Skid Resistance: not less than 45 BPN when tested in accordance with Appendix B of
• Retroreflectivity: No values available for un-beaded paint
• When tested in accordance with either Appendix B or Appendix C of NZTA M 7, the
retroreflectivity of a beaded test paint film after the required number of vehicle passes shall not be less than 100 mcd/m²/lux for white paint and 80 mcd/m²/lux for yellow paint
• Colour: White equal to or whiter than Y35 "Off White" (NZTA M 7), Yellow between Y13
"Vivid Yellow" and Y14 "Golden Yellow" of AS 2700S (NZTA M 7) or approximately match Y14, (AS 4049.3).
NZRF Roadmarking Materials Guide - Temporary / Removable Paint
•
Durability
• The durability is reported variously as between three months and two years
• Section 15 of the Hamilton City Council Development Manual requires a minimum "life" of
Compatibility
• Can be used on most types of surfaces for longitudinal, transverse and other markings
• No compatibility problems observed. Water based paint appears to adhere well to
thermoplastic, solvent based paint and to itself.
• Should not be applied on metal substrates without the use of an appropriate anticorrosive
Adhesion
• Does not perform well on mechanically trowelled / polished concrete. All paints are sensitive
to the alkalinity of fresh concrete. Concrete curing agents may have adverse effect on paint adhesion. New concrete and asphalt should be aged for a minimum of 30 days prior to painting. Sealers and primers may be used.
Application Parameters
• Markings must be protected from traffic until thoroughly dry. Refer to Chart for Dry Time of
Waterborne Paint contained in RTA Use of Waterborne Paints with Large Glass Beads
• Road and air temperatures should be 10oC and rising
• Relative humidity should be 85% Rh and decreasing.
• Evening and night applications should be avoided
• Paint should not be applied if dew is expected in 2 hours
• Paint should not be applied if precipitation is expected in 24 hours
• Spray application recommended, thinning normally not recommended.
• Substrate prepared by hand / mechanical brooming or use of high velocity / high pressure air
blowing to remove loose paint, dust and dir t.
• Application by brush / roller not recommended.
• Public roads and thoroughfares
• Recommended film thickness varies dependent on proposed life and size of glass beads being
• 300 µm wet – approximately 200 µm dry – approximately 3.3 square metres / litre for drop on
beads [Source Damar Aqua 98]
• 500 µm wet – approximately 300 µm dry – approximately 2.0 square metres / litre for
Visibeads [Source Potters AU006]
•
Manufacturing Process
• The coloured and extender pigments are intimately mixed into the binder, using a High Speed
Dispenser or similar machine and then "let down" with solvents and various chemical additives to form the finished paint
• After laboratory QC testing the paint is filtered and filled into its appropriate packaging, it is
then labelled and issued with a Standard QC Certificate confirming its conformity to NZTA requirements or APAS Specification.
NZRF Roadmarking Materials Guide - Temporary / Removable Paint
Testing of Physical Properties
• Paint may be tested to New Zealand Transport Agency specification M 7, AS 4049.3,
AS 4049.4 and / or APAS.
Handling, storage & packaging
• 20L plastic or lacquer lined steel pails
• Empty Drums not usually considered hazardous
• Storage temperatures 1oC to 40oC
• Avoid freezing, excessive heat and changes in temperature
• Incompatible substances are strong oxidisers, & acids
• Paint transfer pumps must be of low shear type, e.g. diaphragm or piston pumps not gear
• Typical Classification – refer to product specific data sheets
• Shipping Name: NONE
• Transport Hazard Class: None, None
• UN/NA Number: None
• ADR Number: None
• Packing Group: None
Environmental Impacts
• Lower VOC's than solvent based paints, in the range of 100 to 150 gm/l
• Waterborne paints are extremely miscible in water, care must be taken to ensure that any
spills or cleaning materials do not enter or contaminate soil or waterways
• In the period of 1st April 2007 to 31st March 2009, at least 12 incidents related to paint, one of
which was roadmarking related, were reported to ERMA.
Occupational Health & Safety Hazards
• Fluid Injection via spray equipment
• Fumes, Gases, Vapours
• Potential to Poison
• Potential to Infection
• Lack of Oxygen (also Fumes vapours & Gases). Confined Spaces. Vapours are heavier than
air and may pool in depressions resulting in oxygen deficit.
Application Process
• Painted pavement markings are applied by an applicator which sprays paint from a fixed
nozzle, connected to paint supply system (typically a high pressure paint pump), while the applicator is driven at a uniform speed following the existing markings (or set-out spots in the case of new work)
• The applicator driver normally controls the entire process
• Tip size, fluid pressure, atomising air pressure, paint viscosity and paint temperature are all
critical to the appearance, consistency and performance of the product
• Paint application plant requires verification / calibration to ensure application requirements
are known. Refer to NZTA/NZRF T 8
• Paint dispensing equipment must be made with 304 or higher grade stainless steel or other
material that will not react with the paint and cause application or storage problems
• Paint may be heated to give optimum drying times. Paint temperatures used typically lie
between 35oC and 45oC. If heat exchangers are used, care needs to be taken to ensure that paint temperature does not go above 50oC
NZRF Roadmarking Materials Guide - Temporary / Removable Paint
• For high pressure airless spray equipment, water based paint may need lower paint pump
pressures than solvent based paint
• With conventional spray equipment, water based paints may need higher paint and
atomisation pressures than solvent based paints
• Commonly used nylon lined hoses may degrade with waterborne paint and should be replaced
with Teflon lined hoses
• Single spray guns angled backwards by 5 to 10 degrees may assist with even line spread.
• Double gun operation recommended for the heavier film builds
• Equipment cleaned / flushed with water or mixture of water and methylated spirits (3/1 ratio)
or ammonia and / or detergent. Window cleaning solutions work well on tips and hose connections.
Removal Process
• Neutralising gel / liquid is applied and left for a period of time (minimum 15 min)
• Marking is flooded with water
• Marking is scarified with hand or mechanical broom to loosen paint
• Marking is left to stand for further period of time to loosen paint
• Paint is removed using medium pressure water jet or water truck
• Process repeated as necessary, although small quantities left will deteriorate with time
• Detergent / surfactant may be used to complete cleaning process
• Area is cleaned up using vacuum sweeper.
Process Monitoring Equipment
• Portable environmental measuring devices for temperature & humidity
• Paint application rate computers
• Electronic scales / bead bucket and stop watch for glass bead application rate
• Applicator speedometers, calibrated over range of applicator speeds
• Paint pressure and or hydraulic/air pressure gauges
• Wet film gauges
• Bead application comparison plates.
Post-Application Measuring Equipment
• Non-destructive eddy current device such as the Elcometer and steel test plates for dry film
• Retroreflectometers
• Skid resistance testers
Test Methods
• Colour, Dry Film thickness, Skid Resistance and Retroreflectivity tested to NZTA M 7,
NZTA M 20 and NZTA T 16.
• Dry film in accordance with Appendix A of NZTA P 22
• Alternative dry film method provided in NZTA/NZRF T 8
• Retroreflectivity refer also to Glass Beads
• Skid Resistance refer also to Glass Beads and Angular Material.
NZRF Roadmarking Materials Guide - Temporary / Removable Paint
Quick Reference Safety Guide
• Provide adequate ventilation during use
• Avoid contact with skin and eyes
• Avoid breathing the vapour and spray mist (may cause respiratory irritation). • Inhalation: Half face-piece class P1 Organic vapour respirator conforming to AS 1716
• Eye Protection: If spray mist is encountered, goggles conforming to AS 1337
• Skin Protection: Wear overalls and gloves. Gloves of neoprene, nitrile rubber or PVC
industrial weight lined gauntlet as per NZS 5812:1982 4.5.2(b). Use of silicone free barrier cream
• If fluid injection occurs, contact a Doctor immediately. Injection of paint or solvents into the
skin may cause serious injury both from traumatic compression of structures and inflammation and damage from the solvents or paint itself. It is important to treat the injury surgically as soon as possible.
• If inhaled, provide fresh air, rest and keep warm. If breathing shallow, give oxygen. Contact
a Doctor or Poisons Information Centre.
• If swallowed, DO NOT induce vomiting; give several glasses of water. Contact a Doctor or
Poisons Information Centre.
• If eye contact, wash with running water for at least 15 minutes. Seek medical attention.
• If skin contact, wash affected area thoroughly with soap and water. Wash contaminated
Recorded Environmental Hazards
Recorded Health & Safety Incidents
Related National / International Standard Specifications
• APAS 0041 – Australian Paint Approval Scheme Specification 0041, Pavement Marking
• AS 4049.4 – Paints and related materials – Pavement marking materials Part 4: High
performance pavement marking systems
• AS 4049.3 - Paints and related materials – Roadmarking materials, Part 3: Waterborne paint
for use with drop-on beads
• AS/NZS 1580 401.8 - Methods of test for paints and related materials
• EN 1871 – Roadmarking Materials – Physical properties
• EN 1436 - Roadmarking Material – Road marking performance for road users
• EN 1824 - Road marking materials. Road trials
• NZTA M 7 - Specification for Roadmarking Paints
Useful References
• Mobile Colors, United Kingdom - www.mobile-colors.co.uk/products/removable-paint-
• Traffic Tech, NSW, Australia
• Ennis Paints – Guidelines for Using Waterborne Traffic Paint
• Safety Data Sheets
Mobile Colors Removable Paint
Mobile Colors Universal Remover
NZRF Roadmarking Materials Guide - Cold-Applied Plastic
11 Cold-Applied Plastic
General Description
• A cold hardening poly methyl methacrylate (PMMA) resin combined with aggregates and
fillers to produce a pourable solution which is virtually 100% solids
• Also known as acrylic glass
• Material is catalysed by the application of benzoyl peroxide in ether liquid or powder form
• Glass beads and / or reflective elements are applied as a subsequent operation to provide
retroreflectivity
• Alternatively aggregate may be applied as a subsequent operation to produce an overlay
surface with appropriate colour and skid resistance.
Composition
• PMMA roadmarking material is tailored for specific application methods such as audio-tactile
profiled (ATP) markings, structured markings and plain flat markings
• Products are covered by patents and licencing agreements
• Poly methyl methacrylate (PMMA) resin
• Typically virtually 100 per cent volume solids.
• Contains titanium dioxide, inorganic and organic colour pigments
Physical Properties
• High elasticity
• Fast drying – "No-pickup" time 7-15 minutes as per AS/NZS 1580 401.8. "Dry-through"
times in the range of 15 to 20 minutes. Drying time dependent on relative humidity, temperature and airflow, i.e. 15 minutes at 20oC
• Colours: White and Yellow, with others available on request.
Performance Properties
• Retroreflectivity: Dependent on the size and application rate of beads
• Luminance: White not less than 65, Yellow not less than 45 when tested in accordance with
• Colour: White equal to or whiter than Y35 "Off White" (NZTA M 20), Yellow between Y13
"Vivid Yellow" and Y14 "Golden Yellow" of AS 2700S (NZTA M 20) or approximately match Y14, (AS 4049.3).
• Skid Resistance: Commonly formulated to have skid resistance greater than or equal to 40
• Material can only be tested in flat format as ATP dimensions are less than sweep of, and their
shape reduces accuracy, of British Pendulum Tester results.
• Retroreflectivity / skid should not be measured immediately after application due to the
presence of process components on the material. Trafficking is advised prior to testing.
NZRF Roadmarking Materials Guide - Cold-Applied Plastic
Durability
• Regarded as "long life" as far as "wear" is concerned
• Retroreflective performance durability will be relative to the durability of the glass beads or
reflective elements used but will likely be less than the durability of the material
• NZTA requires all ATP markings to be high performance markings in accordance with
• Very useful in high wear areas, but soiling of the marking may occur in certain
Compatibility
• Can be used on many types of surfaces and for longitudinal, transverse and other markings.
• Not recommended for application on paving stones or bricks.
• Application to thermoplastic requires pre-application tests.
Adhesion
• Can be applied to most surfaces and textures. Concrete needs priming. New concrete and
asphalt should be aged for a minimum of 30 days prior to painting. Sealers and primers may be used.
Application Parameters
• Both components need to be thoroughly stirred. It is recommended that the component
containing the hardener is machine stirred
• Road and air temperatures should be in the range of 5 to 30oC and rising
• Recommended application rates of between 0.85 to 1 kg/m2
• Application by specially built / modified airless spray applicators recommended
• Applications require attention for skid resistance
• Application of hardener must be rigorously monitored to ensure application to entire marking.
Manufacturing Process
Testing of Physical Properties
• NZTA M 20 and AS 4049.4
Handling, storage & packaging
• Available in a variety of containers from 25 to 1500 kg
• Flammable - attention needed to storage and transport requirements. Dangerous goods store
and licences may be required
• Store in cool dry place protected from rain, sun and moisture
• Protect from excessive heat or contamination from fuels, oils or greases
• Typical Classification – refer to product specific data sheets
• Shipping Name: PAINT
• Transport Hazard Class: 3
• UN/NA Number: 1263
• Packing Group: II
NZRF Roadmarking Materials Guide - Cold-Applied Plastic
Environmental Impacts
• Reported as zero solvent (VOC) emission.
• Although both resin and hardener are not usually considered hazardous, some requirements
may be stipulated for the disposal of waste
• Refer to NZRF Roadmarking Note # 11 HSNO Regulations Emergency Management
Requirements - Guideline
• In the period of 1st April 2007 to 31st March 2009, at least 9 incidents related to solvents, and
at least three related to peroxides were reported to ERMA.
Occupational Health & Safety Hazards
• Fluid Injection
• Fumes, Gases, Vapours
• Potential to Poison
• Allergic dermatitis (Sensitisation)
• Severe Irritation and Chemical Burns
• Respiratory Irritation.
Application Process – Audio-Tactile Profiled (ATP)
• Material commonly applied using a shoe which has mechanism used to produce raised
portions (blocks) at regular intervals in a line which provides motorists with audio-tactile feedback
• Products and their application are covered by patents and licencing agreements
• The PMMA and benzoyl peroxide are combined in the shoe which has an agitator to ensure
consistent mixing
• The shoe has a mechanism used to produce raised portions (blocks) at regular intervals
controlled by a computer. The block height and length is controlled by the opening size of the gates. The spacing of the resultant blocks is determined by the computer timing
• The applicator driver may or may not control the entire process
• The PMMA viscosity (affected by ambient temperature), applicator travel speed and
cleanliness of shoe are all critical to the appearance, consistency and performance of the product
• At regular intervals, and immediately after the completion of marking the shoe and associated
equipment must be removed and thoroughly cleaned using a mixture of mechanical methods and solvents.
Application Process - Structured
• Products and their application are covered by patents and licencing agreements
• Material may be applied using a rotating roller having spikes or lumps used to randomly
distribute the CAP along the marking
• Structured markings may be applied in combination with audio-tactile profile markings
• Glass beads are applied to provide retroreflectivity
• At regular intervals, and immediately after the completion of marking the shoe and associated
equipment must be removed and thoroughly cleaned using a mixture of mechanical methods and solvents.
NZRF Roadmarking Materials Guide - Cold-Applied Plastic
Application Process - Spray
• Products and their application are covered by patents and licencing agreements
• The two components are typically through a static mixer spray gun combined with a flushing
• The pavement markings are applied by an applicator which sprays material from a fixed
nozzle connected to supply system (typically a high pressure paint pump), while the applicator is driven at a uniform speed following the existing markings (or set-out spots in the case of new work)
• The applicator driver normally controls the entire process
• Tip size, fluid pressure, atomising air pressure, paint viscosity and material temperature are all
critical to the appearance, consistency and performance of the product.
Application Process – Hand Applied
• Products and their application are covered by patents and licencing agreements
• The two components are commonly combined in a clean steel container and mixed with a
slow speed drill attached to an appropriate epoxy- mixing paddle
• Appropriate filler may be added to produce a mortar for filling or for vertical surfaces
• The pot life is typically 5-10 minutes, depending on hardener quantity and ambient
• Material is applied by roller / trowel / screed and / or a combination of these, to the desired
thickness and finish. Multiple coats may be used to build desired profiles / shapes.
• Equipment is cleaned with speciality solvents – refer CAP solvents
Process Monitoring Equipment
• Application rate computers
• Applicator speedometers, calibrated over range of applicator speeds
• ATP block dimension measuring equipment – depth gauges, wedges, ruler, tape measure
• Electronic scales and paper for structured application rate determination and setting
• Electronic scales / bead buckets for glass bead application rate determination and setting
• Bead application comparison plates.
Post-Application Measuring Equipment
• Block dimension measuring equipment – depth gauges, wedges, ruler, tape measure
• Steel test plates
• Retroreflectometers
• Skid resistance testers
Test Methods
• Block dimensions, block spacing, film thickness, skid resistance and retroreflectivity tested to
NZTA P 30, NZTA P 22
• Retroreflectivity, refer also to Glass Beads
• Skid Resistance, refer also to Glass Beads and Angular Material. Note: the skid resistance of ATP material cannot be determined in current NZ ATP format with a British Pendulum Tester because the block is smaller than the sweep area of the tester.
NZRF Roadmarking Materials Guide - Cold-Applied Plastic
Quick Reference Safety Guide
• Methyl methacrylate resin may cause skin sensitisation or other allergic responses. Avoid
inhalation of vapour. Prevent contact with skin and eyes
• Dibenzoyl peroxide, avoid contact
• Associated solvents (may be a mixture of toluene and methyl ethyl ketone (MEK), avoid
• Skin Protection: Wear overalls and gloves. Use face-shield where splashing may occur. Use
• Eye Protection: Use full face-shield / goggles while mixing.
• Inhalation: Should be handled and used in well ventilated areas. Refer to CAP solvents. • If skin contact - wash immediately with soap and water – Do not use solvents or thinners.
• If eye contact - flush with water keeping eyelids apart for at least 20 minutes. Seek medical
• Remove contaminated clothing and shoes immediately. Wash clothes before reuse, discard
contaminated footwear.
Recorded Environmental Hazards
Recorded Health & Safety Incidents
• Reports of dermatitis and allergic dermatitis (Sensitisation) are common.
• Specialist sector groups interested in the safe use of methacrylates established overseas
Related National / International Standard Specifications
• Products and their application are covered by patents and licencing agreements
• APAS 0041 – Australian Paint Approval Scheme Specification 0041, Pavement Marking
• AS 4049.4 – Paints and related materials – Pavement marking materials Part 4: High
performance pavement marking systems
• AS/NZS 1580 401.8 - Methods of test for paints and related materials
• ASTM E1710 - Standard Test Method for Measurement of Retroreflective Pavement Marking
Materials with CEN-Prescribed Geometry Using a Portable Retroreflectometer
• ASTM E2176 - Standard Test Method for Measuring the Coefficient of Retroreflected
Luminance of Pavement Markings in a Standard Condition of Continuous Wetting (RL-Rain)
• ASTM E2177 - Standard Test Method for Measuring the Coefficient of Retroreflected
Luminance (RL) of Pavement Markings in a Standard Condition of Wetness
• EN 1871 – Roadmarking Materials – Physical properties
• EN 1436 - Roadmarking Material – Road marking performance for road users
• EN 1824 - Road marking materials. Road trials
• NZTA M 20 – Specification for Long-life Roadmarking Materials
NZRF Roadmarking Materials Guide - Cold-Applied Plastic
Useful References
Kadcam Enterprises – www.kadcam enterprises.com
www.basler- lacke.ch
Damar Bascolin Spray Plastic
Damar Bascoplast Cold Plastic
• Department of Labour Publication "Practical Guidelines for the Safe Use of Organic
• Health Safety & Environment Guide for Printing & Related Industries -
NZRF Roadmarking Materials Guide - Thermoplastic
12 Thermoplastic
General Description
• A material consisting of aggregate, pigment, binder, glass beads and extenders, applied in a
Composition
• Thermoplastic roadmarking material is tailored for specific application methods such as
audio-tactile profiled (ATP) markings structured markings and plain flat markings. For example, the material is specially formulated to enable raised portions to be formed cleanly and accurately. The formulation may contain fibres and /or other bonding agents.
• Virtually 100 per cent volume solids
• Aggregates, (silica sand, calcite, quartz or calcined flint) approximately 40%, combined with
pigment and extenders make up 80% of formulation
• Glass beads in the range 20% - 40%
• Pigments may be titanium dioxide, carbon black or lead chromate, approximately 10%
• Binder (either natural or synthetic resins in an oil mixture) approximately 20%
• Extender (chalk or similar to extend pigment) approximately 10%.
Note: Many fo rmulations can be softened / dissolved in aromatic solvents (i.e. Toluene or
Xylene) or chlorinated hydrocarbon solvents (i.e. Chloroform or Dichloromethane)
Physical Properties
• Rapid setting
• Top surface at a uniform height from road surface
• Edge definition affected by surface texture
• Colours: Full range including White, Yellow, & Black
• Beads can form significant percentage of structure
• Softening point not less than 100oC
• Relative density approximately 1.98kg/l.
•
Performance Properties
• Retroreflectivity: Dependent on the size and application rate of beads
• Luminance: White not less than 65, Yellow not less than 45 when tested in accordance with
• Colour: White equal to or whiter than Y35 "Off White" (NZTA M 20), Yellow between Y13
"Vivid Yellow" and Y14 "Golden Yellow" of AS 2700S (NZTA M 20) or approximately match Y14, (AS 4049.3).
• Skid Resistance: Commonly formulated to have skid resistance greater than or equal to 40
• Material can only be tested in flat format as ATP dimensions are less than sweep of, and their
shape reduces accuracy, of British Pendulum Tester results.
• Retroreflectivity / skid should not be measured immediately after application due to the
presence of process components on the material. Trafficking is advised prior to testing.
NZRF Roadmarking Materials Guide - Thermoplastic
Durability
• Regarded as a "long life" material as far as "wear" is concerned
• Recent overseas developments using high performance rosins have seen significant
improvements in service life
• The life of the material is largely dependent on the formulation, thickness applied, the pattern
of the line and the degree of trafficking.
Note: The pattern of line is selected by Road Controlling Authority for each particular purpose,
many of which are unlikely to be trafficked to any degree, e.g. audio tactile edge- line on straight
sections of highway.
Compatibility
• Can be used on most types of surfaces for longitudinal, transverse and other markings.
• Thermoplastic placed over cold-applied plastic and waterborne paints is likely to fail
• May cause a break down in the resin of waterborne paint. A solution is to apply at 190 -
200ºC to ensure thermoplastic melts through paint to bond with bitumen in road surfacing.
• Thermoplastic applied over alkyds of significant thickness, i.e. over 150 µm may fail.
Adhesion
• Can be applied over most surfaces. Concrete requires priming.
• Can be applied immediately to fresh asphalt (with better adhesion on asphalt that has had 3
month settling period). NZTA P 22 Notes recommend marking new surfaces with paint and allowing a few months settling prior to thermoplastic application.
•
Application Parameters
• Correctly formulated material must be used for profile to form cleanly and accurately
• The thermoplastic material is pre-heated to a molten state in a separate oil jacketed heating
• Pre-melters and applicator holding vessels must have continuous agitation
• Although alkyd (wood rosin) and hydrocarbon materials will fuse to one another on the road,
they are incompatible in melting vessels. Pre- melters and applicator tanks must be cleaned thoroughly between different types of thermoplastic.
• Molten thermoplastic should not be:
• Held above 200oC for more than six hours
• Heated above 230oC
• Reheated more than three times
• Markings must be protected from traffic until set. Markings being trafficked prior to setting
will be deformed. Un-beaded markings coming into contact with tyres while still warm will draw carbon black and road grime from tyres.
• Road and air temperatures should be greater than 10oC and rising. Poor bond will develop if
road temperature falls below 5oC
• Road surface needs to be clean and dry. Moisture tests need to be conducted prior to
• Substrate prepared by hand / mechanical brooming or use of high velocity / high pressure air
blowing to remove loose paint, dust and dirt
• Road surface needs to be smooth and free of objects / shape changes that may affect the travel
of the screed box.
NZRF Roadmarking Materials Guide - Thermoplastic
Manufacturing Process
• For powder products the components are mixed using a ribbon or similar blender to form the
finished product.
• Following QC testing the powder is bagged and labelled.
Testing of Physical Properties
• Thermoplastic may be tested to NZTA M 20, AS 4049.2, AS 4049.4 or EN 1871.
Handling, storage & packaging
• Generally supplied as a powder or powder/oil suspension
• 25 kg plastic and paper bags. Plastic bags can be formulated such they can be added to the
• Store powder mix protected from rain and moisture. Presence of moisture can cause foaming,
spitting and expansion on heating
• Protect from excessive heat or contamination from fuels, oils or greases
• Classified as Non Hazardous unless heated
• Flash Point exceeds 230oC
• Extinguishing Media include Foam, Carbon Dioxide, Dry Chemical
• When Heated Typical Classification – refer to product specific data sheets
• Proper Shipping Name: Elevated Temperature Liquid
• Packing Group: III
• HazChem Code: 2W
Environmental Impacts
• Thermoplastic is largely inert. Powder and waste material can usually be disposed of in
accordance with local disposal regulations for non-hazardous materials.
• In the period of 1st April 2007 to 31st March 2009, at least 1 incident related to heat transfer
oil and 76 related to LPG were reported to ERMA.
• 1) Heat transfer oils used in pre-melters and applicators is classified as 3Z.
• 2) Heat transfer oils may present particular hazards, refer to related Safety Data Sheets
before disposal.
Occupational Health & Safety Hazards
Powder Form
• Dusts
• Eye irritation. Molten Form
NZRF Roadmarking Materials Guide - Thermoplastic
Application Process – Audio-tactile profiled (ATP)
• The thermoplastic material is pre-heated to a molten state in a separate oil jacketed heating
• Pre-melters and applicator holding vessels must have continuous agitation
• Machine screeded thermoplastic pavement markings are applied by an applicator which drags
a frame (screed box) having a fixed aperture on the lower trailing edge, connected to the molten thermoplastic supply system (typically a feed-screw in a cylinder), following the existing markings (or set-out spots in the case of new work)
• At predetermined intervals a secondary gate mechanism is opened increasing aperture height
to form a portion of line with an increased height. The frequency and duration of the gate opening and shutting controls the pattern of the line
• The width of the aperture controls the line width. The material is normally presented to the
screed box aperture through the use of a feed-screw or similar device
• The applicator driver normally has an assistant to monitor conditions and control the process
• The material temperature and the road surface conditions (both texture depth and general
condition) are the critical factors to the appearance, consistency and performance of the product
• Machine screed thermoplastic application plant and pre-melters require verification /
calibration to ensure application requirements are known. Refer to NZTA T 12
• Glass beads are simultaneously applied to the surface of the molten line if immediate
retroreflectivity is specified
• Angular material may be applied in conjunction with beads if required to achieve particular
skid resistance values. The addition of angular material with glass beads must be well controlled to ensure that retroreflectivity is not compromised
• This process is typically slower than extrusion methods.
Application Process - Extrusion
• The thermoplastic material is pre-heated to a molten state in a separate oil jacketed heating
• Pre-melters and applicator holding vessels must have continuous agitation
• Extruded thermoplastic pavement markings are applied by an applicator which extrudes a
ribbon of molten thermoplastic from a fixed width slot, connected to the molten thermoplastic supply system (typically a feed-screw in a cylinder), while the applicator is driven at a uniform speed following the existing markings (or set-out spots in the case of new work)
• The aperture height and the road speed control the thickness achieved on the road. The width
of the line is similarly controlled / affected by aperture width and road speed
• The applicator driver normally has an assistant who monitors conditions and controls the
• Applicator speed, feed rate (feed-screw rpm), height of slot from road surface and material
temperature are all critical to the appearance, consistency and performance of the product
• Extruded thermoplastic application plant and pre-melters require verification / calibration to
ensure application requirements are known. Refer to NZTA T 12
• Glass beads are simultaneously applied to the surface of the molten line if immediate
retroreflectivity is specified
• Angular material may be applied in conjunction with beads if required to achieve particular
skid resistance values
• This process is typically faster than screed methods.
NZRF Roadmarking Materials Guide - Thermoplastic
Application Process - Structured
• The thermoplastic material is pre-heated to a molten state in a separate oil jacketed heating
• Pre-melters and applicator holding vessels must have continuous agitation
• Products and their application are covered by patents and licencing agreements
• Material may be applied using a rotating drum used to distribute the thermoplastic along the
• Glass beads are applied to provide retroreflectivity
Application Process - Embossed
• The thermoplastic material is pre-heated to a molten state in a separate oil jacketed heating
• Pre-melters and applicator holding vessels must have continuous agitation
• Extruded thermoplastic pavement markings are applied by an applicator which extrudes a
ribbon of molten thermoplastic from a fixed width slot, connected to the molten thermoplastic supply system (typically a feed-screw in a cylinder), while the applicator is driven at a uniform speed following the existing markings (or set-out spots in the case of new work)
• Machine screeded thermoplastic pavement markings are applied by an applicator which drags
a frame (screed box) having a fixed aperture on the lower trailing edge, connected to the molten thermoplastic supply system (typically a feed-screw in a cylinder), following the existing markings (or set-out spots in the case of new work)
• The applicator driver normally drives the applicator while an assistant monitors conditions
and controls the process
• The material temperature and the road surface conditions (both texture depth and general
condition) are the critical factors to the appearance, consistency and performance of the product
• Machine screed and extrusion thermoplastic application plant and pre-melters require
verification / calibration to ensure application requirements are known. Refer to NZTA T 12
• Glass beads are simultaneously applied to the surface of the molten line to act as a release
agent for the embossing tool
• This process is typically slower than extrusion methods.
Application Process – Machine Screed
• The thermoplastic material is pre-heated to a molten state in a separate oil jacketed heating
• Pre-melters and applicator holding vessels must have continuous agitation
• Machine screeded thermoplastic pavement markings are applied by an applicator which drags
a frame (screed box) having a fixed aperture on the lower trailing edge, connected to the molten thermoplastic supply system (typically a feed-screw in a cylinder), following the existing markings (or set-out spots in the case of new work)
• The applicator driver normally drives the applicator while an assistant monitors conditions
and controls the process
• The material temperature and the road surface conditions (both texture depth and general
condition) are the critical factors to the appearance, consistency and performance of the product
• Machine screed thermoplastic application plant and pre-melters require verification /
calibration to ensure application requirements are known. Refer to NZTA T 12
NZRF Roadmarking Materials Guide - Thermoplastic
• Glass beads are simultaneously applied to the surface of the molten line if immediate
retroreflectivity is specified. Consistency of beading of machine screeded lines is more difficult to achieve than extrusion
• Angular material may be applied in conjunction with beads if required to achieve particular
skid resistance values
• This process is typically slower than extrusion methods
• The quantity of material used and speed of application is highly dependent on the texture
depth and condition of the pavement.
Application Process – Machine Spray
• The thermoplastic material is pre-heated to a molten state in a separate oil jacketed heating
• Pre-melters and applicator holding tanks must have continuous agitation
• Sprayed thermoplastic pavement markings are applied by an applicator which sprays molten
thermoplastic through a nozzle, connected to the molten thermoplastic supply system (typically pressurised), while the applicator is driven at a uniform speed following the existing markings (or set-out spots in the case of new work)
• The applicator driver normally drives the applicator while an assistant monitors conditions
and controls the process
• Applicator speed, nozzle pressure, supply pressure, height of nozzle from road surface and
material temperature are all critical to the appearance, consistency and performance of the product
• Sprayed thermoplastic application plant and pre-melters require verification / calibration to
ensure application requirements are known. Refer to TNZ T 12
• Glass beads are simultaneously applied to the surface of the molten line if immediate
retroreflectivity is specified
• Angular material may be applied in conjunction with beads if required to achieve particular
skid resistance values
• This process is typically faster than screed methods
• Note: As the heating vessel is pressure vessel it is subject to the certification requirements of
the Pressure Equipment, Cranes and Passenger Ropeways Regulations 1999.
Application Process - Handscreed
• The thermoplastic material is pre-heated to a molten state in a separate oil jacketed heating
• Pre-melters and applicator holding tanks must have continuous agitation.
• Molten thermoplastic is poured by ladle into a frame (screed box) having a fixed aperture on
the lower trailing edge, which is dragged along the existing markings (or set-out spots in the case of new work). Sufficient additional molten material is added to the box to complete the markings
• The material temperature and the road surface conditions (both texture depth and general
condition) are the critical factors to the appearance, consistency and performance of the product
• Due to the manual nature of the process the action of simultaneously applying beads and
angular material to the surface of the molten line is difficult. The more sophisticated methods using wheeled carts can provide a degree of consistency of bead application
• This process is typically slower than machine extrusion methods, however less equipment is
NZRF Roadmarking Materials Guide - Thermoplastic
Process Monitoring Equipment
• Portable environmental measuring devices for temperature
• Thermoplastic application rate computers
• Electronic scales for glass bead application rate
• Speedometers
• Thermoplastic and heating temperature gauges
• Film thickness gauges
• Fixed form height gauges
• Bead application comparison plates
• Surface texture measuring kit (sand circle equipment).
Post-Application Measuring Equipment
• Dry Film Thickness measured using non-destructive eddy current device such as the
Elcometer. Device must be able to measure the full depth of the profile
• Mechanical thickness measuring devices such as external micrometers and snap gauges
• Steel test plates
• Retroreflectometers
• Skid resistance testers
Test Methods
• Block dimensions, block spacing, film thickness, skid resistance and retroreflectivity tested to
NZTA P 30, NZTA P 22
• Retroreflectivity refer to Glass Beads.
Quick Reference Safety Guide
• Understand and carry instructions regarding treatment of burns
• Carry water specifically for the immediate treatment of burns
• Wear full length overalls and safety boots or shoes at all times
• Wear gloves and safety glasses / face shield when handling molten thermoplastic
• Ensure that heating vessels are free of excess water before commencing heating process
• Never operate heating systems while vehicle is moving
• Provide adequate ventilation during loading of pre-melters. • Skin Protection: Wear overalls and gloves. Use face-shield where splashing may occur.
Overalls must be safe at high temperature (e.g. cotton) safety boots must be covered to prevent entry of hot thermoplastic, gloves or gauntlets similarly need to be worn inside sleeves to prevent entry of hot thermoplastic.
• Eye Protection: Use full face-shield while transferring molten material and checking holding
• Inhalation: Should be handled and used in well ventilated areas • If burnt, Do not attempt to remove any thermoplastic, cool the affected area with water, keep
on cooling until medical aid is available, handle carefully, avoid disturbing the burn, remove belts and other constrictions, don't remove clothing, don't attempt to clean area, don't apply lotions or ointments, cover burns free from thermoplastic with clean lint free material, keep patient warm without touching bur ns with blanket. Seek medical help, ensure that they read Burns Card and understand treatment. Stay with patient. Treat patient for shock. Only give small amounts of liquids at frequent intervals
NZRF Roadmarking Materials Guide - Thermoplastic
Notes:
1) There are gel-based products that provide safe and reliable burn cooling effects 2
Many formulations can be softened / dissolved in aromatic solvents (i.e. Toluene or Xylene), Methyl Ethyl Ketone (MEK) or chlorinated hydrocarbon solvents (i.e. Chloroform or Dichloromethane)
• If eye burn, flush with water for at least 20 minutes. Don't remove thermoplastic, seek
medical help, ensure that they read Burns Card and understand treatment. Stay with patient. Treat patient for shock. Only give small amounts of liquids at frequent intervals.
• If dust or fumes inhaled, provide fresh air, rest and keep warm. If breathing shallow, give
oxygen. Contact a Doctor or Poisons Information Centre.
• If eye contact with powder, wash with running water for at least 15 minutes. Seek medical
Recorded Environmental Hazards
Recorded Health & Safety Incidents
Related National / International Standard Specifications
• APAS 0041 – Australian Paint Approval Scheme Specification 0041, Pavement Marking
• AS 4049.2 - Paints and related materials - Pavement marking materials - Thermoplastic
pavement marking materials - For use with surface applied glass beads
• AS 4049.4 – Paints and related materials – Pavement marking materials Part 4: High
performance pavement marking systems
• AS/NZS 1580 401.8 - Methods of test for paints and related materials
• ASTM E1710 - Standard Test Method for Measurement of Retroreflective Pavement Marking
Materials with CEN-Prescribed Geometry Using a Portable Retroreflectometer
• ASTM E2176 - Standard Test Method for Measuring the Coefficient of Retroreflected
Luminance of Pavement Markings in a Standard Condition of Continuous Wetting (RL-Rain)
• ASTM E2177 - Standard Test Method for Measuring the Coefficient of Retroreflected
Luminance (RL) of Pavement Markings in a Standard Condition of Wetness
• EN 1871 – Roadmarking Materials – Physical properties
• EN 1436 - Roadmarking Material – Road marking performance for road users
• EN 1824 - Road marking materials. Road trials
• NZTA M 7 - Specification for Roadmarking Paints
• NZTA M 20 – Specification for Long-life Roadmarking Materials
Useful References
• Safety Data Sheets
Kestral Thermoplastics
• Field Guide on Thermoplastic Application – Swarco Industries
• Roading New Zealand Code of Practice for the safe handling of bituminous materials used on
• Gel-based Burn Treatment Systems
Jackson Allison Medical & Surgical Ltd
NZRF Roadmarking Materials Guide - Pre-formed Thermoplastic
13 Pre-Formed Thermoplastic
General Description
• A material consisting of aggregate, pigment, binder, glass beads and extenders, supplied pre-
formed. The material can be supplied in a variety of line widths and shapes
• The pre-formed material is laid on the road surface and heated until it binds to the road
• Pre-form allows the installation of small quantities of thermoplastic and letters and shapes
without overlaps.
•
Composition
• Virtually 100 per cent volume solids
• Aggregates, (silica sand, calcite, quartz or calcined flint) approximately 40%, combined with
pigment, beads and extenders make up 80% of formulation
• Glass beads in the range of 20 to 40%, NZTA M 20 requires a minimum of 20% by mass
• Pigments may be titanium dioxide, carbon black or lead chromate, approximately 5 to 10%
• Binder (either natural or synthetic resins in an oil mixture) approximately 20%
• Extender (chalk or similar to extend pigment) approximately 10%.
Note: Many formulations can be softened / dissolved in aromatic solvents (i.e. Toluene or
Xylene) or chlorinated hydrocarbon solvents (i.e. Chloroform or Dichloromethane)
Physical Properties
• Rapid setting
• Colours: Full range including White, Yellow, & Black
• Beads can form significant percentage of structure
• Softening point not less than 75oC when tested in accordance with NZTA M 20.
• Relative density approximately 1.98 kg/l
Performance Properties
• Retroreflectivity: No values available for unbeaded thermoplastic
• Luminance: White not less than 75, Yellow not less than 45 when tested in accordance with
• Colour: White equal to or whiter than Y35 "Off White" (NZTA M 20), Yellow between Y13
"Vivid Yellow" and Y14 "Golden Yellow" of AS 2700S (NZTA M 20) or approximately match Y14, (AS 4049.3).
• Skid Resistance: Commonly formulated to have skid resistance equal to or greater than
40 BPN. NZTA M 20 requires a value of 45 to 65BPN
• Note: The skid resistance and retroreflectivity of a marking material is not a fixed property for
any given formulation. It may vary considerably according to the temperature at which it is laid and will also vary throughout its life according to conditions such as traffic and weather.
•
Durability
• Regarded as a "long life" material as far as "wear" is concerned
• The life of the material is largely dependent on the thickness applied
• NZTA P 22 specifies a thickness of 2.0 to 2.5mm on asphalt and 2.0 to 3.0mm on chip-seal Note: thickness' above 4 to 4.5 mm may cause difficulties for particular road users.
NZRF Roadmarking Materials Guide - Pre-formed Thermoplastic
Compatibility
• Can be used on most types of surfaces and for longitudinal, transverse and other markings
• May cause a break down in the resin of waterborne paint
• Thermoplastic placed over cold-applied plastic and waterborne paints is likely to fail
• Thermoplastic applied over alkyds of significant thickness, i.e. over 150 um may fail.
•
Adhesion
• Can be applied over most surfaces. Concrete requires priming
• Can be applied immediately to fresh asphalt (with better adhesion on asphalt that has had 3
month settling period. NZTA P 12 Notes recommends marking new surfaces with paint and allowing a few months settling prior to thermoplastic application.
•
Application Parameters
• Markings must be protected from traffic until set. Markings coming into contact with tyres
while still warm will draw carbon black and road grime from tyres if un-beaded
• Road and air temperatures should be greater than 10oC and rising. Poor bond will develop if
road temperature falls below 5oC
• Road surface needs to be clean and dry. Moisture tests need to be conducted prior to
• Substrate prepared by hand / mechanical brooming or use of high velocity / high pressure air
blowing to remove loose paint, dust and dirt.
Manufacturing Process
The pre- formed product is produced by either extrusion or screed processes using standard
thermoplastic marking materials. Additives may be used to improve sheet strength. Shapes are
commonly cut from sheet product. The material is either rolled up or supplied in sheet form.
Testing of Physical Properties
• Thermoplastic may be tested to NZTA M 20, AS 4049.2, AS 4049.4 or EN 1871,
Handling, storage & packaging
• Generally supplied in roll or sheet form. Protect from shock or impact damage
• Store protected from rain and moisture. Presence of moisture can cause spitting and
deformation on heating
• Protect from excessive heat or contamination from fuels, oils or greases
• Do not stack other material directly on sheets as they deform under pressure / time
• Classified as Non Hazardous
• Flash Point exceeds 230oC
• Extinguishing Media include Foam, Carbon Dioxide, Dry Chemical.
Environmental Impacts
• Thermoplastic is largely inert, waste material can usually be disposed of in accordance with
local disposal regulations for non- hazardous materials
• In the period of 1st April 2007 to 31st March 2009, at least 76 incidents related to LPG were
reported to ERMA.
NZRF Roadmarking Materials Guide - Pre-formed Thermoplastic
Occupational Health & Safety Hazards
Molten Form
• Burns
Application Process
• The pre-formed thermoplastic material is laid on the road surface in the desired location
• The material is heated (typically using gas wand) until it softens sufficiently to adhere to the
road surface. Care needs to be taken to ensure that material is heated sufficiently to bond without overheating or charring of the surface.
• Pre-formed thermoplastic is ideal for small works where urgent long life marking is required
or where there is no other work required. Eliminating the requirement for large thermoplastic equipment on site.
• Due to manual style of application it is difficult to consistently apply glass beads / angular
material to the top surface. Some manufacturers supply pre- form material with surface treatments.
•
Process Monitoring Equipment
• Portable environmental measuring devices for temperature
Post-Application Measuring Equipment
• Dry Film Thickness measured using non-destructive eddy current device such as the
• Steel test plates
• Retroreflectometers
• Skid resistance testers.
Test Methods
• Dry Film thickness, Skid Resistance and Retroreflectivity tested to, NZTA P 20, or
• Retroreflectivity refer to Glass Beads
Quick Reference Safety Guide
• Understand and carry instructions regarding treatment of burns
• Carry water specifically for the immediate treatment of burns
• Wear full length overalls and safety boots or shoes at all times
• Skin Protection: Wear overalls and gloves. Overalls must be safe at high temperature (i.e.
• If burnt, Do not attempt to remove any thermoplastic, cool the affected area with water, keep
on cooling until medical aid is available, handle carefully, avoid disturbing the burn, remove belts and other constrictions, don't remove clothing, don't attempt to clean area, don't apply lotions or ointments, cover burns free from thermoplastic with clean lint free material, keep patient warm without touching burns with blanket. Seek medical help, ensure that they read Burns Card and understand treatment. Stay with patient. Treat patient for shock. Only give small amounts of liquids at frequent intervals
NZRF Roadmarking Materials Guide - Pre-formed Thermoplastic
Notes:
1) There are gel-based products that provide safe and reliable burn cooling effects 2
Many formulations can be softened / dissolved in aromatic solvents (i.e. Toluene or Xylene), Methyl Ethyl Ketone (MEK) or chlorinated hydrocarbon solvents (i.e. Chloroform or Dichloromethane)
• If eye burn, flush with water for at least 20 minutes. Don't remove thermoplastic, seek
medical help, ensure that they read Burns Card and understand treatment. Stay with patient. Treat patient for shock. Only give small amounts of liquids at frequent intervals.
• If dust or fumes inhaled, provide fresh air, rest and keep warm. If breathing shallow, give
oxygen. Contact a Doctor or Poisons Information Centre.
• If eye contact with powder, wash with running water for at least 15 minutes. Seek medical
Recorded Environmental Hazards
Recorded Health & Safety Incidents
Related National / International Standard Specifications
• AS 4049.2 - Paints and related materials - Pavement marking materials - Thermoplastic
pavement marking materials - For use with surface applied glass beads
• AS 4049.4 – Paints and related materials – Pavement marking materials Part 4: High
performance pavement marking systems
• AS/NZS 1580 401.8 - Methods of test for paints and related materials
• ASTM E1710 - Standard Test Method for Measurement of Retroreflective Pavement Marking
Materials with CEN-Prescribed Geometry Using a Portable Retroreflectometer
• ASTM E2176 - Standard Test Method for Measuring the Coefficient of Retroreflected
Luminance of Pavement Markings in a Standard Condition of Continuous Wetting (RL-Rain)
• ASTM E2177 - Standard Test Method for Measuring the Coefficient of Retroreflected
Luminance (RL) of Pavement Markings in a Standard Condition of Wetness
• EN 1790 Roadmarking Materials – Preformed roadmarkings
• EN 1871 – Roadmarking Materials – Physical properties
• EN 1436 - Roadmarking Material – Road marking performance for road users
• EN 1824 - Road marking materials. Road trials
• NZTA M 7 - Specification for Roadmarking Paints
• NZTA M 20 – Specification for Long-life Roadmarking Materials
Useful References
• Safety Data Sheets
Kestral Thermoplastics
• Field Guide on Thermoplastic Application – Swarco Industries
• Roading New Zealand Code of Practice for the safe handling of bituminous materials used on
• Gel-based Burn Treatment Systems
Jackson Allison Medical & Surgical Ltd
NZRF Roadmarking Materials Guide - Permanent Tapes
14 Permanent Tapes
General Description
• A pre-formed adhesive backed product, generally in roll or pre-cut form relying on pressure
on the adhesive to create a bond with the pavement surface.
•
Composition
• Covered by Licence Agreements
• Virtually 100 per cent volume solids
• A variety of materials, which may include but be not limited to polymeric materials, pliant
polymers, thermoplastic resins, pigments and beads
• Glass beads and / or reflective elements are applied as coating to top surface to provide
immediate retroreflectivity
• Pigments may be titanium dioxide, carbon black or, approximately 10%
Physical Properties
• Low Gloss
• Colours: White, Yellow, (may be bordered with black to raise contrast)
• Plain black versions exist designed for the permanent masking of redundant pavement
•
Performance Properties
• Retroreflectivity ranges from 175 mcd, with high performance embossed tapes achieving
retroreflectivity values in excess of 500 mcd
• Capable of providing reflectivity under conditions of wetness or rain with the use of high
refractive index beads and / or elements
• Colour: White equal to or whiter than Y35 "Off White" (NZTA M 20), Yellow between Y13
"Vivid Yellow" and Y14 "Golden Yellow" of AS 2700S (NZTA M 20).
• Commonly formulated to have initial skid resistance of 45 BPN
• Note: Tapes are available in a wide variety of styles and patterns and should be selected on
the basis of the requirements.
•
Durability
• Regarded as a "long life" material.
Compatibility
• Can be used on most types of surfaces and for longitudinal, transverse and other markings
• Caution is needed when applying thermoplastic over permanent tape as the heat could cause
the tape to curl up at the edges
• Caution is required when applying over old markings in poor condition.
•
Adhesion
• Can be applied over most surfaces. Traditional tapes require priming when applying to
• Can be applied immediately to fresh asphalt, often rolled directly into the warm asphalt
• Damage will be caused by heavy trucks, excessive encroachment on high ADT roadways,
narrow lane width, unpaved shoulders, snow removal and ice control techniques.
NZRF Roadmarking Materials Guide - Permanent Tapes
Application Parameters
• Road surface needs to be clean and dry. Moisture tests need to be conducted prior to
• Substrate prepared by hand / mechanical brooming or use of high velocity / high pressure air
blowing to remove loose paint, dust and dirt
• Roller pressure needs to be sufficient to ensure bonding over entire width of tape.
•
Manufacturing Process
Testing of Physical Properties
• NZTA M 20 – Specification for Long Life Markings
• ASTM D4505 - Standard Specification for Preformed Retroreflective Pavement Marking
Tape for Extended Service Life.
Handling, storage & packaging
• Generally supplied in roll form. Protect from shock or impact damage
• Use with 12 months of purchase
• Store protected from rain and moisture. Presence of moisture can cause poor bonding on
• Protect from excessive heat or contamination from fuels, oils or greases
• Extinguishing Media include Foam, Carbon Dioxide, Dry Chemical
• Typically classified as non-hazardous.
Environmental Impacts
• Permanent tapes are largely inert, waste material can usually be disposed of in accordance
with local disposal regulations for non-hazardous materials.
Occupational Health & Safety Hazards
• May give off fumes on application of heat during removal.
Application Process
• Substrate prepared by hand / mechanical brooming or use of high velocity / high pressure air
blowing to remove loose paint, dust and dirt
• Road surface needs to be clean and dry. Moisture tests need to be conducted prior to
• The pre-formed thermoplastic material is laid on the road surface in the desired location
• Tape is rolled directly onto surface using a roller appropriate to the substrate.
Process Monitoring Equipment
None
Post-Application Measuring Equipment
• Tape adhesion / pull-off test kit.
Test Methods
• Retroreflectivity refer to Glass Beads
• Skid Resistance refer also to Glass Beads and Angular Material
NZRF Roadmarking Materials Guide - Permanent Tapes
Quick Reference Safety Guide
• Permanent grades are difficult to remove often-requiring heat, which may give off noxious
fumes. Use organic vapour respirator conforming to AS 1716
Recorded Environmental Hazards
Recorded Health & Safety Incidents
Related National / International Standard Specifications
• AS 4049.2 - Paints and related materials - Pavement marking materials - Thermoplastic
pavement marking materials - For use with surface applied glass beads
• AS 4049.4 – Paints and related materials – Pavement marking materials Part 4: High
performance pavement marking systems
• AS/NZS 1580 401.8 - Methods of test for paints and related materials
• ASTM E303 - Standard Test Method for Measuring Surface Frictional Properties Using the
British Pendulum Tester
• ASTM E1710 - Standard Test Method for Measurement of Retroreflective Pavement Marking
Materials with CEN-Prescribed Geometry Using a Portable Retroreflectometer
• ASTM E2176 - Standard Test Method for Measuring the Coefficient of Retroreflected
Luminance of Pavement Markings in a Standard Condition of Continuous Wetting (RL-Rain)
• ASTM E2177 - Standard Test Method for Measuring the Coefficient of Retroreflected
Luminance (RL) of Pavement Markings in a Standard Condition of Wetness
• EN 1790 Roadmarking Materials – Preformed roadmarkings
• EN 1871 – Roadmarking Materials – Physical properties
• EN 1436 - Roadmarking Material – Road marking performance for road users
• EN 1824 - Road marking materials. Road trials
• NZTA M 7 - Specification for Roadmarking Paints
• NZTA M 20 – Specification for Long-life Roadmarking Materials
Useful References
• Safety Data Sheets
• 3M Information Folders IF 380WRES & IF 5.7
NZRF Roadmarking Materials Guide – Temporary Tapes
15 Temporary Tapes
General Description
• A pre-formed adhesive backed product, generally in roll or pre-cut form relying on pressure
on the adhesive to create a bond with the pavement surface, where the adhesive is specifically designed to enable removal after a specified amount of time or traffic passes.
•
Composition
• Covered by Licence Agreements
• Virtually 100 per cent volume solids
• A variety of materials, which may include but be not limited to polymeric materials, pliant
polymers, pigments and beads
• Reflective Beads, frequently long life ceramic beads are applied as coating to top surface to
provide immediate and durable retroreflectivity
• Pigments may be titanium dioxide, carbon black or lead chromate, approximately 10%, but a
number are lead chromate free
• A non reflective black version is available to enable lines to be temporarily covered.
Physical Properties
• Low Gloss
• Typically have an embossed or raised pattern
• Colours: White, Yellow
• Plain black for temporarily covering lines.
•
Performance Properties
• Retroreflectivity ranges from 175 to 500 mcd plus.
• Have the capability to provide reflectivity under conditions of wetness or rain with the use of
high refractive index beads and / or elements
• Commonly formulated to have initial skid resistance of 45 BPN
• Applied tape is immediately open for vehicle use
• The blackout version has no reflectivity
• Note: These tapes are specifically designed to be removed but use beyond their specified
limits can increase difficulty of removal.
•
Durability
• Strictly for short periods determined by time or traffic counts.
Compatibility
• Can be used on most types of surfaces for longitudinal and some transverse markings
• Caution is required when applying over old markings in poor condition
• Caution where placement has heavy vehicles negotiating tight bends.
NZRF Roadmarking Materials Guide – Temporary Tapes
•
Adhesion
• Can be applied over most surfaces
• Caution should be taken in using the tape for transverse lines
• Can be applied immediately to fresh asphalt
• Damage will be caused by heavy trucks, excessive encroachment on high ADT roadways,
narrow lane width, unpaved shoulders, snow removal and ice control techniques.
•
Application Parameters
• Road surface needs to be clean and dry. Moisture tests need to be conducted prior to
• Substrate prepared by brooming to remove loose paint, dust and dirt
• Roller pressure needs to be sufficient to ensure bonding over entire width of tape.
•
Manufacturing Process
Testing of Physical Propert ies
• No New Zealand or AS/NZS specification
• ASTM D4592 - Standard Specification for Preformed Retroreflective Pavement Marking
Tape for Limited Service Life.
Handling, storage & packaging
• Generally supplied in roll form. Protect from shock or impact damage
• Use within 12 months of purchase
• Store protected from rain and moisture. Presence of moisture can cause poor bonding on
• Protect from excessive heat or contamination from fuels, oils or greases
• Extinguishing Media include Foam, Carbon Dioxide, Dry Chemical.
Environmental Impacts
• Permanent tapes are largely inert, waste material can usually be disposed of in accordance
with local disposal regulations for non-hazardous materials.
Occupational Health & Safety Hazards
Application Process
• Substrate prepared by brooming to remove loose paint, dust and dirt
• Road surface needs to be clean and dry. Moisture tests need to be conducted prior to
• Tape is rolled directly onto surface using a roller appropriate to the substrate.
Process Monitoring Equipment
• Adhesion to the road surface.
Post-Application Measuring Equipment
• Tape adhesion / pull-off test kit.
NZRF Roadmarking Materials Guide – Temporary Tapes
Test Methods
• Retroreflectivity, refer to Reflective Beads and Retroreflectometer
• Skid Resistance, refer also to Reflective Beads and Angular Material.
Quick Reference Safety Guide
Recorded Environmental Hazards
Recorded Health & Safety Incidents
Related National / International Standard Specifications
• AS/NZS 1580 401.8 - Methods of test for paints and related materials
• ASTM E303 - Standard Test Method for Measuring Surface Frictional Properties Using the
British Pendulum Tester
• ASTM E1710 - Standard Test Method for Measurement of Retroreflective Pavement Marking
Materials with CEN-Prescribed Geometry Using a Portable Retroreflectometer
• ASTM D4592 - Standard Specification for Preformed Retroreflective Pavement Marking
Tape for Limited Service Life.
• EN 1790 Roadmarking Materials – Preformed roadmarkings
• EN 1871 – Roadmarking Materials – Physical properties
• EN 1436 - Roadmarking Material – Road marking performance for road users
• EN 1824 - Road marking materials. Road trials
Useful References
• Safety Data Sheets
• 3M Information Folders IF 3.2
NZRF Roadmarking Materials Guide - Permanent Non Retroreflective Raised Pavement
Markers – Type B AS/NZS 1906.3
16 Permanent Non Retroreflective Raised Pavement Markers –
Type B AS/NZS 1906.3
General Description
• A small object adhered to the pavement surface aimed at providing audio-tactile feedback to
•
Composition
• Commonly ceramic, metallic or high impact plastic.
Physical Properties
• Self-cleaning
• High impact strength
• Heat and UV resistant
• Colours: White & yellow.
•
Performance Properties
• Retroreflectivity: None
•
Durability
• Regarded as "semi-long life"
• "Life" dependent on a range of factors that include but are not limited to UV exposure,
substrate, method of fixture, traffic type and volume etc.
Compatibility
• Can be used on most types of surfaces, bitumen, asphaltic concrete and Portland cement.
Refer to RPM Adhesives.
Adhesion
• Can be used on most types of surfaces, bitumen, asphaltic concrete and Portland cement.
Refer to RPM Adhesives.
Application Parameters
• RPM's must be clean and dry
• Refer to RPM Adhesives for application details
• Care must be taken to ensure that adhesive is not left on the body
• Visual observation to confirm that RPM type, and location is correct
• RPM's must not be exposed to traffic until adhesive is set or dry.
Manufacturing Process
Testing of Physical Properties
• Raised Pavement Markers may be tested to NZTA M 12 / AS/NZS 1906.3.
NZRF Roadmarking Materials Guide - Permanent Non Retroreflective Raised Pavement
Markers – Type B AS/NZS 1906.3
Handling, storage & packaging
• Store in cool dry place with packaging protected from rain and moisture
• Protect from excessive heat or contamination from fuels, oils or greases
• Classified as Non Hazardous.
Environmental Impacts
• Loose RPM may cause significant damage /litter.
Occupational Health & Safety Hazards
• Installation / replacement of RPM has significant hazards, not least road traffic. Also refer to
Application Process
• RPM's must be clean and dry
• Refer to RPM Adhesives for application details.
•
Process Monitoring Equipment
• Refer to RPM Adhesives.
Post-Application Measuring Equipment
Test Methods
• Installation and maintenance requirements examined in accordance with NZTA P 14.
Quick Reference Safety Guide
Recorded Environmental Hazards
Recorded Health & Safety Incidents
Related National / International Standard Specifications
• NZTA P 14 Installation of Raised Pavement Markers
• NZTA M 12 Raised Pavement Markers
• NZTA M 12: Notes for Raised Pavement Markers – Contains NZTA Approvals for use
• AS 1906.3 Retroreflective materials and devices for road traffic control purposes -
Retroreflective Markers Type B.
Useful References
NZRF Roadmarking Materials Guide - Permanent Retroreflective Raised Pavement
Markers - Type A AS/NZS 1906.3
17 Permanent Retroreflective Raised Pavement Markers – Type A
AS/NZS 1906.3
General Description
• A small plastic object containing a retroreflective element adhered to the pavement surface
aimed at providing both night-time visibility and audio-tactile feedback to motorists
• Variety of retroreflective lens protection including glass and ceramic coating
• Some have pre applied pressure sensitive adhesive (PSA).
•
Composition
• Commonly made of high impact plastic
• Variety of retroreflective elements used, including large glass spheres.
Physical Properties
• Self-cleaning
• High impact strength
• Colours: Full range including blue.
• Low water absorption
• Heat and UV resistant.
Performance Properties
• Retroreflectivity: When measured in accordance with AS/NZS 1906.3 values in the range of
1.5 to 5.0 mcd/lux for an entrance angle of 0o and observation angle of 0.2o. AS/NZS 1906.3 provides table of required values
• Glass-faced RRPM's provide significant improvements in retroreflectivity over longer service
periods than acrylic- faced RRPM's.
Durability
• Regarded as "semi-long life"
• "Life" dependent on a range of factors, which include but are not limited to UV exposure,
substrate, method of fixture, reflective lens durability, traffic type and volume etc.
• Glass faced RRPM's and Ceramic coated RRPM's reportedly have longer performance life
than acrylic faced RRPM's when adhered to smooth surfaces
• Type of adhesive / substrate may have significant effect on life.
Compatibility
• Can be used on most types of surfaces, bitumen, asphaltic concrete and Portland cement.
Refer to RPM Adhesives.
Adhesion
• Can be used on most types of surfaces, bitumen, asphaltic concrete and Portland cement.
Refer to RPM Adhesives.
NZRF Roadmarking Materials Guide - Permanent Retroreflective Raised Pavement
Markers - Type A AS/NZS 1906.3
Application Parameters
• RRPM's must be clean and dry
• Road surface must be clean, dry and free from loose chips / material
• Refer to RPM Adhesives for application details
• Care must be taken to ensure that adhesive is not left on the body or lens of the RRPM, and
that the bead of adhesive round the RRPM does not obscure the reflective element
• The entire base of the RRPM must be supported by adhesive to ensure that it does not
fracture under load
• The adhesive should form a circle which just touches all four corners of RPM without
submerging RRPM in glue
• Visual observation to confirm that RRPM type, alignment and orientation is correct
• RRPM's must not be exposed to traffic until adhesive is set or dry.
Manufacturing Process
• Typical manufacture has a plastic shell filled with resin. Some may be effectively one piece
for added strength.
Testing of Physical Properties
• Retroreflective Raised Pavement Markers may be tested to NZTA M 12 and AS/NZS 1906.3.
Handling, storage & packaging
• Store in cool dry place with packaging protected from rain and moisture.
• Protect from excessive heat or contamination from fuels, oils or greases.
• Classified as Non Hazardous.
Environmental Impacts
• Loose RPM may cause significant damage /litter
Occupational Health & Safety Hazards
• Installation / replacement of RPM has significant hazards, not least road traffic. Also refer to
Application Process
• RRPM's must be clean and dry
• Glass-faced RRPM's should not be applied to coarse surfaces which are subject to chip /
• Refer to RPM Adhesives for application details.
•
Process Monitoring Equipment
• Refer to RPM Adhesives.
Post-Application Measuring Equipment
• Retroreflectometer.
Test Methods
• Installation and maintenance requirements examined in accordance with NZTA P 14.
NZRF Roadmarking Materials Guide - Permanent Retroreflective Raised Pavement
Markers - Type A AS/NZS 1906.3
Quick Reference Safety Guide
Recorded Environmental Hazards
Recorded Health & Safety Incidents
Related National / International Standard Specifications
• NZTA P 14 Installation of Raised Pavement Markers
• NZTA M 12 Raised Pavement Markers
• NZTA M 12: Notes for Raised Pavement Markers – Contains NZTA Approvals for use
• AS/NZS 1906.3 Retroreflective materials and devices for road traffic control purposes -
Retroreflective Markers Type A
• ASTM D4280-02 Extended life type, non-ploughable, raised retroreflective pavement
Useful References
NZRF Roadmarking Materials Guide - Snow-Ploughable Retroreflective Raised Pavement
18 Snow-Ploughable Retroreflective Raised Pavement Markers
General Description
• A small metallic object containing a retroreflective element adhered to the pavement surface
aimed at providing both night-time visibility and audible / tactile feedback to motorists. The RRPM is designed in such a manner that the risk of it being damaged or removed by regular snow clearance operations is minimised
• A specifically designed RRPM that fits into a cast iron housing that in turn is milled into the
road surface. The cast iron housing deflects the snow plough over the RRPM.
Composition
• One alternative is an aluminium body with a variety of types of retroreflective elements used
• RRPM's designed to be placed into cast iron housings are typically impact resistant plastic.
Physical Properties
• Self-cleaning
• High impact strength
• Heat and UV resistant
• Colours: White & yellow
• Thinner than standard RRPM's with a lower profile.
Performance Properties
• Retroreflectivity: When measured in accordance with AS 1906.3 values in the range of 1.5 to
5.0 mcd/lux for an entrance angle of 0o and observation angle of 0.2o. AS/NZS 1906.3 provides table of required values.
Durability
• Regarded as "semi-long life"
• "Life" dependent on a range of factors that include but are not limited to UV exposure,
substrate, method of fixture, retroreflective lens durability, traffic type and volume etc.
• Designed such that retroreflective element can be replaced while RRPM is still in place.
Compatibility
• Can be used on most types of surfaces, bitumen, asphaltic concrete and Portland cement.
Refer to RPM Adhesives
• RRPM's designed for snow ploughable applications are typically designed with specific
housings having devices to deflect the hard rubber blade of the snow-plough.
Adhesion
• Can be used on most types of surfaces, bitumen, asphaltic concrete and Portland cement.
Refer to Two-component RPM Adhesives.
NZRF Roadmarking Materials Guide - Snow-Ploughable Retroreflective Raised Pavement
Application Parameters
• RRPM's must be clean and dry
• The slots must be at a depth such that the RRPM sits proud of the road surface by
approximately 12mm with the tips of the snow-plough deflecting surfaces below the pavement surface
• The four base lugs must be in contact with the pavement
• Refer to RPM two-component adhesives for application details
• Care must be taken to ensure that adhesive is not left on the body or lens of the RRPM, and
that the bead of adhesive round the RRPM does not obscure the reflective element
• Visual observation to confirm that RRPM type, alignment and orientation is correct
• RRPM's must not be exposed to traffic until adhesive is set or dry. Retroreflective Element Repair/Replacement
• The body casting must be cleaned of remaining traces of damaged element, this is commonly
done by sandblasting
• Appropriate two-component adhesive is to be used to adhere element to body
• Care must be taken to ensure that adhesive is not left on the body or lens of the RRPM, and
that the bead of adhesive round the RRPM does not obscure the reflective element
• Visual observation to confirm that RRPM type, alignment and orientation are correct.
Manufacturing Process
•
Testing of Physical Properties
• Raised Pavement Markers may be tested to NZTA M 12 and AS/NZS 1906.3.
Handling, storage & packaging
• Store in cool dry place with packaging protected from rain and moisture
• Protect from excessive heat or contamination from fuels, oils or greases
• Classified as Non Hazardous
Environmental Impacts
Occupational Health & Safety Hazards
Application Process
• RRPM's must be clean and dry
• Slots are machined into pavement surface to appropriate depth and width, this is commonly
done using gang saw. Care must be taken not to cut detector loop wires
• Residue and loose material is removed from slot
• The slots are filled with epoxy adhesive. Sufficient adhesive is placed to ensure that all voids
beneath and around the casting are filled or casting is adhered into position with RRPM already installed
• Refer to RPM two component adhesives for application details. Note some types may allow or require the retroreflective element to be secured to base after fixing to the pavement.
NZRF Roadmarking Materials Guide - Snow-Ploughable Retroreflective Raised Pavement
Process Monitoring Equipment
• Refer to RPM Adhesives
• Height gauge.
Post-Application Measuring Equipment
Test Methods
• Installation and maintenance requirements examined in accordance with NZTA P 14.
Quick Reference Safety Guide
Recorde d Environmental Hazards
Recorded Health & Safety Incidents
Related National / International Standard Specifications
• ASTM D4383-02 Plowable Raised Retroreflective Pavement Markers
Useful References
• Item 621 Ohio Department of Transport Specifications
NZRF Roadmarking Materials Guide - Roadstuds - Retroreflective Raised Pavement
19 Roadstuds – Retroreflective Raised Pavement Markers
General Description
• A small metallic object containing a retroreflective element adhered to the pavement surface
aimed at providing both night-time visibility and audible / tactile feedback to motorists. The RRPM is designed in such a manner that the risk of it being damaged or removed by arduous traffic conditions is minimised
• The RRPM has an anchor stem that is placed in a hole milled into the road surface.
•
Composition
• Aluminium with bi-convex lenses
• High Impact plastic and polycarbonate variations exist with prismatic lenses.
Physical Properties
• Self-cleaning
• High impact strength
• Heat and UV resistant
• Colours: Full range.
Performance Properties
• Retroreflectivity: When measured in accordance with AS 1906.3 values in the range of 1.5 to
5.0 mcd/lux for an entrance angle of 0o and observation angle of 0.2o. AS/NZS 1906.3 provides table of required values.
Durability
• Regarded as "long life"
• "Life" dependent on a range of factors that include but are not limited to UV exposure,
substrate, method of fixture, retroreflective lens durability, traffic type and volume etc.
Compatibility
• Can be used on most types of surfaces, bitumen, asphaltic concrete and Portland cement.
Refer to RPM Adhesives
•
Adhesion
• Can be used on most types of surfaces, bitumen, asphaltic concrete and Portland cement.
Refer to Two-component RPM Adhesives
Application Parameters
• RRPM's must be clean and dry
• The holes must be at a depth such that the RRPM base sits on the road surface
• The entire base must be in contact with the pavement.
• Appropriate grout is used
• Care must be taken to ensure that adhesive is not left on the body or lens of the RRPM, and
that the bead of adhesive round the RRPM does not obscure the reflective element
• Visual observation to confirm that RRPM type, alignment and orientation is correct
• RRPM's must not be exposed to traffic until grout is set.
NZRF Roadmarking Materials Guide - Roadstuds - Retroreflective Raised Pavement
Manufacturing Process
• Aluminium sand casting Attachment of Bi-convex lens or glass faced prismatic lens using high strength adhesive.
• Polycarbonate moulding.
• Plastic welding of polycarbonate prismatic lens with ceramic coating
•
Testing of Physical Properties
• Raised Pavement Markers may be tested to NZTA M 12 or AS/NZS 1906.3
Handling, storage & packaging
Environmental Impacts
Occupational Health & Safety Hazards
Application Process
• RRPM's must be clean and dry
• Holes are machined into pavement surface to appropriate depth. Care must be taken not to
cut detector loop wires
• Residue and loose material is removed from hole
• The holes are filled with grout, sufficient being placed to ensure that all voids beneath and
around the casting are filled
• Roadstud anchor is placed in hole and stud pressed into road surface until base is in contact
• Excess grout is cleaned from roadstud and surrounding pavement.
Process Monitoring Equipment
• Hole depth gauge.
Post-Application Measuring Equipment
Test Methods
• Installation and maintenance requirements examined in accordance with NZTA P 14.
Quick Reference Safety Guide
Recorded Env ironmental Hazards
Recorded Health & Safety Incidents
Related National / International Standard Specifications
• NZTA P 14 Installation of Raised Pavement Markers
• NZTA M 12 Raised Pavement Markers
• NZTA M 12: Notes for Raised Pavement Markers – Contains NZTA Approvals for use
• EN 1463 Parts 1 & 2 Retroreflecting Road Studs
Useful References
Prismo Roadstuds – Caplin Group Ltd
NZRF Roadmarking Materials Guide – Illuminated Raised Pavement Markers
20 Illuminated Raised Pavement Markers
General Description
• A small metallic object containing a light source retroreflective element adhered to the
pavement surface aimed at providing both night-time visibility and audible / tactile feedback to motorists
• The RRPM is powered either by an integrated solar power system or inductively from a cable
buried in the road surface close to the RPM. The inductive power system may be connected to a solar power system or to a reticulated electricity system
• The RRPM is designed in such a manner that the risk of it being damaged or removed by
arduous traffic conditions is minimised
• The RRPM commonly has an anchor stem that is placed in a hole milled into the road surface.
Composition
• Aluminium body
• High Impact plastic and polycarbonate variations exist
• Light emitting diodes (LED) and appropriate lens system.
Physical Properties
• Self-cleaning
• High impact strength
• Heat and UV resistant
• Colours: Wide range.
Performance Properties
• Typically 50d at 8ºvertical and 10ºhorizontal.
Durability
• Regarded as "long life"
• "Life" dependent on a range of factors that include but are not limited to UV exposure,
substrate, method of fixture, retroreflective lens durability, traffic type and volume etc
• Inductively powered RPM's typically have longer life.
Compatibility
• Can be used on most types of surfaces, bitumen, asphaltic concrete and Portland cement
• Fixing systems typically licenced.
Adhesion
• Can be used on most types of surfaces, bitumen, asphaltic concrete and Portland cement
• Fixing systems typically licenced.
Application Parameters
• RRPM's must be clean and dry
• The holes must be at a depth such that the RRPM base sits on the road surface
• The entire base must be in contact with the pavement
• Appropriate grout is used
• Care must be taken to ensure that adhesive is not left on the body or lens of the RRPM, and
that the bead of adhesive round the RRPM does not obscure the reflective element.
NZRF Roadmarking Materials Guide – Illuminated Raised Pavement Markers
• Visual observation to confirm that RRPM type, alignment and orientation is correct
• RRPM's must not be exposed to traffic until grout is set.
Manufacturing Process
• Aluminium sand casting
Attachment of Bi-convex lens or glass faced prismatic lens using high strength adhesive
• Polycarbonate moulding
• Insertion of light and power system
• Plastic welding of polycarbonate case
• Attachment of base.
Testing of Physical Properties
• Raised Pavement Markers may be tested to NZTA M 12, AS/NZS 1906.3.
Handling, storage & packaging
Environmental Impacts
Occupational Health & Safety Hazards
Application Process
• RPM's must be clean and dry
• Holes are machined into pavement surface to appropriate depth. Care must be taken not to
cut detector loop wires
• Residue and loose material is removed from hole
• The holes are filled with grout, sufficient being placed to ensure that all voids beneath and
around the casting are filled
• Stud anchor is placed in hole and stud pressed into road surface until base is in contact
• Excess grout is cleaned from stud and surrounding pavement
• Inductive power cable trench cut, cable placed and road surface resealed. Care must be taken
not to cut detector loop wires.
Process Monitoring Equipment
• Hole depth gauge.
Post-Application Measuring Equipment
Test Methods
• Installation and maintenance requirements examined in accordance with NZTA P 14.
Quick Reference Safety Guide
Recorded Environmental Hazards
Recorded Health & Safety Incidents
NZRF Roadmarking Materials Guide – Illuminated Raised Pavement Markers
Related National / International Standard Specifications
• NZTA P 14Installation of Raised Pavement Markers
• NZTA M 12Raised Pavement Markers
• NZTA M 12: Notes for Raised Pavement Markers – Contains NZTA Approvals for use
• EN 1463 Parts 1 & 2 Retroreflecting Road Studs
Useful References
Smart Stud – Harding Systems
Astucia – Downer EDI Works ITS
NZRF Roadmarking Materials Guide - Temporary Pavement Markers
21 Temporary Pavement Markers
General Description
• A small L shaped flexible plastic pavement marker used to hold the original line and marking
location in chip and slurry seal road maintenance operations
• The markers may be unreflective or reflective on one or both sides. The reflective markers
have a protective cover which is removed after the tar process to restore the reflective properties
• Commonly called "flickies".
Composition
• Vinyl plastic with high tack butyl adhesive pad
• Retroreflective tape (optional) Covertape on these versions.
Physical Properties
• Colours: White and yellow.
Performance Properties
Durability
• Regarded as "temporary" or disposable.
Compatibility
• Can be used on most types of surfaces, bitumen, asphaltic concrete and Portland cement.
Adhesion
• Can be used on most types of surfaces, bitumen, asphaltic concrete and Portland cement.
Application Parameters
• Commonly supplied in 100mm widths, this may be cut down by contractors
• Marker is placed at critical dimension(s) of existing markings in such a manner that risk of
removal during resealing operation is minimised.
Manufacturing Process
• Plastic extrusion
• Butyl adhesive and reflective tape application
• Cut to length.
•
Testing of Physical Properties
Handling, storage & packaging
• Store in cool dry place with packaging protected from rain and moisture
• Protect from excessive heat or contamination from fuels, oils or greases
• Classified as Non Hazardous.
Environmental Impacts
NZRF Roadmarking Materials Guide - Temporary Pavement Markers
Occupational Health & Safety Hazards
Application Process
• Temporary marker and road surface must be clean and dry.
Process Monitoring Equipment
Post-Application Measuring Equipment
Test Methods
Quick Reference Safety Guide
Recorded Environmental Hazards
Recorded Health & Safety Incidents
Related National / International Standard Specifications
Useful References
NZRF Roadmarking Materials Guide - Bituminous RPM Adhesive
22 Bituminous RPM Adhesive
General Description
• A bituminous material applied in a molten state to fix raised pavement markers to the road
•
Composition
• Petroleum asphalt (Bitumen)
• Virtually 100 per cent volume solids.
Physical Properties
• Black viscous semi-solid having Asphaltic odour
• Density 1.5 to 2
• Negligible solubility in water
• Melting point 40 to 100oC
• Boiling Point > 480oC.
•
Performance Properties
• Softening Point: >99oC when tested in accordance with ASTM D36
• Penetration: 10 to 20 mm when tested in accordance with ASTM D5
• Note: these values match bituminous binders commonly used in road construction.
•
Durability
• Regarded as a "long life" material
• Bond strength matches common pavement surfaces
• Creates / provides enhanced impact resistance for RPM / Adhesive system by cushioning
Compatibility
• May cause a break down in the resin of waterborne paint
• Bituminous adhesive placed over cold-applied plastic and waterborne paints are likely to fail
• Bituminous adhesive applied over alkyds of significant thickness, i.e. over 150 µm may fail.
Adhesion
• Can be used on most types of surfaces, bitumen, asphaltic concrete and Portland cement
• Can be applied immediately to fresh asphalt.
Application Parameters
• Application temperature is 202 to 213oC
• Material should not be heated above 215oC
• Material should be stirred or agitated regularly to avoid settling or coke build-up
• Road surface needs to be clean and dry. Moisture tests need to be conducted prior to
• Substrate prepared by air-hand / mechanical brooming or use of high velocity / high pressure
air blowing to remove loose paint, dust and dirt
• Road and air temperatures should be greater than 4oC and rising. Poor bond may develop if
road temperature falls below 4oC.
NZRF Roadmarking Materials Guide - Bituminous RPM Adhesive
• Note: RPM removal is commonly carried out at times when low road surface temperature has
a significant effect on the shear strength of the adhesive.
Manufacturing Process
Testing of Physical Properties
• NZTA P 14 requires written confirmation from the adhesive manufacturer that it is suitable
for long term fixing of markers to road pavements.
Handling, storage & packaging
• Generally supplied as small bricks in a variety of containers
• Store in cool dry place protected from rain and moisture. Presence of moisture can cause
foaming, spitting and expansion on heating
• Protect from excessive heat or contamination from fuels, oils or greases
• Classified as Non Hazardous for transportation un heated
• Flash Point exceeds 280oC
• Do not heat above Flash Point. Hot asphalt may ignite flammable mixtures on contact
• Sulphur Oxides and Hydrogen Sulphide (which are both toxic) may be released on
• Extinguishing media include Foam, Carbon Dioxide, and Dry Chemical. Water fog may be
used on flat surfaces such as roads
• Do not use water on asphalt fire in tank or other containers as it may cause violent eruption
and spreading of burning asphalt
• When Heated Typical Classification – refer to product specific data sheets
• Proper Shipping Name: Elevated Temperature Liquid
• Packing Group: III
• HazChem Code: 2W
Environmental Impacts
• May burn although not readily ignitable
• Gives off small amounts of Hydrogen Sulphide on heating Notes:
1. Heat transfer oils used in pre- melters and applicators are classified as 3Z 2. Heat transfer oils may present particular hazards, refer to related Safety Data Sheets
3. LPG commonly used as heating medium is classified as 2WE.
• In the period of 1st April 2007 to 31st March 2009, at least 3 incidents related to bitumen, and
at least 76 related to LPG were reported to ERMA.
Occupational Health & Safety Hazards
Brick Form
• Negligible Molten Form
• Fumes (Hydrogen Sulphide)
• Explosion / Fire hazard - LPG Burners.
NZRF Roadmarking Materials Guide - Bituminous RPM Adhesive
Application Process
• The bituminous material is heated to approximately 180°C in a tank connected to an
appropriate dispenser. This may be a simple trickle valve or a computerised pump.
• The adhesive is applied to the road surface to an approximate 2mm thickness that extends past
the outside edges of the RPM
• RPM's are usually applied by hand at correct location.
•
Process Monitoring Equipment
• Bitumen temperature measuring / monitoring devices.
Post-Application Measuring Equipment
Test Methods
• NZTA P 14 – Specification for installation of raised pavement markers.
Quick Reference Safety Guide
• Understand and carry instructions regarding treatment of burns
• Carry water specifically for the immediate treatment of burns
• Wear full length overalls and safety boots or shoes at all times
• Wear gloves when handling molten bitumen
• Ensure that heating vessels are free of excess water before commencing heating process
• Never operate heating systems while in transit
• Provide adequate ventilation during loading and heating of heating vessels. • Skin Protection: Wear overalls and gloves. Use face-shield where splashing may occur.
Overalls must be safe at high temperature (i.e. cotton), safety boots must be covered to prevent entry of hot bitumen, gloves or gauntlets similarly need to be worn inside sleeves to prevent entry of hot bitumen
• Eye Protection: Use full face-shield while transferring molten material and checking holding
• Inhalation: Should be handled and used in well-ventilated areas. Note: Hydrogen Sulphide in
high concentrations has no odour.
• If burnt, Do not attempt to remove any bitumen, cool the affected area with water, keep on
cooling until medical aid is available, handle carefully, avoid disturbing the burn, remove belts and other constrictions, don't remove clothing, don't attempt to clean area, don't apply lotions or ointments, cover burns free from thermoplastic with clean lint free material, keep patient warm without touching burns with blanket. Seek medical help, ensure that they read Burns Card and understand treatment. Stay with patient. Treat patient for shock. Only give small amounts of liquids at frequent intervals
1) There are gel-based products that provide safe and reliable burn cooling effects
• If eye burn, flush with water for at least 20 minutes. Don't remove bitumen, seek medical
help, ensure that they read Burns Card and understand treatment. Stay with patient. Treat patient for shock. Only give small amounts of liquids at frequent intervals.
• If dust or fumes inhaled, provide fresh air, rest and keep warm. If breathing shallow, give
oxygen. Contact a Doctor or Poisons Information Centre.
NZRF Roadmarking Materials Guide - Bituminous RPM Adhesive
Recorded Environmental Hazards
Recorded Health & Safety Incidents
• There has been at least one "Serious Harm" accident requiring skin grafts in New Zealand
related to heated bituminous products
Related National / International Standard Specifications
• ASTM D 4280 Section A1 - Standard Specification for Extended Life Type, Nonplowable,
Raised Retroreflective Pavement Markers
• NZTA P 14 Installation of Raised Pavement Markers
Useful References
• Safety Data Sheets
Gulf States Asphalt Co Inc.
• Roading New Zealand Code of Practice for the safe handling of bituminous materials used on
• RTL Raised Pavement Markers Installation Instructions
• Gel-based Burn Treatment Systems
Jackson Allison Medical & Surgical Ltd
NZRF Roadmarking Materials Guide - Two Component RPM Adhesive
23 Two Component RPM Adhesive
General Description
• A two component epoxy resin material applied in a molten state to fix raised pavement
markers and delineators to median barriers, parapets and the road surface.
•
Composition
• Two component moisture insensitive epoxy resin
• Part A normally contains epoxy resin
• Part B normally contains amine polymer.
Physical Properties
• Part A – White or grey resin paste
• Part B – Black or cream resin paste
• Filler - (if required) - White powder
• Negligible solubility in water.
•
Performance Properties
• Bond strength 450psi after 2 hours, 1800psi after 24 hours.
• Note: these values are higher than many bituminous binders commonly used in road
•
Durability
• Regarded as a "long life" material.
Compatibility
• Can be used on most types of surfaces, bitumen, asphaltic concrete and Portland cement.
Adhesion
• Can be used on most types of surfaces, bitumen, asphaltic concrete and Portland cement.
Application Parameters
• Material should be well mixed to a uniform colour
• Road and air temperatures should be greater than 5oC and rising. Poor bond may develop if
road temperature falls below 5oC
• Road surface needs to be clean and dry. Moisture tests need to be conducted prior to
• Sandblasting, waterblasting or wire brushing is recommended
• Substrate prepared by air-hand / mechanical brooming or use of high velocity / high pressure
air blowing to remove loose paint, dust and dirt.
Manufacturing Process
Testing of Physical Properties
• NZTA P 14 requires written confirmation from the adhesive manufacturer that it is suitable
for long term fixing of markers to road pavements.
NZRF Roadmarking Materials Guide - Two Component RPM Adhesive
Handling, storage & packaging
• Supplied in 500 ml, 4, 5, 20 and 200 l containers
• Store in cool dry place protected from rain and moisture
• Protect from excessive heat or contamination from fuels, oils or greases
• Classified as Non Hazardous for transportation
• Extinguishing media include Foam, Carbon Dioxide, and Dry Chemical.
Environmental Impacts
• Epoxy resin doesn't have major or identifiable volatile components
• Although both resin and hardener are not usually considered hazardous, some requirements
may be stipulated for the disposal of waste
• RPM's torn or removed from bituminous road surface are generally accompanied by all the
adhesive creating a larger object and hole than if a bituminous adhesive had been used.
Occupational Health & Safety Hazards
• Dermatitis
• Allergic dermatitis (Sensitisation)
• Severe Irritation and Chemical Burns
• Respiratory Irritation.
Application Process
• The two components are combined in a clean steel container and mixed with a slow speed
drill attached to an appropriate epoxy-mixing paddle. The two components have differing colours to aid indication of even mixing
• Appropriate filler may be added to produce a mortar for filling or vertical surfaces
• Heating may be used to allow easier placement and / or shortening set and cure times
• Material is usually trowelled or "buttered" onto base of RPM
• RPM's are usually applied by hand at correct location.
•
Process Monitoring Equipment
Post-Application Measuring Equipment
Test Methods
• NZTA P 14 – Specification for installation of raised pavement markers.
Quick Reference Safety Guide
• Epoxy resins are skin sensitising to some people. • Part A contains epoxy resin that may cause skin sensitisation or other allergic responses.
Avoid inhalation of vapour. Prevent contact with skin and eyes
• Part B contain amine polymer, avoid contact • Skin Protection: Wear overalls and gloves. Use face-shield where splashing may occur. Use
• Eye Protection: Use full face-shield / goggles while mixing.
• Inhalation: Should be handled and used in well ventilated areas
NZRF Roadmarking Materials Guide - Two Component RPM Adhesive
• If skin contact with Part A, wash immediately with soap and water.
• If eye contact with Part A flush with water for at least 20 minutes. Seek medical help.
• If contact with Part B immediately flush eyes or skin with water for at least 20 minutes. Seek
medical help. Remove contaminated clothing and shoes. Wash clothes before reuse, discard contaminated footwear.
Recorded Environmental Hazards
Recorded Health & Safety Incidents
Allergic dermatitis (Sensitisation) is common.
Related National / International Standard Specifications
• ASTM D 4280 Section A1 - Standard Specification for Extended Life Type, Nonplowable,
Raised Retroreflective Pavement Markers
• NZTA P 14 Installation of Raised Pavement Markers
Useful References
• Safety Data Sheets
Epoxy Systems Type 702.
• Fosroc TS Epoxy Adhesive Application Guide
• West Systems General Safety Guidelines
NZRF Roadmarking Materials Guide – Self-Adhesive Pads
24 Self-Adhesive Pads
General Description
• Self-adhesive squares approximately 3mm thick designed for the application of raised
pavement markers to smooth surfaces.
Composition
• Self adhesive, many are poly butyl rubber, although thermoplastic ones are available.
Physical Properties
• Semi-flexible under normal ambient conditions
• Specific Gravity 1.53.
Performance Properties
• Bond strength highly dependent on surface and application technique.
Durability
• Regarded as a "long life" material.
Compatibility
• Can be used on most types of surfaces, bitumen, asphaltic concrete and Portland cement.
Adhesion
• Can be used on most types of surfaces, bitumen, asphaltic concrete and Portland cement.
Application Parameters
• Road and air temperatures should be greater than 5oC and rising. Poor bond may develop if
road temperature falls below 5oC
• Road surface needs to be clean and dry. Moisture tests need to be conducted prior to
• Sandblasting, waterblasting or wire brushing of the pavement surface is recommended
• Substrate needs to be prepared by air-hand / mechanical brooming or use of high velocity /
high pressure air blowing to remove loose paint, dust and dirt.
Manufacturing Process
Testing of Physical Properties
• NZTA P 14 requires written confirmation from the adhesive manufacturer that it is suitable
for long term fixing of markers to road pavements.
Handling, storage & packaging
• Supplied in boxes of 200
• Store in cool dry place protected from rain and moisture
• Protect from excessive heat or contamination from fuels, oils or greases.
• Classified as Non Hazardous for transportation
• Extinguishing media include Foam, Carbon Dioxide, and Dry Chemical.
NZRF Roadmarking Materials Guide – Self-Adhesive Pads
Environmental Impacts
• Poly butyl rubber doesn't have major or identifiable volatile components in the quantities
Occupational Health & Safety Hazards
• Respiratory Irritation.
Application Process
• A clean dry surface is required
• Sweep or blow off area with compressed air to remove all loose material in a 300 mm
perimeter of where the marker will be installed
• Remove the slip sheeting from one side of the pad and place it on the ground the exposed
surface facing up
• Center the marker on the pad. Press on the marker to secure it to the pad
• Lift the marker and remove the remaining slip sheet from the other side of the pad
• Follow manufacturer's instructions as to proper orientation of the marker on the desired
• Press the marker down firmly onto road surface
• Slowly drive a vehicle on the marker and stop with a wheel directly on top of the marker
• Allow 15-20 seconds for the marker to set before removing the vehicle
Note: for optimum performance of the butyl pad, the recommended installation
temperature is 10ºC or above. When working below 10ºC the pad, marker and road surface
should be warmed to this temperature prior to installation.
Process Monitoring Equipment
Post-Application Measuring Equipment
Test Methods
• NZTA P 14 – Specification for installation of raised pavement markers.
Quick Reference Safety Guide
• Inhalation: Should be handled and used in well ventilated areas.
Recorded Environmental Hazards
Recorded Health & Safety Incidents
Related National / International Standard Specifications
• ASTM D 4280 Section A1 - Standard Specification for Extended Life Type, Nonplowable,
Raised Retroreflective Pavement Markers
• NZTA P 14 Installation of Raised Pavement Markers
Useful References
• Safety Data Sheets
NZRF Roadmarking Materials Guide - Glass Beads
25 Glass Beads
General Description
• Small spherical glass beads intended either for the surface application to a wet / unset film of
pavement marking material or combined to the marking to provide or enhance the retroreflective properties of that marking
• Roadmarking glass beads are available in a range of size, clarity and refractive index
• Various coatings are applied to reduce caking (i.e. enhance flow / add flotation), and / or to
enhance the bond between bead and the marking material. Coatings include but are not limited to silicone (anticaking), silane,
Composition
• Clear and colourless glass – amorphous non-crystalline silica.
Physical Properties
• Bulk density of approximately 2.5
• Negligible solubility in water
• Size Distribution: Drop-on - Class B in AS/NZS 2009: The size distribution when tested in accordance with AS/NZS 2009 is as follows:
Intermix - Class C in AS/NZS 2009: The size distribution when tested in accordance with AS/NZS 2009 is as follows:
Large diameter - Class D in AS/NZS 2009: The size distribution when tested in accordance with AS/NZS 2009 is as follows:
Performance Properties
• Essentially spherical
• Clear, free form opacity / inclusions / colour
• Free flowing (may be coated with flow/anti-caking compounds to assist this)
• Refractive Index:
• Standard refractive index at least 1.5
• High Index glass beads e.g. D-HR, refractive index is of the order of 1.55 or greater
(AS/NZS 2009 bench test entry level minimum requirement of 600 mcd
Durability
• Regarded as a "long life" material.
NZRF Roadmarking Materials Guide - Glass Beads
Compatibility
• Various coatings are applied to enhance the bond between bead and the marking material
• Beads applied to particular marking materials e.g. cold-applied plastic, thermoplastic, etc
require an appropriate coating. Selection of coating needs to be made in consultation with glass bead manufacturer
Application Parameters
• NZTA P 22 requires machine application, hand spreading is not allowed
• Application equipment needs to be matched to application speed and desired retroreflectivity
• Care must be taken to minimise the effects of wind, airflow past dispenser and road speed
• A rate of 270 to 300 gm/m2 is considered appropriate by AS/NZS 2009 for a smooth
substrate. Greater application rates are generally required on course surface substrates. NZTA P 22 specifies an application rate of 275gm/m2
• Beads need to be applied directly following the application of material to ensure effective
embedment without being coated in material. The use of dual gun arrangement is recommended for application of paint using high-pressure airless systems
• Optimum embedment is 60% of the bead depth
• If angular material is required to be applied in conjunction with the beads, it is recommended
that this is applied separately, immediately before the application of the glass. Mixing prior to application is not recommended
• Trafficking of the markings must not occur until material is sufficiently dry to retain beads.
Dry through times will vary significantly with materials and film builds
• Over application may reduce effectiveness of marking through dirt entrapment and shadowing
of surrounding beads.
Manufacturing Process
Testing of Physical Properties
• Beads may be tested in accordance with AS/NZS 2009.
Handling, storage & packaging
• Supplied in bags in a range of sizes of
• Store in cool dry place protected from rain and moisture
• Protect from excessive heat or contamination from fuels, oils or greases.
• Clean up spills immediately, particularly on smooth hard surfaces such as concrete
• Classified as Non Hazardous.
Environmental Impacts
• NZTA have introduced heavy metal limitations
• APAS has specified in APAS 0042 not greater than 50ppm: Arsenic, (As)Antimony (Sb),
Lead (Pb) and not greater than 10ppm: Mercury (Hg), Cadmium (as the oxide) (CdO), Chromium (hexa-valent) (Cr6+)
• Caltrans (California Department of Transport) has set upper limit of 200 ppm for heavy
NZRF Roadmarking Materials Guide - Glass Beads
Occupational Health & Safety Hazards
• Slipping on smooth surfaces
• Dusts (Should contain no free silica nor high levels of respirible dust containing heavy
Application Process – Surface Applied
• Material must be kept clean and dry to ensure smooth and constant flow
• Beads are normally surface applied under low pressure i.e. approximately 10psi (provided by
compressed air) through an appropriated designed applicator, which applies them uniformly across the width of markings with minimal wastage. Bead tank air pressures are the control
• Equipment specifically designed for application at speed (e.g. Potters Speedbeader) may be
required for higher application rates and higher marking speeds.
•
Application Process – Internally Mixed
• Intermix – Class C AS/NZS 2009 which have a relatively wide diameter distribution are
traditionally used as a constituent part to products such as thermoplastic
• Material must be kept clean and dry to ensure smooth and constant flow
• Glass beads are stirred through product using a ribbon blender or similar device
• Roadmarking material containing glass beads must be handled appropriately handled during
processing, e.g. molten thermoplastic must be stirred continuously to ensure that the beads do not settle out.
•
Process Monitoring Equipment
Bead tank air pressure gauge and regulator
Volume / mass determination devices (dispenser calibration)
Visual comparison panels.
Post-Application Measuring Equipment
Retroreflectometer.
Test Methods
• NZTA P 20 – Specification for performance based contracts
• SADOT MAT TP901 – South Australia Department of Australia Determination of Wet Film
Thickness of Road Marking Paint / Glass Bead Application Rate, Plastic Bag Method.
Quick Reference Safety Guide
• Irritation of eyes and respiratory tract may result from high dust exposures. Handle in well-
ventilated areas and limit exposure to dusts
• Glass beads are extremely slippery, flow freely and are hard to see on smooth surfaces – use
carpet / mats to trap spilt beads and clean up spills immediately.
• Eye Protection: Use goggles where there is a risk of spill of material and / or dusts.
• Inhalation: Should be handled and used in well-ventilated areas. • If eye contact flush with water until clear. Seek medical help if irritation continues.
• If dust inhaled remove to fresh air. If discomfort continues seek medical help.
Recorded Environmental Hazards
NZRF Roadmarking Materials Guide - Glass Beads
Recorded Health & Safety Incidents
Related National / International Standard Specifications
• AS/NZS 2009 – Glass beads for pavement-marking materials
• AS/NZS 3661 – Slip resistance of pedestrian surfaces
• EN 13036-4 : 2003 : Road and airfield surface characteristics - Test methods - Part 4 : Method
for measurement of slip/skid resistance of a surface - The pendulum test
• EN 1423 Roadmarking Materials – Drop on materials – Glass beads, antiskid aggregates and
mixtures of the two
• NZTA P 30 – Specification for High Performance Marking
• NZTA P 20 – Specification for performance based contracts
• NZTA P 22 – Specification for Reflectorised Pavement Marking
• NZTA T 10 Skid Resistance Deficiency Investigation and Treatment Selection
Useful References
• Basic Principles – Retroreflection Rl (night visibility) of roadmarkings caused by Glass Beads
– Zehntner Testing Instruments – www.zehntner.com
• Potters Europe Datasheet: Glass Bead Coatings
• SADOT MAT TP901 – South Australia Department of Australia Determination of Wet Film
Thickness of Road Marking Paint / Glass Bead Application Rate, Plastic Bag Method
• Safety Data Sheets
Potters Industries Pty Ltd.
• The New Line Marking System – Potters Industries Pty Ltd
• Use of Glass Beads in Pavement Marking – Potters Industries Pty Ltd.
• Visibead An Australian Experience – Potters Industries Pty Ltd
NZRF Roadmarking Materials Guide - High Index - Airport Beads
26 High Index - Airport Beads
General Description
• Glass beads having a high index of refraction which are intended for both surface application
and the incorporation into materials used for pavement marking on airport runways and other applications that require high viewing angles.
Composition
• Clear and colourless high-density barium titanate glass.
Physical Properties
• Diameters in the range of 300 to 1000 µm (0.3 to 1mm)
• Negligible solubility in water.
Performance Properties
• Refractive index of approximately 1.9 to 1.92.
Durability
• Regarded as a "long life" material.
Compatibility
• Various coatings are applied to enhance the bond between bead and the marking material.
• Beads applied to particular marking materials e.g. cold-applied plastic, thermoplastic, etc
require an appropriate coating. Selection of coating needs to be made in consultation with glass bead manufacturer.
Application Parameters
1. As intermix – High index beads may be mixed into material by the manufacturer prior to
application. These beads should be intermixed at a rate of not less than 20% by mass
2. These beads may also be applied as for Drop on – Type B beads, however higher application
rates are recommended in the order of 500 gm/m2 on smooth surfaces. Greater application rates are generally required on course surface substrates
Where Airport Beads are applied as a Drop on • Application equipment needs to be matched to application speed and desired retroreflectivity.
Beads need to be applied directly following the application of material to ensure effective embedment without being coated in material. The use of dual gun arrangement is recommended for application of paint using high-pressure airless systems
• Application equipment needs to be matched to application speed and desired retroreflectivity
• Care must be taken to minimise the effects of wind, airflow past dispenser and road speed
• Optimum embedment is 60% of the bead depth
• Trafficking of the markings must not occur until material is sufficiently dry enough to retain
beads. Dry through times will vary significantly with materials and film builds
• Over application may reduce effectiveness of marking through dirt entrapment and shadowing
of surrounding beads.
Manufacturing Process
NZRF Roadmarking Materials Guide - High Index - Airport Beads
Testing of Physical Properties
Handling, storage & packaging
• Store in cool dry place protected from rain and moisture
• Protect from excessive heat or contamination from fuels, oils or greases
• Clean up spills immediately, particularly on smooth hard surfaces such as concrete
• Classified as Non Hazardous.
Environmental Impacts
• Caltrans (California Department of Transport) has set upper limit of 200 ppm for heavy
Occupational Health & Safety Hazards
• Slipping on smooth surfaces
• Dusts (Should contain no free silica nor high levels of respirible dust containing heavy
Application Process
Where high index beads are applied as a Drop on
• Material must be kept clean and dry to ensure smooth and constant flow
• Beads are normally applied under low pressure i.e. approximately 10psi (provided by
compressed air) through an appropriated designed applicator, which applies them uniformly across the width of markings with minimal wastage. Bead tank air pressures are the control
• Equipment specifically designed for application at speed (e.g. Potters Speedbeader) may be
required for higher application rates and higher marking speeds.
Process Monitoring Equipme nt
Where high index beads are applied as a Drop on
• Bead tank air pressure gauge and regulator
• Volume / mass determination devices (dispenser calibration)
• Visual comparison panels.
Post-Application Measuring Equipment
Where high index beads are applied as a Drop on
• Retroreflectometer.
Test Methods
Quick Reference Safety Guide
• Irritation of eyes and respiratory tract may result from high dust exposures. Handle in well-
ventilated areas and limit exposure to dusts
• Glass beads are extremely slippery, flow freely and are hard to see on smooth surfaces – use
carpet / mats to trap spilt beads and clean up spills immediately.
• Eye Protection: Use goggles where there is a risk of spill of material and / or dusts.
• Inhalation: Should be handled and used in well-ventilated areas.
NZRF Roadmarking Materials Guide - High Index - Airport Beads
• If eye contact flush with water until clear. Seek medical help if irritation continues.
• If dust inhaled remove to fresh air. If discomfort continues seek medical help.
Recorded Environmental Hazards
Recorded Health & Safety Incidents
Related National / International Standard Specifications
• AS/NZS 2009 – Glass beads for pavement-marking materials
• EN 1423 Roadmarking Materials – Drop on materials – Glass beads, antiskid aggregates and
mixtures of the two
Useful References
• Safety Data Sheets
Potters Industries Pty Ltd.
• The Use of Glass Beads in Pavement Marking – Potters Industries Pty Ltd
• High Index Retroreflective Glass Beads – Potters Industries Inc.
NZRF Roadmarking Materials Guide – Retroreflective Elements
27 High Index – Retroreflective Elements
General Description
• Glass beads having a high index of refraction which are bonded together or bonded to a
suitable material to form an agglomerate which may stand proud of typical wet marking surfaces, also offering effective retroreflectivity under water
• Beads, binder, item bonded to may be made from a range of materials
• Agglomerate may be formed from 20 to 100 beads
• Products manufactured / distributed under licence.
Composition
• May include clear and colourless high-density barium titanate glass, ceramics, pigmented
Physical Propert ies
• Negligible solubility in water.
•
Performance Properties
• Refractive index typically at least 1.9.
Durability
• Regarded as a "long life" material.
Compatibility
• Beads applied to particular marking materials e.g. cold-applied plastic, thermoplastic, etc
require an appropriate coating. Selection of coating needs to be made in consultation with glass bead manufacturer.
Application Parameters
• Products distributed / applied under licence.
Manufacturing Process
Testing of Physical Properties
Handling, storage & packaging
• Store in cool dry place protected from rain and moisture
• Protect from excessive heat or contamination from fuels, oils or greases.
• Clean up spills immediately, particularly on smooth hard surfaces such as concrete
• Classified as Non Hazardous.
Environmental Impacts
• Heavy metal limitations are to soon be introduced to limit dangerous high loadings of arsenic
trioxide, lead and other heavy metals and elements.
Occupational Health & Safety Hazards
• Slipping on smooth surfaces
• Dusts (Should contain no free silica nor high levels of respirible dust containing heavy
NZRF Roadmarking Materials Guide – Retroreflective Elements
Application Process
• Products distributed / applied under licence.
Process Monitoring Equipment
Bead tank air pressure gauge and regulator
Volume / mass determination devices (dispenser calibration)
Visual comparison panels.
Post-Application Measuring Equipment
Retroreflectometer.
Test Methods
Quick Reference Safety Guide
Treat as for glass beads, i.e.:
• Irritation of eyes and respiratory tract may result from high dust exposures. Handle in well-
ventilated areas and limit exposure to dusts
• Glass beads are extremely slippery, flow freely and are hard to see on smooth surfaces – use
carpet / mats to trap spilt beads and clean up spills immediately.
• Eye Protection: Use goggles where there is a risk of spill of material and / or dusts.
• Inhalation: Should be handled and used in well-ventilated areas. • If eye contact flush with water until clear. Seek medical help if irritation continues.
• If dust inhaled remove to fresh air. If discomfort continues seek medical help.
Recorded Environmental Hazards
Recorded Health & Safety Incidents
Related National / International Standard Specifications
• AS/NZS 2009 – Glass beads for pavement-marking materials
• EN 1423 Roadmarking Materials – Drop on materials – Glass beads, antiskid aggregates and
mixtures of the two
Useful References
3M Technology for Visibility Durability & Safety
3M All Weather Paint
Prismo Clusterbead
Prismo Zebrabright
NZRF Roadmarking Materials Guide - Quartz Angular Material
28 Quartz Angular Material
General Description
• Quartz angular material which is intended for the surface application to a wet / unset film of
pavement marking material to provide or enhance the skid resistance properties of that marking
• This material may be applied in conjunction with glass beads.
Composition
• Crushed high purity quartz.
Physical Properties
• Cubic shapes
• Bulk density of in the range of 2.5 to 3
• Negligible solubility in water
• May be covered by licencing arrangements.
•
Performance Properties
• Hardness approximately Mohs 7
Durability
• Regarded as a "long life" material.
Compatibility
• Can be used with all types of roadmarking materials.
Adhesion
• Can be used with all types of roadmarking materials.
Application Parameters
• Machine application recommended
• Application equipment needs to be matched to application speed and desired skid resistance
• Rates of 200 to 275 gm/m2 are considered appropriate for many materials / substrates to
achieve skid resistance values similar to common road surfaces
• If angular material is required to be applied in conjunction with the beads, it is recommended
that this is applied separately, immediately before the application of the glass. Mixing prior to application is not recommended. Material needs to be matched to bead size. An application rate of 1 part angular material to 2 parts beads may be found to be sufficient
• Trafficking of the markings must not occur until material is sufficiently dry to retain beads.
Dry through times will vary significantly with materials and film builds
• Over application may reduce effectiveness of marking through dirt entrapment and shadowing
of surrounding beads.
Manufacturing Process
Testing of Physical Properties
NZRF Roadmarking Materials Guide - Quartz Angular Material
Handling, storage & packaging
• Commonly supplied in 25 kg bags
• Store in cool dry place protected from rain and moisture
• Protect from excessive heat or contamination from fuels, oils or greases
• Clean up spills immediately, as is highly abrasive
• Classified as Non Hazardous.
Environmental Impacts
Occupational Health & Safety Hazards
• Dusts (Should contain no free silica nor high levels of respirible dust containing heavy
Application Process
• Material must be kept clean and dry to ensure smooth and constant flow
• Angular material can be applied under pressure (provided by compressed air) through an
appropriated designed applicator, which applies it uniformly across the width of markings with minimal wastage. Supply tank air pressures are the control
• Angular material may be pre-mixed with glass beads, although this method may suffer from
separation of materials during transportation.
•
Process Monitoring Equipment
• Supply tank air pressure gauge and regulator (if pressure delivery)
• Volume / mass determination devices (dispenser calibration)
• Visual comparison panels.
Post-Application Measuring Equipment
• Skid Resistance Testers.
Test Methods
• NZTA P 20 – Specification for performance based contracts
• NZTA P 22 – Specification for Reflectorised Pavement Marking
• NZTA P 30 – Specification for High Performance Marking
• TRL Overseas Road Note 3 – A guide to surface dressing in Tropical and Subtropical
• EN 13036-4 : 2003 : Road and airfield surface characteristics - Test methods - Part 4 : Method
for measurement of slip/skid resistance of a surface - The pendulum test
• TRL Road Note 39: Design Guide for Road Surface Dressing
• NZTA T 10 Skid Resistance Deficiency Investigation and Treatment Selection.
Quick Reference Safety Guide
• Irritation of eyes and respiratory tract may result from high dust exposures. Handle in well-
ventilated areas and limit exposure to dusts
• Quartz angular material is extremely abrasive – clean up spills immediately.
NZRF Roadmarking Materials Guide - Quartz Angular Material
• Eye Protection: Use goggles where there is a risk of spill of material and / or dusts.
• Inhalation: Should be handled and used in well-ventilated areas. • If eye contact flush with water until clear. Seek medical help if irritation continues.
• If dust inhaled remove to fresh air. If discomfort continues seek medical help.
Recorded Environmental Hazards
Recorded Health & Safety Incidents
Related National / International Standard Specifications
• AS/NZS 3661 – Slip resistance of pedestrian surfaces
• EN 13036-4 : 2003 : Road and airfield surface characteristics - Test methods - Part 4 : Method
for measurement of slip/skid resistance of a surface - The pendulum test
• EN 1423 Roadmarking Materials – Drop on materials – Glass beads, antiskid aggregates and
mixtures of the two
• NZTA P 30 – Specification for High Performance Marking
• NZTA P 20 – Specification for performance based contracts
• NZTA P 22 – Specification for Reflectorised Pavement Marking
• NZTA T 10 Skid Resistance Deficiency Investigation and Treatment Selection
• TRL Road Note 39: Design Guide for Road Surface Dressing
• TRL Overseas Road Note 3 – A guide to surface dressing in Tropical and Subtropical
Useful References
• Various – Potters Industries Pty Ltd
NZRF Roadmarking Materials Guide - Silica Friction Material
29 Silica Friction Material
General Description
• Silica friction material which is intended for the surface application to a wet / unset film of
pavement marking material to provide or enhance the skid resistance properties of tha t marking
• This material may be applied in conjunction with glass beads.
Composition
• Silica sand.
Physical Properties
• Bulk density of in the range of 2.5 to 3
• Negligible solubility in water
• Varying shades of white
• Irregular shapes, shape varies significantly between individual particles
• Note: difficulty with sand is that it may be formed by a variety of materials and its
characteristics may vary dramatically.
Performance Properties
• Hardness approximately Mohs 6 to 7
• Note: difficulty with sand is that it may be formed by a variety of materials and its
characteristics may vary dramatically.
Durability
• Regarded as a "long life" material, however see note above.
Compatibility
• Can be used with all types of roadmarking materials.
Adhesion
• Can be used with all types of roadmarking materials.
Application Parameters
• Machine application recommended
• Application equipment needs to be matched to application speed and desired skid resistance
• Rates of 200 to 275 gm/m2 are considered appropriate for many materials / substrates to
achieve skid resistance values similar to common road surfaces
• If silica friction material is required to be applied in conjunction with the beads, it is
recommended that this is applied separately, immediately before the application of the glass. Mixing prior to application is not recommended. Material needs to be matched to bead size. An application rate of 1 part silica sand to 2 parts beads may be found to be sufficient
• Trafficking of the markings must not occur until material is sufficiently dry to retain material.
Dry through times will vary significantly with materials and film builds
• Over application may reduce effectiveness of marking through dirt entrapment and shadowing
of surrounding beads.
Manufacturing Process
Quarried from either natural rock or sourced from rivers.
NZRF Roadmarking Materials Guide - Silica Friction Material
Testing of Physical Properties
Handling, storage & packaging
• Store in cool dry place protected from rain and moisture
• Protect from excessive heat or contamination from fuels, oils or greases
• Clean up spills immediately, as is highly abrasive
• Classified as Non Hazardous.
Environmental Impacts
Occupational Health & Safety Hazards
• Dusts (Should contain no free silica nor high levels of respirible dust containing heavy
Application Process
• Material must be kept clean and dry to ensure smooth and constant flow
• Angular material can be applied under pressure (provided by compressed air) through an
appropriated designed applicator, which applies them uniformly across the width of markings with minimal wastage. Supply tank air pressures are the control
• Silica friction material may be pre-mixed with glass beads, although this method may suffer
from separation of materials during transportation.
•
Process Monitoring Equipment
• Supply tank air pressure gauge and regulator (if pressure delivery)
• Volume / mass determination devices (dispenser calibration)
• Visual comparison panels.
Post-Application Measuring Equipment
• Skid Resistance Testers.
Test Methods
• NZTA P 20 – Specification for performance based contracts
• NZTA P 22 – Specification for Reflectorised Pavement Marking
• NZTA P 30 – Specification for High Performance Marking
• TRRL Road Note 3
• TRRL Road Note 27
• NZTA T 10 Skid Resistance Deficiency Investigation and Treatment Selection.
Quick Reference Safety Guide
• Irritation of eyes and respiratory tract may result from high dust exposures. Handle in well-
ventilated areas and limit exposure to dusts
• Quartz angular material is extremely abrasive – clean up spills immediately. • Eye Protection: Use goggles where there is a risk of spill of material and / or dusts.
• Inhalation: Should be handled and used in well-ventilated areas. • If eye contact flush with water until clear. Seek medical help if irritation continues.
• If dust inhaled remove to fresh air. If discomfort continues seek medical help.
NZRF Roadmarking Materials Guide - Silica Friction Material
Recorded Environmental Hazards
Recorded Health & Safety Incidents
Related National / International Standard Specifications
• AS/NZS 3661 – Slip resistance of pedestrian surfaces
• EN 13036-4 : 2003 : Road and airfield surface characteristics - Test methods - Part 4 : Method
for measurement of slip/skid resistance of a surface - The pendulum test
• EN 1423 Roadmarking Materials – Drop on materials – Glass beads, antiskid aggregates and
mixtures of the two
• NZTA P 30 – Specification for High Performance Marking
• NZTA P 20 – Specification for performance based contracts
• NZTA P 22 – Specification for Reflectorised Pavement Marking
• NZTA T 10 Skid Resistance Deficiency Investigation and Treatment Selection
• TRL Road Note 39: Design Guide for Road Surface Dressing
• TRL Overseas Road Note 3 – A guide to surface dressing in Tropical and Subtropical
Useful References
• Various – Potters Industries Pty Ltd
NZRF Roadmarking Materials Guide - Corundum Angular Material
30 Corundum Angular Material
General Description
• Corundum angular material which is intended for the surface application to a wet / unset film
of pavement marking material to provide or enhance the skid resistance properties of that marking
• This material may be applied in conjunction with glass beads.
Composition
Physical Properties
• Bulk density of in the range of 2.5 to 3
• Negligible solubility in water.
•
Performance Properties
• Hardness approximately Mohs 9.
Durability
• Regarded as a "long life" material, however see note below.
Compatibility
• Can be used with all types of roadmarking materials.
Adhesion
• Can be used with all types of roadmarking materials.
Application Parameters
• Machine application recommended
• Application equipment needs to be matched to application speed and desired skid resistance
• Rates of 200 to 275 gm/m2 are considered appropriate for many materials / substrates to
achieve skid resistance values similar to common road surfaces
• If angular material is required to be applied in conjunction with the beads, it is recommended
that this is applied separately immediately before the application of the glass. Mixing prior to application is not recommended. Material needs to be matched to bead size. An application rate of 1 part angular material to 2 parts beads may be found to be sufficient
• Trafficking of the markings must not occur until material is sufficiently dry enough to retain
material. Dry through times will vary significantly with materials and film builds
• Over application may reduce effectiveness of marking through dirt entrapment and shadowing
of surrounding beads.
Manufacturing Process
Testing of Physical Properties
Handling, storage & packaging
• Store in cool dry place protected from rain and moisture
• Protect from excessive heat or contamination from fuels, oils or greases
• Clean up spills immediately, as is highly abrasive
• Classified as Non Hazardous
NZRF Roadmarking Materials Guide - Corundum Angular Material
Environmental Impacts
Occupational Health & Safety Hazards
• Dusts (Should contain no free silica nor high levels of respirible dust containing heavy
Application Process
• Material must be kept clean and dry to ensure smooth and constant flow
• Angular material can be applied under pressure (provided by compressed air) through an
appropriated designed applicator, which applies it uniformly across the width of markings with minimal wastage. Supply tank air pressures are the control
• Angular material may be pre-mixed with glass beads, although this method may suffer from
separation of materials during transportation.
•
Process Monitoring Equipment
• Supply tank air pressure gauge and regulator (if pressure delivery)
• Volume / mass determination devices (dispenser calibration)
• Visual comparison panels.
Post-Application Measuring Equipment
• Skid Resistance Testers.
Test Methods
• NZTA P 20 – Specification for performance based contracts
• NZTA P 22 – Specification for Reflectorised Pavement Marking
• NZTA P 30 – Specification for High Performance Marking
• TRRL Road Note 3
• TRRL Road Note 27
• NZTA T 10 Skid Resistance Deficiency Investigation and Treatment Selection.
Quick Reference Safety Guide
• Irritation of eyes and respiratory tract may result from high dust exposures. Handle in well-
ventilated areas - –limit exposure to dusts
• Corundum angular material is extremely abrasive – clean up spills immediately. • Eye Protection: Use goggles where there is a risk of spill of material and / or dusts.
• Inhalation: Should be handled and used in well-ventilated areas. • If eye contact flush with water until clear. Seek medical help if irritation continues.
• If dust inhaled remove to fresh air. If discomfort continues seek medical help.
Recorded Environmental Hazards
Recorded Health & Safety Incidents
NZRF Roadmarking Materials Guide - Corundum Angular Material
Related National / International Standard Specifications
• AS/NZS 3661 – Slip resistance of pedestrian surfaces
• EN 13036-4 : 2003 : Road and airfield surface characteristics - Test methods - Part 4 : Method
for measurement of slip/skid resistance of a surface - The pendulum test
• EN 1423 Roadmarking Materials – Drop on materials – Glass beads, antiskid aggregates and
mixtures of the two
• NZTA P 30 – Specification for High Performance Marking
• NZTA P 20 – Specification for performance based contracts
• NZTA P 22 – Specification for Reflectorised Pavement Marking
• NZTA T 10 Skid Resistance Deficiency Investigation and Treatment Selection
• TRL Road Note 39: Design Guide for Road Surface Dressing
• TRL Overseas Road Note 3 – A guide to surface dressing in Tropical and Subtropical
Useful References
• Various – Potters Industries Pty Ltd
NZRF Roadmarking Materials Guide - Alkyd Paint Thinners
31 Alkyd Paint Thinners
General Description
• A colourless aromatic liquid (petrochemical) used as a diluent and cleaner for alkyd pavement
Composition
• Petroleum based solvent
• Products may include but are not limited to:
• Methyl benzene
• Phenyl methane
• Methyl benzol
Physical Properties
• Colourless aromatic liquid
• Flash Point <12oC
• Density 0.7 to 0.8 kg/l
• Highly flammable
• Solubility in water approximately 0.5 kg/m3.
Performance Properties
Application Parameters
• Refer to paint manufacturer's recommendations
• Addition to paint in excess of that specified by paint manufacturers will significantly degrade
the performance of the applied coatings
• Use of thinners other than that specified by the paint manufacturers will significantly degrade
the performance of the applied coatings.
Application Process
• Use of thinners not commonly used or desirable in application of paint by high pressure
airless paint systems
• Thinners are required for application of alkyd paints by conventional air spray equipment
• Equipment cleaned / flushed with thinners
Durability
• Addition of thinners may have a significant impact on the durability of coatings.
Environmental Impacts
• Increases VOC's of painted product directly in ratio of addition rate
• Softens, dissolves bitumen pavement surfaces
• Refer to NZRF Roadmarking Note # 11 HSNO Regulations Emergency Management
Requirements - Guideline
• In the period of 1st April 2007 to 31st March 2009, at least 9 incidents related to solvents, and
at least 80 related to unidentified hydrocarbons were reported to ERMA.
NZRF Roadmarking Materials Guide - Alkyd Paint Thinners
Handling, storage & packaging
• High flammability. Dangerous goods stores generally needed
• Haz Chem Code 3[Y]E
• UN Number 1294
• Packaging Group II
• Flash Point Less than 4oC.
Measuring Equipment
• Volume measuring containers and dipsticks.
Measurement Standards
• Not applicable.
Occupational Health & Safety Hazards
• Fire and explosion
• Fumes, Gases, Vapours
• Potential to Poison
• Potential to Infection
• Lack of Oxygen (also Fumes vapours & Gases). Confined Spaces. Vapours are heavier than
air and may pool in depressions resulting in oxygen deficiencies
• Fluid Injection
• Hazardous decomposition products on burning.
Process Monitoring Equipment
• Not applicable.
Quick Reference Safety Guide
• Provide adequate ventilation during use
• Keep away from heat and naked flame
• Avoid contact with skin and eyes
• Avoid breathing the vapour and spray mist • Inhalation: Half mask organic vapour respirator conforming to AS 1716
• Eye Protection: Chemical monogoggles
• Skin Protection: Wear silver shield or nitrile rubber gloves, overalls and chemical resistant
shoes or boots. Where splashing may occur, wear PVC apron. Use of silicone free barrier cream
• If inhaled, provide fresh air, rest and keep warm. If breathing shallow, give oxygen. Contact
a Doctor or Poisons Information Centre.
• If swallowed, DO NOT induce vomiting, give several glasses of water. Contact a Doctor or
Poisons Information Centre.
• If eye contact, wash with running water for at least 15 minutes. Seek medical attention.
• If skin contact, remove contaminated clothing. Wash skin with water using soap if available.
If persistent irritation occurs, obtain medical attention.
NZRF Roadmarking Materials Guide - Alkyd Paint Thinners
• If fluid injection occurs, contact a Doctor immediately. Injection of paint or solvents into the
skin may cause serious injury both from traumatic compression of structures and inflammation and damage from the solvents or paint itself. It is important to treat the injury surgically as soon as possible.
Recorded Environmental Hazards
Recorded Health & Safety Incidents
Related National / International Standard Specifications
Useful References
• Safety Data Sheets
Shell New Zealand Ltd – Chemicals Division
Damar Industries (NZ) Ltd
Resene Paints Ltd
• Department of Labour Publication "Practical Guidelines for the Safe Use of Organic
• Health Safety & Environment Guide for Printing & Related Industries -
NZRF Roadmarking Materials Guide - Chlorinated Rubber Modified Alkyd Paint
Thinners
32 Chlorinated Rubber Modified Alkyd Paint Thinners
General Description
• A colourless aromatic liquid (petrochemical) used as a diluent and cleaner for chlorinated
rubber modified alkyd pavement marking paint.
Composition
• Petroleum based solvent
• Products may include but are not limited to:
• Methyl benzene
• Phenyl methane
• Methyl benzoyl.
Physical Properties
• Colourless aromatic liquid
• Flash Point <12oC
• Density 0.7 to 0.8 kg/l
• Highly flammable
• Solubility in water approximately 0.5 kg/m3
Application Parameters
• Refer to paint manufacturer's recommendations
• Addition to paint in excess of that specified by paint manufacturers will significantly degrade
the performance of the applied coatings
• Use of thinners other than that specified by the paint manufacturers will significantly degrade
the performance of the applied coatings.
Application Process
• Use of thinners not commonly used or desirable in application of paint by high pressure
airless paint systems
• Thinners are required for application of alkyd paints by conventional air spray equipment
• Equipment cleaned / flushed with thinners.
Durability
• Addition of thinners may have a significant impact on the durability of coatings.
Environmental Impacts
• Increases VOC's of painted product directly in ratio of addition rate
• Softens, dissolves bitumen pavement surfaces
• Refer to NZRF Roadmarking Note # 11 HSNO Regulations Emergency Management
Requirements - Guideline
• In the period of 1st April 2007 to 31st March 2009, at least 9 incidents related to solvents, and
at least 80 related to unidentified hydrocarbons were reported to ERMA.
NZRF Roadmarking Materials Guide - Chlorinated Rubber Modified Alkyd Paint
Thinners
Handling, storage & packaging
• High flammability. Dangerous goods stores generally needed
• Haz Chem Code 3[Y]E
• UN Number 1294
• Packaging Group II
• Flash Point Less than 4oC.
Measuring Equipment
• Volume measuring containers and dipsticks.
Measurement Standards
• Not applicable.
Occupational Health & Safety Hazards
• Fire and explosion
• Fumes, Gases, Vapours
• Potential to Poison
• Potential to Infection
• Lack of Oxygen (also Fumes vapours & Gases). Confined Spaces. Vapours are heavier than
air and may pool in depressions resulting in oxygen deficiencies
• Fluid Injection
• Hazardous decomposition products on burning.
Process Monitoring Equipment
• Not applicable
Quick Reference Safety Guide
• Provide adequate ventilation during use
• Keep away from heat and naked flame
• Avoid contact with skin and eyes
• Avoid breathing the vapour and spray mist. • Inhalation: Half mask organic vapour respirator conforming to AS 1716
• Eye Protection: Chemical mono-goggles
• Skin Protection: Wear silver shield or nitrile rubber gloves, overalls and chemical resistant
shoes or boots. Where splashing may occur, wear PVC apron. Use of silicone free barrier cream.
• If inhaled, provide fresh air, rest and keep warm. If breathing shallow, give oxygen. Contact
a Doctor or Poisons Information Centre.
• If swallowed, DO NOT induce vomiting, give several glasses of water. Contact a Doctor or
Poisons Information Centre.
• If eye contact, wash with running water for at least 15 minutes. Seek medical attention.
• If skin contact, remove contaminated clothing. Wash skin with water using soap if available.
If persistent irritation occurs, obtain medical attention.
NZRF Roadmarking Materials Guide - Chlorinated Rubber Modified Alkyd Paint
Thinners
• If fluid injection occurs, contact a Doctor immediately. Injection of paint or solvents into the
skin may cause serious injury both from traumatic compression of structures and inflammation and damage from the solvents or paint itself. It is important to treat the injury surgically as soon as possible.
Recorded Environmental Hazards
Recorded Health & Safety Incidents
Related National / International Standard Specifications
Useful References
• Safety Data Sheets
Shell New Zealand Ltd – Chemicals Division
Damar Industries (NZ) Ltd
Resene Paints Ltd
• Department of Labour Publication "Practical Guidelines for the Safe Use of Organic
• Health Safety & Environment Guide for Printing & Related Industries -
NZRF Roadmarking Materials Guide - Waterborne Paint Thinners
33 Waterborne Paint Thinners
Important Note:
Waterborne paints are not normally designed to be thinned in any way. The paint as supplied is
specified by paint companies to deliver a balance of viscosity for handling with sufficient flow to
allow film builds to be achieved without excessive drain on equipment. Any thinning must be
carried out with care using materials recommended by the supplier to ensure that chemical
composition of paint remains within specified limits for pH etc.
General Description
• A colourless liquid (containing various alcohols and glycols) used as a diluent and cleaner for
waterborne pavement marking paint.
Composition
• Products may include but are not limited to:
• Ethyl alcohol
• Hydroxy –4 Methyl 2 pentanone
• Diacetone alcohol.
Physical Properties
• Clear low viscosity liquid with hydrocarbon odour
• Flash Point can be less than 15oC
• Density 0.8 to 1 kg/l
• Highly flammable
• Miscible in water.
Application Parameters
• Refer to paint manufacturer's recommendations
• Addition to paint in excess of that specified by paint manufacturers will significantly degrade
the performance of the applied coatings
• Use of thinners other than that specified by the paint manufacturers will significantly degrade
the performance of the applied coatings.
Application Process
• Use of thinners not commonly used or desirable in application of paint by high pressure
airless paint systems
• Thinners are required for application of waterborne paints by conventional air spray
• Equipment cleaned / flushed with thinners.
Durability
• Addition of thinners may have a significant impact on the durability of coatings.
Environmental Impacts
• Highly miscible with water
• Poisonous, oxidising agent, harmful to organisms
• Refer to NZRF Roadmarking Note # 11 HSNO Regulations Emergency Management
Requirements - Guideline
NZRF Roadmarking Materials Guide - Waterborne Paint Thinners
Handling, storage & packaging
• High flammability. Dangerous goods stores generally needed
• Haz Chem Code 3[Y]E
• UN Number 1263
• Packaging Group II
• Flash Point can be less than 15oC
• Plastic containers only suitable if approved for flammable liquids
Measuring Equipment
• Volume measuring containers and dipsticks.
Measurement Standards
• Not applicable.
Occupational Health & Safety Hazards
• Fire and explosion
• Fumes, Gases, Vapours
• Potential to Poison
• Potential to Infection
• Lack of Oxygen (also Fumes vapours & Gases). Confined Spaces. Vapours are heavier than
air and may pool in depressions resulting in oxygen deficiencies
• Fluid Injection
• Hazardous decomposition products on burning.
Process Monitoring Equipment
• Not applicable.
Quick Reference Safety Guide
• Provide adequate ventilation during use
• Keep away from heat and naked flame
• Avoid contact with skin and eyes
• Avoid breathing the vapour and spray mist. • Inhalation: Half mask organic vapour respirator conforming to AS 1716
• Eye Protection: Chemical mono-goggles
• Skin Protection: Wear neoprene or nitrile rubber gloves, overalls and chemical resistant shoes
or boots. Where splashing may occur, wear PVC apron. Use of silicone free barrier cream.
• If inhaled, Provide fresh air, rest and keep warm. If breathing shallow, give oxygen. Contact
a Doctor or Poisons Information Centre.
• If swallowed, DO NOT induce vomiting, give several glasses of water. Contact a Doctor or
Poisons Information Centre.
• If eye contact, wash with running water for at least 15 minutes. Seek medical attention.
• If skin contact, remove contaminated clothing. Wash skin with water using soap if available.
If persistent irritation occurs, obtain medical attention.
• If fluid injection occurs, contact a Doctor immediately. Injection of paint or solvents into the
skin may cause serious injury both from traumatic compression of structures and
NZRF Roadmarking Materials Guide - Waterborne Paint Thinners
inflammation and damage from the solvents or paint itself. It is important to treat the injury surgically as soon as possible.
Recorded Environmental Hazards
Recorded Health & Safety Incidents
Related National / International Standard Specifications
Useful References
• Safety Data Sheets
Damar Industries (NZ) Ltd
Resene Paints Ltd
NZRF Roadmarking Materials Guide - Cold Applied Plastic Thinners
34 Cold Applied Plastic Thinners
General Description
• A translucent blend of Methyl methacrylate, PMMA resin and wetting agents used as
viscosity reducer used for Cold Applied Plastic Long life paints.
•
Composition
• Products may include but are not limited to:
• Methyl methacrylate
• Poly methyl methacrylate.
Physical Properties
• Colourless liquid with a sweet sharp fruity odour
• Flash Point <10.0oC
• Density 0.97 kg/l
• Highly flammable
• Boiling Point 101°C.
Performance Properties
•
Application Parameters
• Refer to paint manufacturer's recommendations
• Addition to paint in excess of that specified by paint manufacturers will significantly degrade
the performance of the applied coatings
• Use of thinners other than that specified by the paint manufacturers will significantly degrade
the performance of the applied coatings.
•
Application Process
• Use of thinners not commonly used or desirable in application of paint.
Durability
• Addition of thinners may have a significant impact on the durability of coatings.
Environmental Impacts
• In the period of 1st April 2007 to 31st March 2009, at least 9 incidents related to solvents, and
at leasT 80 related to unidentified hydrocarbons were reported to ERMA.
Handling, storage & packaging
• 20L & 200L
• High flammability. Dangerous goods stores generally needed
• Haz Chem Code 3(Y)E
• UN Number 1247
• Packaging Group II
• Flash Point <10.0oC.
Measuring Equipment
• Volume measuring containers and dipsticks.
NZRF Roadmarking Materials Guide - Cold Applied Plastic Thinners
Measurement Standards
• Not applicable.
Occupational Health & Safety Hazards
• Fire and explosion
• Fumes, Gases, Vapours
• Potential to Poison
• Potential to Infection
• Lack of Oxygen (also Fumes vapours & Gases). Confined Spaces. Vapours are heavier than
air and may pool in depressions resulting in oxygen deficiencies
• Fluid Injection
• Hazardous decomposition products on burning
• It may polymerise in the presence of catalyst or elevated temperature.
Process Monitoring Equipment
• Not applicable
Quick Reference Safety Guide
• Provide adequate ventilation during use
• Keep away from heat and naked flame
• Avoid contact with skin and eyes
• Avoid breathing the vapour and spray mist • Inhalation: Type A Filter of sufficient capacity
• Eye Protection: Chemical mono goggles
• Skin Protection: Wear nitrile rubber gloves, overalls and chemical resistant shoes or boots.
Where splashing may occur, wear PVC apron. Use of silicone free barrier cream.
• If inhaled, provide fresh air, rest and keep warm. If breathing shallow, give oxygen. Contact
a Doctor or Poisons Information Centre.
• If swallowed, DO NOT induce vomiting, give several glasses of water. Contact a Doctor or
Poisons Information Centre.
• If eye contact, wash with running water for at least 15 minutes. Seek medical attention.
• If skin contact, remove contaminated clothing. Wash skin with water using soap if available.
If persistent irritation occurs, obtain medical attention.
• If fluid injection occurs, contact a Doctor immediately. Injection of paint or solvents into the
skin may cause serious injury both from traumatic compression of structures and inflammation and damage from the solvents or paint itself. It is important to treat the injury surgically as soon as possible.
Recorded Environmental Hazards
This material and its container must be disposed of as hazardous waste
Recorded Health & Safety Incidents
Related National / International Standard Specifications
NZRF Roadmarking Materials Guide - Cold Applied Plastic Thinners
Useful References
• Safety Data Sheets
Damar Industries (NZ) Ltd
NZRF Roadmarking Materials Guide - Waterborne Catalysts
35 Waterborne Paint Catalysts
General Description
• A material used as a drying accelerant (catalyst) for waterborne pavement marking paint.
Composition
• Products are covered by patents and licencing agreements, e.g. Damar BST.
Physical Properties
• May be a clear low viscosity liquid with strong organic odour
• Water absorbing, acidified spherical beads, known as a drying adjuvants or dry speed
boosters, which rapidly drop the pH and absorb water which is released slowly after the paint has dried.
Application Parameters
• Refer to paint manufacturer's recommendations
• The use of a drying adjuvant can be recommended when drying conditions are less than
optimal. This can be characterised by high humidity, low temperature and low air flow. However, as has been demonstrated, there is a reasonable case to be made for use when there is a chance of rain impacting the work within 2 hours, protection of the work is limited due to local regulations or road geometry, or the specifications calling for a greater thickness of paint than might reasonably dry in the time provided
• Addition to paint in excess of the rates specified by paint manufacturers will significantly
degrade the performance of the applied coatings.
•
Application Process
• Covered by Licence agreements
• Catalyst matched to base material
• Commonly applied during the pavement marking application.
Durability
• Use of catalysts / drying agents other than that specified by the paint manufacturer will
significantly degrade the performance of the applied coatings.
Environmental Impacts
Handling, storage & packaging
• Supplied in a range of container sizes
• Store in cool dry place protected from rain and moisture
• Protect from excessive heat or contamination from fuels, oils or greases
• Clean up spills immediately, particularly on smooth hard surfaces such as concrete
Measuring Equipment
• Volume measuring containers and dipsticks.
Measurement Standards
• Not applicable.
NZRF Roadmarking Materials Guide - Waterborne Catalysts
Occupational Health & Safety Hazards
Process Monitoring Equipment
Quick Reference Safety Guide
Recorded Environmental Hazards
Recorded Health & Safety Incidents
Related National / International Standard Specifications
Useful References
• Damar BST Data Sheet - Damar Industries (NZ) Ltd
• Potters Visilok® TPD.
NZRF Roadmarking Materials Guide - Benzyl Peroxide Catalyst for PMMA
36 Benzoyl Peroxide
General Description
• A material used as the catalyst for poly methyl methacrylate (PPMA) / cold applied plastic
Composition
• Benzoyl peroxide, (C14 H10 O4), combined with other materials to facilitate mixing
• May be either of liquid or powder form (with or without beads)
Physical Properties
• Appearance - White, granular, crystalline solid.
• Slightly soluble in water
• Melting Point - 103-105 °C
• Specific Gravity - 1.3340 @ 25 °C
• Flash Point – 40 °C (CC)
• Auto-ignition Temperature – 80 ºC
• Decomposes explosively above 105 ºC
• Appearance – White paste with slight ester odour
• Negligible solubility in water
• Boiling point – Decomposes
• Specific Gravity – 1.2 @ 25 °C
• Flash Point – Not Applicable
Application Parameters
• Refer to CAP manufacturer's recommendations
• Addition to CAP in excess of the rates specified by manufacturers will significantly degrade
the performance of the applied coatings.
Application Process
• Covered by Licence agreements
• Catalyst matched to base material
Durability
• Use of catalysts other than that specified by the CAP manufacturer will significantly degrade
the performance of the applied coatings.
Environmental Impacts
• Keep combustibles (wood, paper, clothing, oil etc.) away from spilled material.
• Prevent entry into waterways, drains, confined areas. Use water spray to knock down or divert
vapour clouds. Use clean, non-sparking tool to collect materia l and place it into loosely-covered plastic containers for later disposal. Absorb with earth, sand or other non-combustible material and transfer to container.
NZRF Roadmarking Materials Guide - Benzyl Peroxide Catalyst for PMMA
•
Handling, storage & packaging
Powder
• Store in cool place and out of direct sunlight
• Store in well ventilated area
• Keep containers securely sealed and protected against physical damage
• Dangerous goods of Class 5.2 (Organic Peroxide) are incompatible in a placard load with any
of the following: Class 1, Class 2, Class 3, Class 4, Class 5.1, Class 7, Class 8, Fire risk substances and Combustible liquids
• Store in original containers - Do not return product which has been taken out of original
• Protect from shock, friction, fire and other sources of ignition
• Proper Shipping Name - Organic Peroxide Type C, Solid Liquid
• Keep containers tightly closed when not in use. Rotate stock using the oldest material first
• Do not use near food or drink
• Avoid skin and eye contact - Wear personal protection equipment
• Reseal containers immediately after use to prevent contamination and drying
• Keep material in its original container away from any incompatible materials, direct sunlight
or other sources of heat
• Do not store with food or drink.
• Store in an isolated, cool and well-ventilated area and remove only as needed
• Keep material sealed to prevent contamination and drying.
• Other precautions - Avoid any conditions that may cause contamination and drying. Do not
leave material uncovered. Containers of this material may be hazardous when empty since they retain product residues, observe all warnings and precautions listed. Use good personal hygiene practices. Wash hands before eating, drinking, smoking, or using toilet facilities.
Measuring Equipment
• Volume measuring containers and dipsticks.
Measurement Standards
• Not applicable.
Occupational Health & Safety Hazards
Powder
• Acute - Swallowed May cause abdominal pain, nausea and vomiting
• Acute (Eye) - irritating to eyes, may cause redness and pain
• Acute (Skin) - May cause sensitisation by skin contact, may cause redness and pain, stinging
or burning sensation may occur for a brief time after application to skin
• Acute (Inhaled) -Dust may cause irritation to mucous membranes with coughing and sore
• Chronic - Repeated or prolonged skin contact may cause chronic dermatitis, may cause
asthmatic effects in some individuals.
Liquid • Skin Absorption - May cause irritation and redness of the skin
• Eye Contact - Eye contact may cause inflammation
NZRF Roadmarking Materials Guide - Benzyl Peroxide Catalyst for PMMA
• Ingestion - Poison by ingestion, may cause human systemic eye effects by ingestion:
hallucinations distorted perceptions, nausea or vomiting and kidney, urethra or bladder changes
• Inhalation - Not expected to be an inhalation hazard.
Process Monitoring Equipment
• Dosing rate monitors
Quick Reference Safety Guide
• Provide adequate ventilation during use
• Keep away from heat, naked flame, or impact
• Avoid contact with skin and eyes Powder
• Swallowed - Rinse mouth thoroughly with water immediately. Give plenty of water to drink
and induce vomiting. Use fingers in the throat, Ipecac Syrup (APF) or similar emetic. Seek immediate medical assistance.
• Eye- Immediately irrigate with copious quantity of water for at least 15 minutes. Eyelids to be
held open. Seek immediate medical assistance.
• Skin- Wash affected areas with copious quantities of water immediately. Remove
contaminated clothing and wash before re-use. Seek medical attention.
• Inhaled - Remove victim to fresh air. Employ artificial respiration if indicated. Seek medical
Liquid • Skin - Immediately remove any contaminated clothing. Wash contaminated area thoroughly
with soap and copious amounts of water for at least 15 minutes. If irritation or adverse symptoms develop, seek medical attention.
• Eyes - Remove any contact lenses at once. Flush eyes with water for at least 15 minutes.
Ensure adequate flushing by separating the eyelids with fingers. If irritation or adverse symptoms develop, seek medical attention.
• Ingestion - Contact a physician, hospital or Poison Control Centre at once. Do not induce
Recorded Enviro nmental Hazards
Recorded Health & Safety Incidents
• Effects of over-exposure - May cause dermatitis, asthmatic effects, testicular atrophy, and
vasodilatation. Mutation data reported.
Related National / International Standard Specifications
Useful Refere nces
• Damar Beads Hardener Data Sheet - Damar Industries (NZ) Ltd
• Benox Safety Data Sheet
NZRF Roadmarking Materials Guide – Modified Epoxy Resin
37 Modified Epoxy Resin
General Description
• A two-part modified cold-applied thermosetting epoxy resin designed for use with a surface
applied aggregate having an appropriate colour and skid resistance. This product can be used either as a binder for a high friction surfacing system or permanent overlay marking system.
Composition
• Epoxy pavement overlay material is tailored for specific conditions and application methods
• Products are covered by patents and licencing agreements
• May contain inorganic and organic colour pigments
Physical Properties
• Appearance – Coloured viscous liquids
• Viscosity Part A 3,000 cps @25 ºC
• Viscosity Part B 15,000 cps @25 ºC
• Density Part A 1.0 kg/l
• Density Part B 1.1 kg/l
• Odour – Characteristic, Part A – ammonical
• Boiling Points >190 ºC
• Flash Points .100 ºC
• Insoluble in water
Performance Properties
• Odourless after cure
• Shore Hardness Type D in the range of 65 to 75
• Tensile Strength (ASTM D638) >10 N/mm² after 24 hours, > 13 after 7 days
Durability
• Regarded as "long life" as far as "wear" is concerned
• Resistant to oil, petrol and de-icing salts
Compatibility
• Can be used on many types of surfaces.
Adhesion
• Can be applied to most pavement surfaces and textures
• Friable / highly absorbent surfaces such as porous concrete require priming.
Application Parameters
• Both components need to be thoroughly machine stirred. It is recommended that the
component containing the hardener is machine stirred
• Part A and Part B must be proportioned to the correct ration (typically 50:50 ± 4% by weight)
• Road and air temperatures should be in the range of 5 and rising up to a maximum of 40oC
• Recommended application rates of 1 to 2.5 kg/m2. Increased rates required for surfaces having
greater texture depths
NZRF Roadmarking Materials Guide – Modified Epoxy Resin
• Use of specially built applicators which require accurate measuring devices and / or calibrated
• Hand applied binder requires serrated edged squeegee to control applied thickness
• Aggregate application by hand requires skill and experience
• Aggregate application rates need to be in excess of 6 kg/m² to ensure sufficient coverage /
embedment – no compaction is required.
Manufacturing Process
Testing of Physical Properties
• NZTA M 20, NZTA M 25 and AS 4049.4
Handling, storage & packaging
• Available in a variety of containers from 25 to 1500 kg
• Keep away from food and drink
• Store in cool dry place protected from rain, sun and moisture
• Protect from excessive heat or contamination from fuels, oils or greases
• Typical Classification – refer to product specific data sheets
• Proper Shipping Name: Environmentally Hazardous Substance, Liquid, NOS
• UN Number: 3082
• HazChem Code: 2X
• Proper Shipping Name: Corrosive Liquid, Toxic, NOS
• UN Number: 2922
• HazChem Code: None
Environmental Impacts
• Do not allow to enter drains, rivers and watercourses
• Toxic to aquatic organisms, may cause long-term adverse effects in the aquatic environment
• Materials are special waste and need to be disposed of by licenced contractor – Contaminated
packaging or clothing should be disposed of identically to the product itself
• Uncontaminated packaging may be treated as household waste
• Refer to NZRF Roadmarking Note # 11 HSNO Regulations Emergency Management
Requirements - Guideline
NZRF Roadmarking Materials Guide – Modified Epoxy Resin
Occupational Health & Safety Hazards
Part A
• Irritating to eyes and skin
• May cause sensitisation by skin contact
• Carcinogen, Category 2
• May cause cancer Part B • Toxic in contact with skin or if swallowed
• Causes burns
• Carcinogen, Category 2
• May cause cancer
Application Process
• Products and their application are covered by patents and licencing agreements
• The two part epoxy binder material cannot be applied on a wet surface, if the ambient and/or
surface temperature is below 5 ºC or above 40 ºC, or if the anticipated weather conditions would prevent the proper application of the surface treatment as determined by the manufacturer
• Existing surfaces need to be cleaned by use of mechanical sweepers, high pressure air or other
• All existing pavement markings and utilities are covered / protected prior to placement.
• All inadequately sealed joints and cracks greater than 5 mm are filled / sealed with the
manufacturers approved crack sealant.
• The two part modified epoxy binder components part A / part B are combined (proportioned
to the correct ratio of 50:50 ± 4% by weight and mixed using a low speed high torque drill fitted with a helical stirrer
• The binder material is then spread by serrated edge squeegee such that it is uniformly
distributed over the pavement section to be treated and within the temperature range specified
• Operations need to proceed in such a manner that will not allow the epoxy material to chill,
set up, dry, or otherwise impair retention of the covered aggregate.
• Immediately after the binder is laid the aggregate is spread onto the binder at a rate in excess
of 6 kg/m². The placement of this material does not require any compaction.
• The treatment is allowed to cure in accordance with manufacturer recommendations,
approximately 3 hours at an ambient temperature of 4 C and rising
• The excess aggregate is removed by hand or suction sweeping before opening to traffic.
Process Monitoring Equipment
• Weighing devices
• Atmospheric condition measuring / monitoring devices
Post-Application Measuring Equipment
• Skid resistance testers
Test Methods
• Skid Resistance, refer also to Glass Beads and Angular Material
NZRF Roadmarking Materials Guide – Modified Epoxy Resin
Quick Reference Safety Guide
• Part A causes burns
• Part B may cause sensitisation by skin contact • Skin Protection: Wear overalls, boots and gloves. Use chemical resistant face-shield where
splashing may occur. Use barrier creams
• Eye Protection: Use full face-shield / goggles while mixing.
• Inhalation: Use respirator, should be handled and used in well ventilated areas • General: In all cases of doubt, or where symptoms persist, seek medical attention
• Eye Contact: Rinse immediately with water for at least 15 minutes and get medical attention
• Skin Contact: Wipe with absorbent paper disposable towels. Wash with plenty of soap and
water – do not use organic solvents. In case of dermatitis or if irritation persists, get medical attention.
• Inhalation: Move affected person to fresh air. In case of irritation to respiratory system or
mucous membranes, or if you feel unwell or in case of prolonged exposure, get medical attention.
• Ingestion: Immediately rinse the mouth with water. If swallowing has occurred drink water in
small sips. Do not induce vomiting. Seek medical attention promptly.
• Contaminated clothing and shoes: Remove immediately. Wash clothes before reuse, discard
contaminated footwear.
Recorded Environmental Hazards
Recorded Health & Safety Incidents
• Reports of dermatitis, and allergic dermatitis (Sensitisation) are common.
• Specialist sector groups interested in the safe use of epoxies established overseas
Related National / International Standard Specifications
• Products and their application are covered by patents and licencing agreements
• AS 4049.4
Useful References
• Prismo Tyregrip® Safety Data Sheets
• Integrated Traffic Solutions Ltd TyreGrip Technical Data Sheets
NZRF Roadmarking Materials Guide – Modified Polyurethane Resin
38 Modified Polyurethane Resin
General Description
• A two-part modified cold-applied thermosetting polyurethane resin designed for use with a
surface applied aggregate having an appropriate colour and skid resistance. This product can be used either as a binder for a high friction surfacing system or permanent overlay marking system.
Composition
• Polyurethane pavement overlay material is tailored for specific conditions and application
• Products are covered by patents and licencing agreements
• May contain inorganic and organic colour pigments
Physical Properties
• Appearance – Coloured viscous liquids
• Density Part A 0.94 kg/l
• Density Part B 1.21 kg/l
• Odour – Characteristic, Part A – Aromatic, Part B – Musty / mouldy
• Flash Point Part B .190 ºC
• Auto-ignition Temperature Part B >260 ºC
• Insoluble in water
Performance Properties
• Shore Hardness Type D 50
• Tensile Strength (ASTM D638) >10 N/mm² after 24 hours
Durability
• Regarded as "long life" as far as "wear" is concerned
• Resistant to oil, petrol and de-icing salts
Compatibility
• Can be used on many types of surfaces.
Adhesion
• Can be applied to most pavement surfaces and textures
• Friable / highly absorbent surfaces such as porous concrete require priming.
Application Parameters
• Both components need to be thoroughly machine stirred. It is recommended that the
component containing the hardener is machine stirred
• Part A and Part B must be proportioned to the correct ration (product typically supplied in
packs which control ratio) and mixed
• Road and air temperatures should be in the range of 5 and rising up to a maximum of 40oC
• Recommended application rates of 1.35 to 2.8 kg/m2. Increased rates required for surfaces
having greater texture depths
NZRF Roadmarking Materials Guide – Modified Polyurethane Resin
• Use of specially built applicators which require accurate measuring devices and / or calibrated
• Hand applied binder requires serrated edged squeegee to control applied thickness
• Aggregate application by hand requires skill and experience
• Aggregate application rates need to be in excess of 6 kg/m² to ensure sufficient coverage /
embedment – no compaction is required.
Manufacturing Process
Testing of Physical Properties
• NZTA M 20, NZTA M 25 and AS 4049.4
Handling, storage & packaging
• Available in a variety of containers from 25 to 1500 kg
• Keep away from food and drink
• Store in cool dry place protected from rain, sun and moisture
• Protect from excessive heat or contamination from fuels, oils or greases.
Environmental Impacts
• Not regarded as hazardous to the environment
• Do not allow to enter drains, rivers and watercourses
• Refer to NZRF Roadmarking Note # 11 HSNO Regulations Emergency Management
Requirements - Guideline
Occupational Health & Safety Hazards
Part A
• Not regarded as a health or environmental hazard under current legislation Part B
• Harmful by inhalation
• Irritating to eyes, respiratory system and skin
• May cause sensitisation by inhalation and skin contact
Application Process
• Products and their application are covered by patents and licencing agreements
• The two part epoxy binder material cannot be applied on a wet surface, if the ambient and/or
surface temperature is below 5 ºC or above 40 ºC, or if the anticipated weather conditions would prevent the proper application of the surface treatment as determined by the manufacturer
• Existing surfaces need to be cleaned by use of mechanical sweepers, high pressure air or other
• All existing pavement markings and utilities are covered / protected prior to placement.
• All inadequately sealed joints and cracks greater than 5 mm are filled / sealed with the
manufacturers approved crack sealant.
• The two part modified epoxy binder components part A / part B are combined proportioned to
the correct ratio and mixed using a low speed high torque drill fitted with a helical stirrer
• The binder material is then spread by serrated edge squeegee such that it is uniformly
distributed over the pavement section to be treated and within the temperature range specified
• Operations need to proceed in such a manner that will not allow the epoxy material to chill,
set up, dry, or otherwise impair retention of the covered aggregate.
NZRF Roadmarking Materials Guide – Modified Polyurethane Resin
• Immediately after the binder is laid the aggregate is spread onto the binder at a rate in excess
of 6 kg/m². The placement of this material does not require any compaction.
• The treatment is allowed to cure in accordance with manufacturer recommendations,
approximately 3 hours at an ambient temperature of 24 ºC and rising
• The excess aggregate is removed by hand or suction sweeping before opening to traffic.
•
Process Monitoring Equipment
• Weighing devices
• Atmospheric condition measuring / monitoring devices
Post-Application Measuring Equipment
• Skid resistance testers
Test Methods
• Skid Resistance, refer also to Glass Beads and Angular Material
Quick Reference Safety Guide
• Part A not regarded as a health hazard
• Part B harmful by inhalation, irritating to eyes, respiratory system and skin, may cause
sensitisation by skin contact
• Skin Protection: Wear overalls, boots and gloves. Use chemical resistant face-shield where
splashing may occur. Use barrier creams
• Eye Protection: Use full face-shield / goggles while mixing.
• Inhalation: Part B - Use respirator, should be handled and used in well ventilated areas • General: In all cases of doubt, or where symptoms persist, seek medical attention
• Eye Contact: Make sure to remove contact lenses before rinsing. Rinse immediately with
water for at least 15 minutes and get medical attention immediately.
• Skin Contact: Wipe with absorbent paper disposable towels. Wash with plenty of soap and
water – do not use organic solvents. In case of dermatitis or if irritation persists, get medical attention.
• Inhalation: Move affected person to fresh air. Provide fresh air, warmth and rest, preferably in
a comfortable upright sitting position. Get medical attention.
• Ingestion: Do not induce vomiting. Immediately rinse the mouth with water. If swallowing
has occurred drink water in small sips. Seek medical attention promptly.
• Contaminated clothing and shoes: Remove immediately. Wash clothes before reuse, discard
contaminated footwear.
Recorded Environmental Hazards
Recorded Health & Safety Incidents
• Reports of dermatitis, and allergic dermatitis (Sensitisation) are common.
• Specialist sector groups interested in the safe use of epoxies established overseas
NZRF Roadmarking Materials Guide – Modified Polyurethane Resin
Related National / International Standard Specifications
• Products and their application are covered by patents and licencing agreements
• AS 4049.4
Useful References
• Caplin Group Ltd Coldgrip Technical Data Sheet
NZRF Roadmarking Materials Guide – Roller Applied Cement Based Coatings
39 Roller Applied Cement Based Coatings
General Description
• A compound consisting of white Portland cement and aggregates which when mixed with
water (or an emulsion) cures by hydration. Glass beads are injected prior to setting to provide retroreflectivity.
Composition
• Commonly provided as a two component mix under Licence
• Part A containing a blend of white Portland cement with selected aggregates and additives,
including glass beads
• Part B containing a blend of acrylic emulsion, water, titanium dioxide and other additives.
Physical Properties
• Part A – White powder - High miscibility in water
• Part B – Liquid emulsion - Soluble in water
• Bond strength (on concrete) 4.3 Mpa after 45 days.
Performance Properties
• Retroreflectivity: Dependent on bead type and application rate, typically in the range of 280 to
• Skid Resistance: Commonly formulated to have a minimum skid resistance of 45 BPN
• Note: The skid resistance of a marking material is not a fixed property for any given
formulation. It may vary considerably according to the temperature at which it is laid and will also vary throughout its life according to conditions such as traffic and weather.
Durability
• Regarded as a "long life" material as far as "wear" is concerned, expectancy greater than 8
years in roading environment.
Compatibility
• Can be used on most types of surfaces, bitumen, asphaltic concrete and Portland cement.
Adhesion
• Can be used on most types of surfaces, bitumen, asphaltic concrete and Portland cement.
Application Parameters
• Material should be well mixed
• Road and air temperatures should be greater than 5oC and rising. Poor bond may develop if
road temperature falls below 5oC
• Road surface needs to be clean and free from oils and greases. Primer tests need to be
conducted prior to application
• Sandblasting, waterblasting or wire brushing is recommended
• Substrate prepared by air-hand / mechanical brooming or use of high velocity / high pressure
air blowing to remove loose paint, dust and dirt.
Manufacturing Process
NZRF Roadmarking Materials Guide – Roller Applied Cement Based Coatings
Testing of Physical Properties
Handling, storage & packaging
• Part A supplied in 25kg bags
• Part B supplied in 10l containers
• Store in cool dry place protected from rain and moisture. Store Part A off the floor.
• Protect from excessive heat or contamination from fuels, oils or greases.
• Classified as Non Hazardous.
Environmental Impacts
• Materials are miscible in water, care must be taken to ensure that any spills or cleaning
materials do not enter or contaminate soil or waterways.
Occupational Health & Safety Hazards
• Skin irritation.
Application Process
• The two components are combined in a clean container and mixed with a slow speed drill
attached to an appropriate epoxy- mixing paddle
• Appropriate filler may be added to produce a mortar for filling or vertical surfaces
• In very hot conditions, the emulsion can be cooled with ice
• Material is rolled to suit the desired finish at a thickness of 2 to 3 mm
• Glass beads are injected using a special bead gun.
•
Process Monitoring Equipment
Post-Application Measuring Equipment
Retroreflectometer
Skid Tester
Test Methods
Quick Reference Safety Guide
• Part A contains cement dust resin that may cause inflammation of the lining tissue of the
interior of the nose, and inflammation of the cornea. Prevent contact with skin and eyes
• Part B contains emulsions that may cause skin irritation
• The wet mixture can dry the skin and cause caustic burns. • Skin Protection: Wear overalls and gloves. Use face-shield where splashing may occur. Use
barrier creams. Avoid continual contact with wet mix.
• Eye Protection: Use full face-shield / goggles while mixing or in dusty environments.
• Inhalation: Should be handled and used in well ventilated areas. In dusty environments use a
disposable respirator.
• If skin contact, wash immediately with soap and water.
• If eye contact flush with water for at least 20 minutes. Seek medical help.
• Remove contaminated clothing and shoes. Wash clothes before reuse, discard contaminated
NZRF Roadmarking Materials Guide – Roller Applied Cement Based Coatings
Recorded Environmental Hazards
Recorded Health & Safety Incidents
Related National / International Standard Specifications
Useful References
• Safety Data Sheets
Glow Line –Western Roads & Tac Pave.
• Western Roads Guidelines
NZRF Roadmarking Materials Guide - Spray Applied Cement Based Coatings
40 Spray Applied Cement Based Coatings
General Description
• A compound consisting of white Portland cement and aggregates which when mixed with
water (or an emulsion) cures by hydration. Glass beads are injected prior to setting to provide retroreflectivity.
Composition
• Commonly provided as a two component mix under Licence
• Part A containing a blend of white Portland cement with selected aggregates and additives,
including glass beads
• Part B containing a blend of acrylic emulsion, water, titanium dioxide and other additives.
Physical Properties
• Part A – White powder - High miscibility in water
• Part B – Liquid emulsion - Soluble in water
• Bond strength (on concrete) 4.3 Mpa after 45 days.
Performance Properties
• Retroreflectivity: Dependent on bead type and application rate, typically in the range of 280 to
• Skid Resistance: Commonly formulated to have a minimum skid resistance of 45 BPN.
• Note: The skid resistance of a marking material is not a fixed property for any given
formulation. It may vary considerably according to the temperature at which it is laid and will also vary throughout its life according to conditions such as traffic and weather.
•
Durability
• Regarded as a "long life" material as far as "wear" is concerned, expectancy greater than 8
years in roading environment.
Compatibility
• Can be used on most types of surfaces, bitumen, asphaltic concrete and Portland cement.
•
Adhesion
• Can be used on most types of surfaces, bitumen, asphaltic concrete and Portland cement.
Application Parameters
• Material should be well mixed
• Road and air temperatures should be greater than 5oC and rising. Poor bond may develop if
road temperature falls below 5oC
• Road surface needs to be clean and free from oils and greases. Primer tests need to be
conducted prior to application
• Sandblasting, waterblasting or wire brushing is of pavement surface is recommended
• Substrate must be prepared by air-hand / mechanical brooming or use of high velocity / high
pressure air blowing to remove loose paint, dus t and dirt.
Manufacturing Process
NZRF Roadmarking Materials Guide - Spray Applied Cement Based Coatings
Testing of Physical Properties
Handling, storage & packaging
• Store in cool dry place protected from rain and moisture. Store Part A off the floor.
• Protect from excessive heat or contamination from fuels, oils or greases
• Classified as Non Hazardous.
Environmental Impacts
• Materials are miscible in water, care must be taken to ensure that any spills or cleaning
materials do not enter or contaminate soil or waterways.
Occupational Health & Safety Hazards
• Dust
• Skin irritation
Application Process
• The two components are combined in a clean steel container and mixed with a slow speed
drill attached to an appropriate epoxy-mixing paddle
• Appropriate filler may be added to produce a mortar for filling or vertical surfaces.
• In very hot conditions, the emulsion can be cooled with ice
• Glass beads are injected using a special bead gun.
Process Monitoring Equipment
Post-Application Measuring Equipment
Retroreflectometer
Skid Tester
Test Methods
Quick Reference Safety Guide
• Part A contains cement dust resin that may cause inflammation of the lining tissue of the
interior of the nose and inflammation of the cornea. Prevent contact with skin and eyes
• Part B contains emulsions that may cause skin irritation
• The wet mixture can dry the skin and cause caustic burns. • Skin Protection: Wear overalls and gloves. Use face-shield where splashing may occur. Use
barrier creams. Avoid continual contact with wet mix.
• Eye Protection: Use full face-shield / goggles while mixing or in dusty environments.
• Inhalation: Should be handled and used in well ventilated areas. In dusty environments use a
disposable respirator.
• If skin contact, wash immediately with soap and water.
• If eye contact flush with water for at least 20 minutes. Seek medical help.
• Remove contaminated clothing and shoes. Wash clothes before reuse, discard contaminated
NZRF Roadmarking Materials Guide - Spray Applied Cement Based Coatings
Recorded Environmental Hazards
Recorded Health & Safety Incidents
Related National / International Standard Specifications
Useful References
• Safety Data Sheets
Glow Line –Western Roads & Tac Pave.
• Western Roads Guidelines
Introduction. 2
1
Materials covered. 3
Generic Headings . 5
Heading Content & Scope . 6
General Descriptions . 8
Cold-Applied Plastic . 9
Thermoplastic. 9
Self-Adhesive Tapes . 9
Raised Pavement Markers . 10
RPM Adhesive . 10
Glass Beads (Retroreflective Beads). 11
Retroreflective Elements. 11
Angular Material . 11
Modified Epoxy Resin. 11
Modified Polyurethane Resin. 12
Cement Based Coatings . 12
Roadmarking Material Classification Schemes . 13
New Zealand Transport Agency . 13
Australian Paint Approval Scheme (APAS) . 13
Waterborne Paint . 14
Polymer Modified Solvent Based Paint . 20
Chlorinated Rubber Modified Alkyd Paint . 25
Alkyd Paint . 30
10 Temporary / Removable Paint . 36
11 Cold-Applied Plastic . 41
12 Thermoplastic. 47
13 Pre-Formed Thermoplastic . 55
14 Permanent Tapes. 59
15 Temporary Tapes. 62
16 Permanent Non Retroreflective Raised Pavement Markers – Type B AS/NZS 1906.3 65
17 Permanent Retroreflective Raised Pavement Markers – Type A AS/NZS 1906.3. 67
18 Snow-Ploughable Retroreflective Raised Pavement Markers . 70
19 Roadstuds – Retroreflective Raised Pavement Markers . 73
20 Illuminated Raised Pavement Markers . 75
21 Temporary Pavement Markers . 78
22 Bituminous RPM Adhesive . 80
23 Two Component RPM Adhesive. 84
24 Self-Adhesive Pads . 87
25 Glass Beads . 89
26 High Index - Airport Beads . 93
27 High Index – Retroreflective Elements . 96
28 Quartz Angular Material. 98
29 Silica Friction Material . 101
30 Corundum Angular Material . 104
31 Alkyd Paint Thinners . 107
32 Chlorinated Rubber Modified Alkyd Paint Thinners . 110
33 Waterborne Paint Thinners . 113
34 Cold Applied Plastic Thinners . 116
35 Waterborne Paint Catalysts . 119
36 Benzoyl Peroxide . 121
37 Modified Epoxy Resin. 124
38 Modified Polyurethane Resin. 128
39 Roller Applied Cement Based Coatings . 132
40 Spray Applied Cement Based Coatings . 135
Source: http://nzrf.co.nz/techdocs/NZRF-Materials-Guide.pdf
SECCIÓN INVESTIGATIVA Revista Areté: ISSN: 1657-2513 2013, vol. 13 N° 1. 138-151 teNdeNcias de iNVestigaciÓN FoNoaudiolÓgica: eNcueNtRos NacioNales de iNVestigaciÓN Angélica María Lizarazo-Camacho2 y Diana Fique Ortega3 Fecha de Recepción: 1 de agosto de 2013 Fecha de Aprobación: 5 de octubre de 2013 Citar como: Lizarazo-Camacho, A. & Fique, D. (2013). Tendencias de la investigación fonoaudiológica: Encuentros Nacionales de Investigación en Fonoaudiología. Revista
Li et al. / J Zhejiang Univ-Sci B (Biomed & Biotechnol) 2011 12(12):983-989 Journal of Zhejiang University-SCIENCE B (Biomedicine & Biotechnology) ISSN 1673-1581 (Print); ISSN 1862-1783 (Online) www.zju.edu.cn/jzus; www.springerlink.com E-mail: [email protected] Gastric motility functional study based on electrical bioimpedance measurements and simultaneous electrogastrography*